
На сучасному етапі ведення землеробства наявність надійної та універсальної сівалки для висівання як дрібного, так і великого насіння не є примхою. Сьогодні ми маємо широкий спектр вирощуваних сільськогосподарських культур. Тому господарства відчувають гостру потребу в універсальних сівалках.
A з урахуванням того, що навіть у межах одного господарства ми можемо зустріти нині поєднання різноманітних схем обробітку грунту, то в такому разі універсальна машина для висівання (сівалка зернова) — неодмінна умова успішного господарювання. Іншим питанням є тенденція до широкого впровадження мінімальної, а то й нульової систем обробітку грунту, і відповідно до цього також потрібно використовувати універсальні машини ( сівалки зернові), які б були здатні проводити якісне висівання за таких умов.
Не менш значущим питанням є і строки висіву та можливість одночасного внесення мінеральних добрив, адже час на проведення висівання, особливо навесні, досить обмежений. Тож поєднання цих двох технологічних операцій скорочує не лише часові, а й виробничі витрати, адже не потрібно додатково використовувати техніку для внесення та загортання мінеральних добрив.
На теренах нашої держави можна зустріти різноманітні сівалки зернові та їхні комбінації для проведення висівання. В цьому матеріалі ми поговоримо про широкозахватні пневматичні комплекси, які славляться своєю продуктивністю та універсальністю щодо роботи за всіма технологіями обробітку грунту, а також можливістю висівати широкий спектр сільськогосподарських культур.
Попередній аналіз ринку України показує, що практично всі широкозахватні висівні комплекси — це машини ( сівалки зернові) канадського та американського виробництва. Для створення посівного ложа та закладання насіння у них використовують однодисковий сошник. Слід сказати, що в Україні також випускають сівалку зернову такого типу — на заводі «Червона зірка».
Тож що сьогодні пропонують заокеанські гості та чи насправді вони є настільки універсальними та продуктивними?
SDX 30 від Case IH - агрегат, перевірений часом
SDX 30 — це універсальний агрегат, який поєднує у собі передові світові технології. Сівалка зернова із шириною захвату 9 м працює разом із пневматичним бункером Precision Air 2230 загальним об’ємом 8105 л, причому останній складається із двох відсіків місткістю 5074 та 3030 л — для насіння та добрив відповідно. Оскільки поля мають різний рельєф, то для забезпечення надійного контакту сошників із грунтовою поверхнею конструкція сівалки має три секції — така комбінація створює висівний комплекс, який сьогодні завойовує все більше і більше прихильників на території України.
Особливістю сівалки зернової є унікальна висівна секція. Висівання проводиться за допомогою однодискового сошника Precisiom Disk, який має найбільший діаметр із пропонованих на ринку не тільки України, а й світу — 57,2 мм. Це забезпечує краще прорізування грунту із великою кількістю пожнивних решток, залишаючи при цьому чисту борозну для оптимального контакту насіння із грунтом.
Диски виготовлено зі спеціального сплаву, до якого входить бор, та підсилено завдяки збільшенню товщини, яка становить 6,4 мм, що сприяє подовшенню терміну їхньої служби. Відстань між дисками — 19 см — забезпечує висівання сільськогосподарських культур із такою самою шириною міжрядь.
Оскільки сівалка зернова може працювати за різними технологіями обробітку грунту, притискне зусилля регулюється у досить широких межах — від 110 до 230 кг на один сошник, що дає змогу працювати як по оранці (тиск на сошник становить 110–150 кг), так і по твердому необробленому полю із великою кількістю пожнивних решток (тиск — 180–230 кг). Крім того, унікальності агрегату також додає сама висівна секція, яка складається із сошника, скребка, що формує насіннєве ложе й запобігає проникненню до нього рослинних решток, прикочувального колеса, механізму регулювання глибини та тиску на грунт.
Висока якість борозни, у яку укладається насіння, досягається також завдяки спеціальному куту нахилу диска у горизонтальній та вертикальній площинах, який становить 5°. Крім того, таке рішення також знижує опір агрегату, що сприяє зменшенню потужності, необхідної для приводу трактора.
Борозна закривається за допомогою прикочувального колеса, яке може регулюватись по горизонталі відносно центра рядка на відстань від 0 до 52 мм із кроком 13 мм. Притискне зусилля прикочувального колеса регулюється у межах від 13,6 до 27,2 кг.
Бункер Precision AIR
Система дозування пневматичних бункерів компанії Case IH грунтується на запатентованій системі низхідного потоку, що забезпечує рівномірне розподілення посівного матеріалу між первинними насіннєпроводами. Для запобігання забиттю маси у бункері використано механічний змішувач-ворушилку, що також сприяє однорідності та рівномірності подавання матеріалу до висівних органів.
Для дозування різних за розміром культур компанія Cаse IH використовує чотири види дозувальних котушок, які забезпечують точне нормування висівного матеріалу як дрібнонасіннєвих культур, таких як ріпак, так і великонасінних бобових, а також дають можливість вносити будь-які дози добрив.
Challenger серії CH 9800 — незвична технологічність
Ця серія сівалок зернових являє собою високопродуктивний висівний комплекс, що здатен проводити якісне висівання за трьома системами обробітку грунту: традиційною, мінімальною та нульовою. Висівний орган цієї сівалки — однодисковий сошник діаметром 45,6 см. Висівання проводиться у здвоєні рядки із відстанню між ними 15 см, наступна пара рядків — на відстані 23 см. Особливістю такого висіву є забезпечення більшої площі живлення вирощуваної культури.
Крім цього, опційно сівалку зернову можна оснащувати додатковим сошником для внесення добрив у міжряддя завширшки 15 см. У такому разі ми отримуємо відстань між рядком рослини та рядком добив завширшки лише 7,5 см, що сприяє швидшому досягненню корінням рослини зони залягання добрив та швидшому їхньому засвоєнню, а відтак — кращому розвитку рослин. Два рядки насіння та рядок добрив прикочуються одним великим колесом.
У сівалці зерновій використано висівний апарат котушкового типу. Висівні комплекси серії СН 9800 придатні для сівби усіх сільськогосподарських культур з одночасним внесенням добрив або без нього. Робоча швидкість сівалки становить 14 км/год.
Сівалка зернова має досить просту систему регулювання глибини висіву: приміром, на 12-метровій сівалці воно забезпечується із чотирьох точок. Сила прикочування та тиск на сошник регулюються із трактора, що полегшує роботу оператора та підвищує продуктивність висівного комплексу.
Ширина захвату залежно від обраної моделі — від 9 до 18 м.
Сівалки зернові серії СН 9800 агрегатуються із пневматичними бункерами СН 9920-280, 9920-335 та 9930-525, які вирізняються збільшеною місткістю для насіння та добрив. Крім того, слід сказати, що перші дві моделі — об’ємом 10 та 12 м3 відповідно — мають два відділення для насіння та добрив у пропорції 60/40. Остання модель — місткістю 18 м3 і має три відділення: об’ємом 5, 6 та 7 м3. Крім того, бункер СН 9930-525 місткістю 18 м3 має повітряну систему із двома повітряними потоками.
Пневматичні бункери від Challenger характеризуються підвищеною надійністю та довговічністю, адже всі частини бункера, що контактують із насінням та добривами, виготовлено із нержавіючої сталі.
Bourgault 3720 — новачок з амбіціями
Канадський виробник сільськогосподарської техніки, компанія Bourgault, нещодавно представила нову модель висівних комплексів — Bourgault 3720.
Bourgault
Висівний комплекс оснащується однодисковим робочим органом, діаметр якого становить 521 мм. Відстань між дисками, і як наслідок — ширина міжряддя культур, які висівають, може становити 19, 25 і 30 см. Висівний диск сівалки встановлено під кутом 10° у вертикальній площині та 5° — у горизонтальній, що в поєднанні із великим діаметром дає змогу працювати на полях із великою кількістю пожнивних решток. Особливість висівної секції сівалки зернової моделі 3720 — відмінне забезпечення стабільності глибини загортання насіння і можливість повного копіювання рельєфу поля, що робить конструкцію зручною для використання у будь-яких умовах. Крім того, ви можете бути впевненими, що цей агрегат якісно працюватиме на всіх полях незалежно від наявності пожнивних решток та стану поля щодо вологості грунту. Притискне зусилля на сошник регулюється дистанційно (із кабіни трактора) і перебуває в межах від 32 до 104 кг — за плаваючої конфігурації сошників та 45–150 кг — за блокування очисного колеса, при цьому глибина обробітку буде встановлюватися і контролюватися лише прикочувальним колесом.
Завдяки опції блокування кожного другого сошника, висівну систему моделі 3720 із міжряддям 19 і 25 см можна використовувати для висіву просапних культур із міжряддям 38 і 51 см відповідно.
На сівалці зерновій можливе також встановлення системи MRB — для внесення мінеральних добрив у міжряддя культури, яку висівають.
До то ж із 2016 р. виробник пропонує функцію автоматичного контролю сошників, що забезпечує автоматичне їхнє підіймання та опускання на розворотах. Тепер для розвороту агрегату на краю поля операторові достатньо лише натиснути на кнопку автоуправління. Функція автоматичного контролю сошників зменшує кількість необхідних операцій, контрольованих оператором. Така система входить до стандартної комплектації моделей 3320 і 3720 із бункерами серій 6000 і 7000, оснащеними системою автоматичного відключення секцій ASC, які почали випускати із 2016 р. Для попередніх моделі — 3310, 3320, 3710 і 3720 із бункерами, оснащеними системою X30 Apollo, виробник пропонує додаткову опцію — комплект для установки функції автоматичного контролю сошників.
Бункери
Українським аграріям виробник пропонує пневматичні бункери Bourgault серії 6000 ємністю від 9,8 до 18,9 л. Вони можуть мати чотири секції, тобто працювати окремо з чотирма незалежними продуктами.
Дозувальна система PDM Plus є серцем пневматичних бункерів цієї серії. Основою таких дозувальних систем є дозувальні шнеки, виготовлені із пластику високої міцності або металу, які у поєднанні з ідеально дібраними до них калібрувальними діафрагмами гарантують високу точність вимірювання продукту і низькі витрати на обслуговування навіть за роботи із проблемним продуктом, таким як надмірно вологе насіння і певні види добрив.
Система контролю та регулювання норми висівання CRA дає змогу регулювати кількість внесення продукту для кожного дозатора бункера із кабіни трактора. Електричний варіатор, установлений на кожній трансмісії, дистанційно регулює норму внесення продукту після його активації оператором. Для зручності налаштування норми висіву під час калібрування другий блок управління розташовано на бункері.
John Deere 1890 — надійний помічник
Ще один американський виробник сільськогосподарської техніки, компанія John Deere, пропонує широкий модельний ряд широкозахватних комплексів. Серед них можна виділити пневматичну сівалку 1890, яка має можливість працювати за трьома системами обробітку грунту.
Сівалка 1890 поставляється у п’яти конфігураціях із шириною захвату від 9,1 до 18,3 м. Крім того, що вона може працювати за всіма технологіями, основне її призначення — це роботи на полях із великою кількістю пожнивних решток.
На сівалці встановлено сошники John Deere 90-ї серії. Цей сошник має конструкцію одинарного диска, який установлено під кутом 7°, що дає змогу працювати на полях зі значною кількістю пожнивних решток. А притискне зусилля на рівні до 181 кг забезпечує рівномірне заглиблення сошників на твердих грунтах. Висівний башмак на цих сошниках розміщено у центрі ступиці, насіння переміщується і укладається на дно ущільненої борозни для забезпечення найкращої схожості. Висівні башмаки задля більшої надійності виготовлено із чавуну. Насіння «уловлюється» нейлоновими насіннєвими відбивачами, які спрямовують його на дно борозни, забезпечуючи надійний контакт із грунтом. На моделі 1890 також можливе встановлення висівного башмака, виготовленого із хромистого сплаву, який має втричі більший термін служби порівняно із чавунним. Надзвичайно важливим є розташування висівних башмаків. На сошниках 90-ї серії вони встановлені по центру диска. Переваги такої конструкції полягають у тому, що забезпечуються краще заглиблення сошника і контроль глибини.
Пневмопричіп 1910 з об’ємом бункерів від 6872 до 15 153 л пропонують у конфігурації, що передбачає можливість агрегатування між трактором та сівалкою (для забезпечення кращої тяги) або позаду сівалки (для кращого контролю висіву). Максимально бункер пневмопричепа може мати три відсіки — для роботи з різними матеріалами. Як опцію до пневмопричепа компанія-виробник пропонує завантажувач насіння продуктивністю 1400 л/хв, виготовлений за конвеєрним типом, що забезпечує бережне ставлення до зерна.+
Котушкова система дозування насіння та добрив сприяє високій точності висіву за широкого діапазону висівної норми — від 2 до 567 кг/га. Для цього потрібно просто замінити висівну котушку, яка відповідатиме вимогам щодо потрібної норми висіву.
Бункери можуть оснащуватися ручною та дистанційними (із кабіни трактора) системами налаштування норми висіву.
Компанія Bourgault пропонує широкий вибір посівних комплексів, що володіють унікальними характеристиками і водночас виготовлених за принципом надійності і простоти.
|
|
|
|
|
| ||||||
|
|
|
|
|
| ||||||
|
|
|
|
|
| ||||||
|
|
|
|
|
| ||||||
|
|
|
|
|
| ||||||
|
|
|
|
|
| ||||||
|
|
|
|
|
| ||||||
|
|
|
|
|
|
Передова запатентована паралелограмна конструкція важелів сошника забезпечує точне закладення насіння зі збереженням постійної глибини при зміні контуру поля. Рівномірне посівне ложе гарантує однорідні сходи навіть у важких польових умовах.
Мінімальне порушення ґрунтового шару дисковими робочими органами під час посіву дає максимальні переваги в посушливих умовах. З агрегатом моделі 5925 Ви без проблем можете проводити посів по високій стерні і гарантовано розділяти насіння і добрива при посіві за один прохід, використовуючи систему MRB. Дискові посівні комплекси демонструють неперевершені результати в посушливих районах, де збереження ґрунту і утримання вологи є пріоритетними завданнями.
Модель 3320 SE пропонує ефективну і перевірену конфігурацію для сільгоспвиробників, що вимагають посівний агрегат з незалежним
копіюванням контуру поля на кожному сошнику і який можна використовувати у всіх польових умовах.
Модель 3320 QDA – єдиний посівний комплекс з незалежним копіюванням рельєфу кожним сошником, який надає можливість швидкого (протягом декількох хвилин) регулювання глибини посіву по всіх сошниках.
У компанії Bourgault довга історія виробництва посівних агрегатів, продовження представлено посівним комплексом анкерного типу моделі 5810. Поєднавши перевірені практикою характеристики попередніх моделей з новими технологіями Bourgault запропонувала сучасному ринку вдосконалену модель традиційного посівного комплексу.
Багатоцільовий агрегат моделі 8910 один з найбільш популярних знарядь для господарств, що виконують комплекс технологічних операцій, як в процесі передпосівної підготовки ґрунту, так і під час проведення посіву. Простий дизайн, надійна конструкція і чудові характеристики проходження пожнивних залишків зробили даний агрегат універсальним для виконання різних сільськогосподарських операцій.
Чизельний культиватор оснащений посиленим причіпним пристроєм плаваючого типу. Велика відстань між стійками, розташованими на рамі в чотири ряди, гарантує відмінне проходження пожнивних залишків. Жорстка конструкція рами і використання посилених пружинних зчіпок сошників та робочих органів BTT серії 410 забезпечує рівномірне проникнення навіть на самих важких ґрунтах.
Пружинні борони дозволяють рівномірно розподіляти пожнивні залишки з максимальним покриттям площі, створюючи мульчуючий шар для утримання
вологи і захисту сходів. Середні борони можна також використовувати для перед або післяпосівного боронування без ризику пошкодження насіннєвого ложа.
Широко використовуються для боротьби з бур’янами у фазі «білої ниточки» на парових ділянках.
Спіральні катки є ідеальним знаряддям для тих господарств, які бажають додати механічний спосіб боротьби з бур’яном і культиваторну обробку до технології посіву за один прохід. дані катки не тільки виконують функцію прикочування, але і вирівнюють поверхню ґрунту, забезпечуючи рівномірну глибину загортання обробленої поверхні після проходу стрілчастої лапи. Можуть мати ширину захвату від 7,6 до 18,2 м, яка підбирається під ширину захвату основного ґрунтообробного знаряддя.
Унікальні характеристики зернового бункера-накопичувача GC1200 дозволять у рази підвищити ефективність збирання врожаю. Практика показує, що використання одного бункера-накопичувача GC1200 на 2-3 комбайна під час збирання врожаю по ефективності замінює ще один комбайн. Під час посівних робіт бункер може використовуватися для завантаження посівних комплексів.
ГРУНТООБРОБНІ АГРЕГАТИ
|
|
|
|
|
| ||||||
|
|
| |||||||||
| 5 | 3 |
| ||||||||
|
|
|
|
|
| ||||||
|
|
|
|
|
| ||||||
|
|
|
|
|
| ||||||
|
|
|
|
|
|
Галерея – Широкозахватні посівні комплекси BOURGAULT
Посівна техніка
John Deere пропонує широкий модельний ряд посівної техніки, що забезпечує високу ефективність і швидкість виконання робіт. У портфоліо представлені механічні та пневматичні сівалки. Усі вони гарантують високоточний посів, що досягається за рахунок спеціалізованих конструктивних рішень (систем дозування насіння, Section Command та ін.).
Переваги техніки
Завдяки культиваторній конструкції деякі сівалки за один прохід можуть виконати не тільки посів, але й передпосівну обробку. Знаряддя використовується для посіву бобових, зернових, кормових, олійних культур та ін. Багато моделей посівної техніки John Deere є широкозахватними, завдяки чому можна швидко обробити поле з мінімальною кількістю проходів (відповідно, і мінімальними витратами палива). В залежності від моделі, сівалки можна вносити добрива як в основну борозну разом з насінням так й в окрему за допомогою окремих сошників та другого контуру пневматичних трубопроводів.
Сівалки John Deere дозволяють досягти встановленої стабільної глибини закладення насіння, що забезпечує рівномірність сходів, а також створює передумови для отримання хорошого врожаю. Міжрядкова відстань (наприклад, 19 або 15 см) підбирається в залежності від різновиду рослин.
Зручне управління.
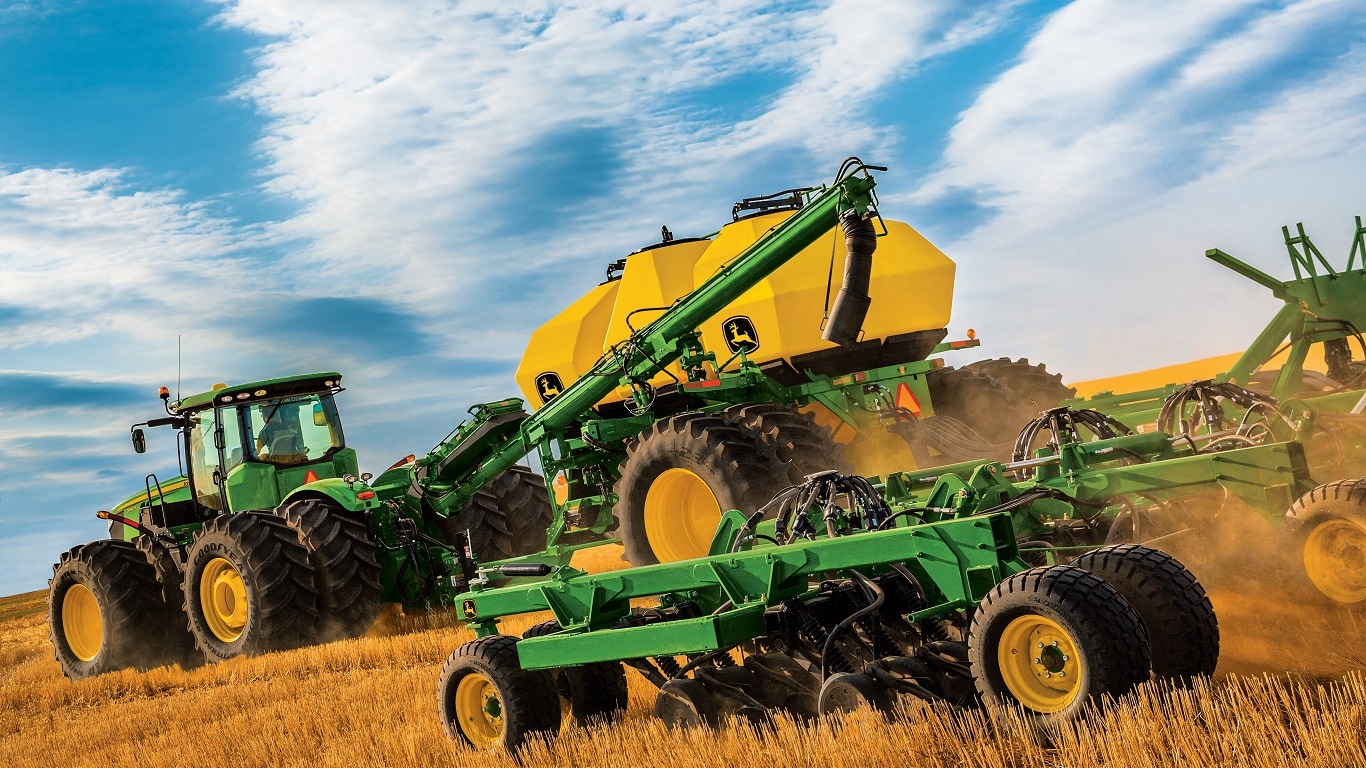
Пневматична сівалка
Оптимальні рішення для самих різних умов посіву: сівалка 1830 з гнучкою рамою і сошниками анкерного типу вирішить проблему посіву у вологий грунт; пневматична сівалка 730 підрізає бур'яни, культивує, вносить добрива і висіває за один прохід; модель 1890 завдяки сошнику 90 серії ефективно розрізає пожнивні залишки і забезпечує найбільш сприятливі умови для посіву за нульовою технологією. Широкий вибір варіантів завантажувача насіння моделі 1910 дозволить скласти оптимальний посівний комплекс для досягнення найкращих результатів:
Пневматична сівалка 730LL
Пневматична сівалка 1830
Пневматичні сівалки P500
Пневматичні сівалки N500
Пневматичні сівалки N500F
Пневматичний бункер 1910
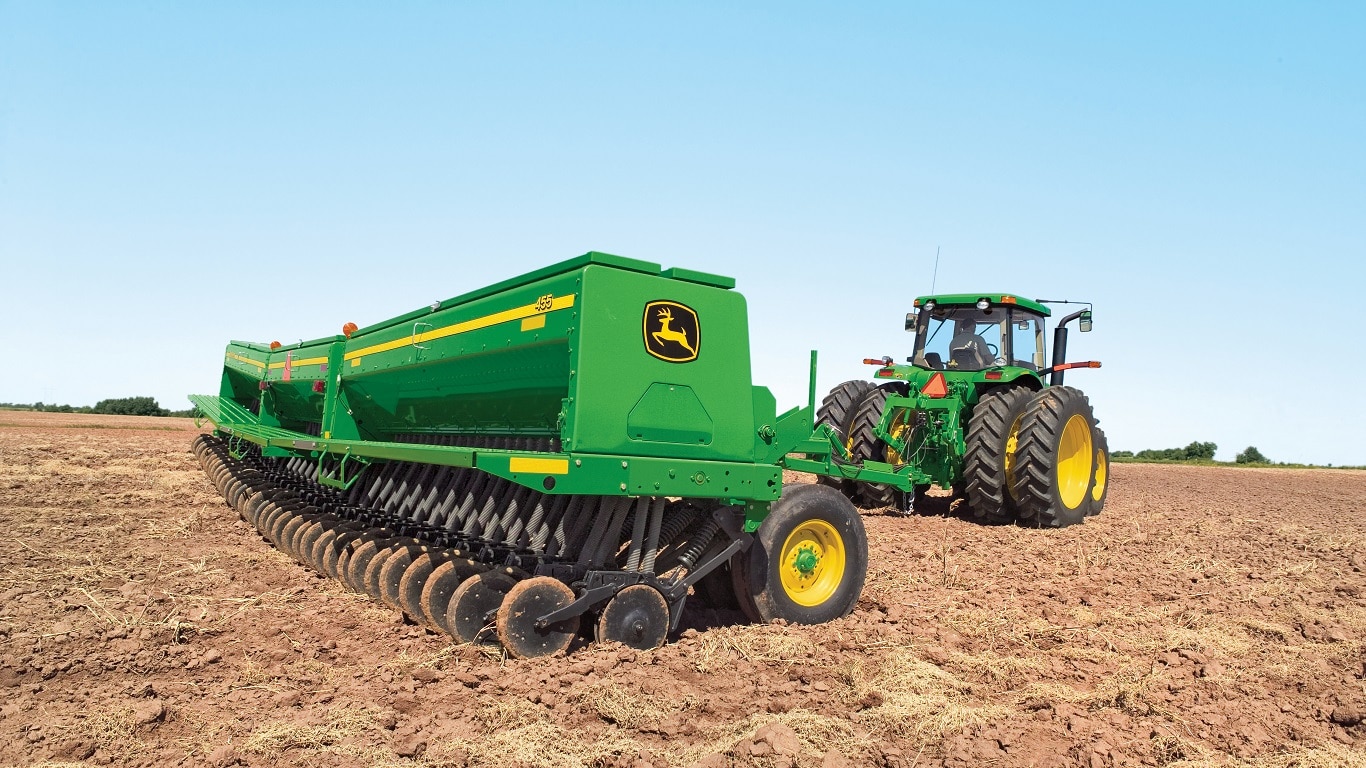
Механічні сівалки
Механічні сівалки John Deere 1590 та 455 пропонують виключно широкі можливості: робота за традиційною, мінімальною і нульовою технологією, посів зернових, бобових культур і трав:

До сучасної посівної техніки сьогодні висувається низка агротехнічних вимог. Цим вимогам повністю відповідають посівні агрегати виробництва компанії LEMKEN (Німеччина). Повний спектр посівної техніки цього виробника досить широкий – він налічує кілька десятків моделей і модифікацій із різноманітними базовими параметрами: шириною захвату, об’ємом бункера, можливістю одночасного внесення мінеральних добрив тощо. Для ґрунтово-кліматичних і організаційно-господарських умов України більше за інші підходять агрегати «Компакт-Солітер 9».
Нова посівна комбінація «Компакт-Солітер 9» виготовляється з робочою шириною захвату 3, 4 та 6 м і демонструє високу якість та ефективність сівби у різних виробничих і ґрунтово-кліматичних умовах роботи.
При вирощуванні зернових культур і ріпаку зростає потреба у посівних комбінаціях, які дають змогу вносити мінеральні добрива. Тому, окрім наявної чотириметрової посівної комбінації, компанія LEMKEN вивела на ринок більш продуктивний агрегат із шириною захвату шість метрів та можливістю внесення гранульованих мінеральних добрив у міжряддя. Застосовуючи такий посівний агрегат як за традиційної, так і консервуючої технології ґрунтообробки, можна забезпечити відмінний розвиток молодих рослин.
Для підвищення ефективності сівби та адаптації до різноманітних умов використання посівні комплекси «Компакт-Солітер» можуть постачатися як з короткою дисковою бороною «Геліодор», так і з ротаційною «Циркон». Напівсферичні зубчасті диски компактної дискової борони «Геліодор» забезпечують інтенсивне перемішування та рівномірне вирівнювання ґрунту. «Геліодор» складається із двох рядів зубчастих напівсферичних дисків діаметром 465 мм і товщиною 5 мм, які закріплені індивідуально. Для збільшення інтенсивності обробітку напівсферичні диски з міжряддям 125 мм розташовані у два ряди зі зміщенням. Глибина ходу дисків регулюється гідравлічно, а за допомогою шкали можна контролювати встановлену глибину обробітку.
Для високопродуктивної сівби навіть у найважчих виробничих умовах посівна комбінація «Компакт-Солітер» із шириною захвату 6 м може оснащуватися ротаційною бороною «Циркон 10», яка забезпечує поверхневий, швидкий та інтенсивний, або глибокий інтенсивний обробіток. Такі параметри роботи ротаційної борони, як глибина обробітку, частота обертів роторів, положення робочих органів і поступальна швидкість руху налаштовуються індивідуально. Таким чином, за один робочий прохід готується ідеальне посівне ложе.
Комбінація «Компакт-Солітер» обладнана дводисковими сошниками OptiDisc, які відмінно працюють як на стерні, так і на мульчованому полі. Такі сошники із напрямними роликами глибини, що мають гумову шину, навіть за нерівної поверхні ґрунту точно висівають насіння на однакову глибину. Напрямна подвійного диска залишається на постійній глибині на різних ґрунтах і за підвищених швидкостей. Притискний ролик придавлює насіння, що забезпечує оптимальну глибину його загортання незалежно від вологості ґрунту, створюючи таким чином належний контакт насіння із ґрунтом, що є передумовою для дружних сходів і високих урожаїв.
Оригінальною є автоматична система регулювання тиску на сошники, яка застосовується на посівних комбінаціях «Компакт-Солітер». Ця система забезпечує постійну глибину загортання насіння незалежно від зміни ґрунтових умов (типу ґрунту, його вологості, механічного складу тощо) та швидкості руху посівного агрегату. Серійне центральне механічне налаштування тиску (до 45 кг), що діє на дводискові сошники OptiDisc з роликом ведення глибини, створює умови для цього. За необхідності працювати з більшим, до 70 кг, тиском можна замовити гідравлічне регулювання.
Особливістю паралелограмної підвіски сошників на «Компакт-Солітер» є те, що, на відміну від конкурентів, паралелограм на машинах LEMKEN не є абсолютно жорстким у плані кінематики. Завдяки цьому поверхню ґрунту копіює спочатку сошник, а вже потім – прикочувальний коток, що дає змогу абсолютно точно дотримувати встановленої глибини сівби.
У варіанті комбінації посівного модуля з дисковою бороною «Геліодор» ґрунт під посів готується дисками борони. За ними розміщені дискові сошники для внесення мінеральних добрив діаметром 400 мм. Вони точно розподіляють добрива на встановлену глибину внесення. Максимальний тиск сошників на ґрунт може становити 150 кг. Далі встановлено колісний прикочувальний коток зі зміщеним розташуванням коліс діаметром 1097 мм, який забезпечує необхідне ущільнення ґрунту перед сівбою та виконує транспортну функцію; великий діаметр коліс, а також їх розміщення в шаховому порядку зменшують потребу в тяговому зусиллі. Більше того, кожна триметрова секція може копіювати рельєф поля незалежно від іншої. Це забезпечує постійну якість роботи за всією шириною агрегату. Велика площа контакту шин забезпечує відмінну роботу навіть у важких умовах.
Зміщення коліс сприяє їх кращому самоочищенню, що гарантує високу якість сівби навіть в умовах підвищеного зволоження. Ширину шин вибрано таким чином, щоб кожна з них ущільнювала ґрунт для трьох сошників у разі сівби з міжряддям 16,7 см. Для додаткового попереднього ущільнення посівних рядків перед дводисковим сошником OptiDisc комбінація «Компакт-Солітер» може обладнуватися вбудованим трапецієвидним прикочувальним котком; у такій комплектації сівалка автоматично має систему розподілення тиску в процентному співвідношенні між шинним і трапецієвидним котками. Тобто залежно від умов на полі (типу ґрунту, його вологості, механічного складу тощо) тиск може або на всі 100% подаватися на один із котків, або рівномірно розподілятися між двома котками чи змінюватися в будь-якому співвідношенні з кроком регулювання 10%. Регулювання відбувається із кабіни трактора в робочому комп’ютері сівалки.
Посівна комбінація «Компакт-Солітер 9/600 K HD» має бункер місткістю близько 5000 літрів, розділений на два відсіки. Рухомі перегородки бункера дають змогу легко змінювати розміри відсіків для насіння та добрив у співвідношеннях 40:60, 50:50 або 60:40%. Якщо застосування мінеральних добрив при сівбі не планується, то весь бункер можна заповнювати посівним матеріалом.
Для якісної сівби різного за розміром насіння передбачено використання шести різних висівних котушок, які розміщені на висівному валу. Завдяки оригінальній конструкції дозувальних валів для насіння та добрив, які мають електричний привід, норма висіву кожним із валів встановлюється незалежно один від одного. Завдяки цьому діапазон висіву насіння можна безступінчасто змінювати у межах від 1,5 до 500 кг/га, а мінеральних добрив – від 50 до 600 кг/га.
Залежно від ширини захвату посівні комбінації «Компакт-Солітер» можуть мати від двох до чотирьох дозаторів. Управління дозаторами відбувається з використанням електронного блока Solitronic, а за наявності опції можна включати або відключати подачу насіння за допомогою гідравліки. Блок Solitronic забезпечує калібрування сівалки на задану норму висіву.
Посівний матеріал від бункера до висівних робочих органів подається за допомогою стисненого повітря. З цією метою на сівалках встановлено компресор із гідравлічним приводом. Оберти компресора можна змінювати плавно, незалежно від частоти обертання колінчастого вала двигуна. Потрібної швидкості обертання можна досягти навіть за мінімальних обертів двигуна трактора, а коливання частоти обертання колінчастого вала двигуна не впливають на число обертів компресора.
Однією з останніх розробок фірми є можливість приєднати за допомогою ISOBUS інтерфейсу просапну сівалку LEMKEN Azurit. В такому разі висівний брус замінюється на нову сівалку, а бункер «Компакт-Солітера» використовується як ємність для добрив. Отже, ця посівна комбінація є універсальною посівною машиною в будь-якому господарстві.
Розрахунок схем створення технологічної колії.
Зернові культури становлять понад 70% всіх продуктів харчування людства. Пріоритет їх вирощування у всьому світі зумовлений транспортабельністю, високою продовольчою та кормовою якістю та можливістю зберігати упродовж кількох років. Запаси зерна – є стратегічним запасом продовольства у будь-якій країні.
У світі зернові займають величезні площі: пшениця – 216 млн. га, рис- 146,5, кукурудза-131,5, ячмінь-73,5 млн. га.
Найпоширенішою зерновою культурою в Україні є озима пшениця, посіви якої займають залежно від року 6,4-7,3 млн. га землі. До 90% площ її зосереджено у степовій та лісостеповій зонах і лише близько 10% – у поліській. Друге місце за площами посіву належить ячменю ярому, який в окремі роки висівають на 3,5-4 млн. га. Вирощують його, як і озиму пшеницю, переважно в Степу й Лісостепу. Третє місце за зерновою кукурудзою, посівні площі якої часто перевищують 1,5-2,0 млн. га і розміщені переважно у степовій та лісостеповій зонах. Інші зернові злакові культури (жито, тритикале, овес, яра пшениця, озимий ячмінь, просо, рис, сорго) висівають в Україні на площі, яка в різні роки коливається в межах 2,5-3,5 млн. га.
Озиме жито, тритикале і овес поширені переважно на Поліссі та в Лісостепу; озимий ячмінь – в районах Степу; просо – в усіх зонах України; кукурудза на зерно – в Степу й Лісостепу; рис і сорго – у степових районах.
Досить давно в теорії, а тепер вже й на практиці було зроблено кардинальний висновок, що немає іншого шляху вирішення продовольчої проблеми світу і будь-якого окремого його регіону, як інтенсифікація рослинництва. В умовах зростаючого науково- технічного потенціалу розвинутих країн досить швидко і обґрунтовано був знайдений, а тепер уже й реалізований, головний напрямок такої інтенсифікації – це інтенсивні технології вирощування всіх сільськогосподарських культур, у поєднанні та на фоні загальних прогресивних систем землеробства.
Рівень урожайності головних зернових культур світу – пшениці та рису, навіть у третіх країнах світу, подвоївся.
Інтенсивні технології спираються на використання сучасної техніки і жорстку експлуатацію обмежених або непоновлюваних ресурсів продуктивності, локалізацію технічних заходів і зусиль на окремо взятих культурах при вузькій спеціалізації господарств. Але потрібно сказати, що ці принципи не враховували екологічний стан при застосуванні цих технологій, основним завданням яких було збільшення виробництва продукції тієї або іншої культури і рослинництва, в цілому за рахунок інтенсивних факторів.
При врахуванні екологічної нешкідливості інтенсифікації рослинництва та його інтенсивних технологій, за відношенням до всіх елементів навколишнього середовища, яким є грунт, з усіма його процесами життєдіяльності та максимальної продуктивності, були запропоновані нові поняття інтенсивних технологій типу: біологічних, біологі- зованих, вологозберігаючих, ґрунтозахисних, ресурсозберігаючих, енергозберігаючих, матеріалонемістких, зональних, адаптивних тощо. Тому рослинництво має бути інтенсивним за рахунок найбільш повного використання унікальної здатності рослин до біологічної акумуляції космічних (сонячна радіація, клімат) факторів продуктивності, в поєднанні з такою ж самою ефективністю використання геологічних (ґрунт, водні ресурси) факторів. Тут мова може йти про інтенсивні агроекосистеми зон або регіонів, а в масштабах конкретних господарських формувань, де фактично і здійснюються інтенсивні технології, перш за все про інтенсивні агроландшафти. Одним з важливих аспектів підвищення реалізації біологічної продуктивності агро- ландшафтів є інтенсифікація рослинництва, в межах і на основі природозахисних систем землеробства з контурно-меліоративною організацією території повсюди, в тому числі й в основних рослинницьких районах України.
Зокрема в США, Німеччині, біологічне землеробство та рослинництво навіть при найкращих системах їх ведення менш продуктивні, ніж інтенсивні технології (на 25–30% і більше). Одержана при цьому продукція дорожча. До того ж, і за правильно застосованих інтенсивних технологій, з використанням оптимізованих хімічних заходів забезпечення продуктивності, є можливість підтримувати в основній продукції рослинництва вміст екологічно шкідливих речовин на рівні, що не перевищує медично обгрунтованих нормативів. З цього погляду біологічні системи землеробства та біологічні технології рослинництва можуть становити абсолютну альтернативу інтенсивним, хіба що стосовно продуктів дитячого харчування та елітарного попиту. Тому основним напрямом підвищення продуктивності рослинництва має стати поєднання найкращого, що є в надбаннях як в інтенсивних, так і в біологічних технологіях. Саме такий напрям одержав назву біологізовані інтенсивні технології.
Зернові культури можуть бути найкращим модельним об'єктом висвітлення питань максимального використання всіх складових потенціалу інтенсивних технологій, у поєднанні з найширшою їх біологізацією, як оптимального шляху зростання виробництва екологічно чистої продукції.
Науково обгрунтоване вирішення питання оптимізації умов та параметрів формування інтенсивних посівів зернових культур спирається на закон незамінності та рівнозначності факторів продуктивності рослин, взаємодію цих факторів від простої до складносумарної (синергетичної). Максимально сприятливо і максимально повно повинні створюватися і використовуватися ті умови, фактори і параметри інтенсивних посівів, що за рахунок переважно природних дешевих і відновлюваних джерел забезпечують найвищий рівень продуктивності посівів, прийнятий рівень екологічної чистоти та споживчих якостей продукції, працюють на енергозбереження антропогенних за походженням енергоресурсів.
Через удосконалення структури посівів зернових культур у зонально-регіональних межах можна створити, а потім і реалізувати, найвищий біологічний потенціал зернового господарства в кожній зоні або регіоні. Здійснити пошук найбільшої відповідності біологічних потреб та можливостей тієї або іншої культури щодо агрокліматичних і грунтових умов (адаптації'). Під впливом підвищеної уваги до інтенсифікації виробництва озимої пшениці, а в певній мірі й під впливом переважного забезпечення її інтенсивними сортами, вона поширилася в необгрунтованих масштабах в усіх зонах країни. В результаті значну частину зерна озимої пшениці використовують на корм худобі, хоча вона поступається за кормовою щнністю продукції іїшіих зернових. Тому скорочення посівів озимої пшениці до оптимальних лише на задоволення харчових потреб дасть змогу значно розширити площі зернофуражних культур. Так, на
Поліссі, це насамперед, стосується тритикале. Збільшення площ потребує також ячмінь, у тому числі озимий, на півдні країни та в деяких західних лісостепових районах. Має зайняти належне місце в структурі зернового господарства і виробництво зерна кукурудзи, яке в країнах розвинутого тваринництва є основною складовою частиною високоенергетичних кормових раціонів.
За сучасних інтенсивних технологій та зрослого потенціалу інтенсивних сортів цих культур, така заміна не призведе до зменшення валового виробництва зерна, а за рахунок більш якісної та відповідної до потреб тваринництва зернокормової продукції в цілому, може значно підвищити рівень інтенсифікації цієї галузі рослинництва.
На зонально-регіональному рівні потрібно здійснювати регулювання водного балансу територій (зрошення, осушення, залісення), меліоративне поліпшення не тільки природно кислих і засолених грунтів, але й тих, де тепер уже значно погіршилася їх родючість під впливом все більш кислих атмосферних опадів та науково необгрунтованого використання мінеральних добрив, шляхом застосування адаптованих вологозберігаючих та грунтозахисних систем землеробства.
Оптимізація основних природних умов формування високопродуктивних посівів зернових культур у грунтозахисних контурно-меліоративних системах землеробства, дає можливість підвищити виробництво зернових за показниками їх врожайності на 20-30%. Загальнооптимізаційні заходи цієї системи супроводжуються скороченням застосування хімічних засобів для інтенсивного вирощування зернових та інших культур і поліпшують екологічну чистоту продукції.
Загальний рівень біокліматичного потенціалу та його складові забезпечують досить високий рівень інтенсивного рослинництва.
Бездефіцитним, практично для найвищого рівня інтенсифікації виробництва зернових, є потенціал сонячної радіації як з точки зору теплового балансу, так і балансу фотосинтетично-активної радіації, а також нормального розвитку рослин. Лише на півдні та на південному сході України в значному дефіциті є вологозабезпечення, та й то на рівні зон, так званого, ризикованого землеробства, а не жорсткої посушливості. Ґрунти країни, навіть в наявності природно менш родючих грунтів Полісся, західних та передгірних районів, в цілому забезпечують Україні чільне місце серед найродючіших регіонів світу.
Проте все це лише передумови інтенсифікації. Самі ж її умови та наслідки їх реалізації створюються і здійснюються лише у відповідно сформованих посівах.
На біолого-рослинницькому та агротехнічно-технологічному рівнях формування інтенсивних посівів зернових культур передбачається оптимізація досить широкого спектра умов, факторів і параметрів, що в сукупності та взаємодії забезпечують високу продуктивність.
У сучасному науковому забезпеченні обґрунтованим є розгляд і здійснення підходу до оптимізації умов формування інтенсивних посівів за допомогою концепції ідеального типу (ідеатипу) рослини та ідеального типу посівів. Концепція ідеатипу або синонімічно ідеамоделі передбачає оптимізацію практично всіх умов та факторів інтенсифікацій продукційного процесу рослини та її біологічних (фізіологічних, біохімічних, біометричних) параметрів, що забезпечують їх повне використання і відтворення на рівні кінцевої продуктивності посіву (сукупності ідеальних рослин). Зрозуміло, що на практиці важко або навіть неможливо в повній мірі створити і забезпечити функціонування саме ідеатипів рослин і посівів, але вже сам процес можливості наближення до них не може не стимулювати прагнення до цього.
У структурі створення і забезпечення ефективного функціонування ідеатипу посівів зернових культур найважливішою складовою є генетично обумовлений потенціал сорту з усіма його властивостями щодо продуктивності та можливостей використання умов інтенсивного продукційного процесу.
В своєму розвитку зернові знаходяться до виходу в трубку або утворення стебла (ВВСН 10 ... 29і*) у вегетативному періоді розвитку, від початку виходу в колос до кінця цвітіння (30.. .69) – в генеративному і від першої стадії дозрівання до повної стиглості і (71...92) – в репродуктивному періоді. Вегетативний період співпадає з системним ростом вегетативної маси, генеративний період – із ростом продукту, тобто зерна. Окремі стадії, з точки зору утворення урожаю, мають різне значення.
Потенціал продуктивності нових інтенсивних сортів, що є біологічним за своєю природою, став також і чи не найголовнішим фактором біологізації рослинництва.
Постійна технологічна колія — один з невикористаних резервів підвищення ефективності рослинництва.
Однією зі складних проблем при застосуванні системи точного землеробства є визначення координат того чи іншого МТА на полі. Польові випробування засвідчили, що на точність визначення координат агрегата суттєво впливають атмосферні фактори. Залежно від пори року, часу доби, стану тропосфери тощо тренд визначення місцеположення об’єкта суттєво різниться. У результаті для внесення добрив, пестицидів, визначення забур’яненості посівів або урожайності окремих ділянок досягнутої точності достатньо, а для реалізації основного призначення системи — створення однакових умов росту і розвитку для кожної вирощуваної рослини без порушення норм екологічної безпеки — ні.
Для вирішення цієї проблеми пропонується нова компромісна концепція впровадження системи точного землеробства. Основою її є оригінальна методика визначення координат машинно-тракторних агрегатів на полі у процесі виконання ними операцій вирощування сільгоспкультур (у першу чергу просапних) із застосуванням колійної системи землеробства. Зміст останньої базується на розв’язанні принципового протиріччя у системі «рушій-ґрунт». Це протиріччя полягає в тому, що для досягнення енергетичним засобом високих тягово-зчіпних властивостей рушії мають контактувати із сухим та ущільненим ґрунтом, а для нормального росту культурних рослин потрібне оптимально вологе і пухке середовище. Уникнення цього протиріччя забезпечується під час руху МТА постійними технологічними коліями (ПТК). При цьому залишаться тільки відрегулювати зони ущільнення ґрунту, тобто досягти повної його (ущільнення) відсутності в зоні росту культур, а залишити в зоні проходу рушіїв енергетичних засобів.
Відомо, що основна частка переущільнення ґрунту припадає на весняний період виконання польових робіт. Тільки в посівах, наприклад, просапних культур за цей час проводиться сім ґрунтообробних операцій: боронування зябу, ранньовесняна і передпосівна культивація ґрунту, сівба з подальшим прикочуванням, досходове і післясходове боронування сходів. Розглянемо два варіанти виконання цих робіт. У першому згадані технологічні операції виконуються серійними машинно-тракторними агрегатами, склади яких представлено чисельниками даних другого і третього стовпчиків таблиці. Робоча ширина захвату використовуваних МТА при цьому різна і змінюється від 5,6 до 20 м.
Таблиця. Склади МТА і їх робоча ширина захвату на обробітку просапних культур із застосуванням ПТК (у знаменнику) і без неї (у чисельнику)
Операція | Склад МТА | Робоча шириназахвату МТА,м | |
трактор | машина | ||
1.Боронування зябуБоронування зябу зпрокладанням ПТК | Т-150ХТЗ-160 | 21 БЗТС-1,010 БЗТС-1,0 | 20,08,4 |
2.Культивація зябу | Т-150ХТЗ-160 | 2КПС-4КРН-8,41) | 7,88,4 |
3.Сівба | ЮМЗ-80ХТЗ-160 | СУПН-8СУПН-12 | 5,68,4 |
4.Прикочування посівів | Т-150ХТЗ-160 | 3 ККШ-63 ККШ-6 | 17,116,8 |
5.До- та післясходовеборонування посівів | Т-150ХТЗ-160 | 21 БЗСС-1,017 БЗСС-1,0 | 20,016,8 |
1) — у варіанті для суцільного обробітку ґрунту
Згідно з другим варіантом, згадані технологічні операції виконуються новими агрегатами, склади яких представлено знаменниками тих самих стовпчиків таблиці. Але за цих умов їхня робоча ширина або дорівнює, або кратна 8,4 м. Ця величина називається кроком (Н) постійної технологічної колії.
На рис. а в масштабі 1:400 відтворено сліди рушіїв тракторів на полі при виконанні розглядуваних технологічних операцій згідно з першим варіантом, а на рис. б — згідно з другим. Аналіз свідчить, що застосування ПТК (рис. б) зменшує площу ущільнення поля в середньому в 2,7 раза!
Процес формування слідів постійної технологічної колії відбувається під час виконання першої з тих технологічних операцій, які проводяться весною. Як правило, це боронування зябу. В іншому варіанті він виконується окремою операцією.
а) б)
Рис. Сліди рушіїв тракторів при використанні ПТК (б) та без неї (а)
Постійні технологічні колії повинні прокладатися із заданим кроком, а також бути поглиблені та вирівняні у поздовжньо-вертикальному напрямку. Глибина їх слідів має бути такою, щоб на момент сівби просапної культури без маркера вони візуально відстежувалися механізатором. Прямолінійність слідів ПТК повинна відповідати вимогам до прямолінійності рядків, а стабільність кроку — до прямолінійності стикових міжрядь просапних культур.
За результатами попередніх досліджень було встановлено, що для прокладання слідів постійної технологічної колії використовується трактор, який відповідає таким вимогам: тягове зусилля — в межах 20…40 кН; ходова система — колісна, яка б вписувалась у міжряддя просапних культур (70 см); компонування — інтегральне або класичне з можливістю оперативного переобладнання на реверсивний рух; наявність переднього гідрофікованого начіпного механізму. Таким вимогам повною мірою відповідають лише модульні енергетичні засоби універсально-просапного призначення, інформація про які викладена у липневому номері 2010 року The Ukrainian Farmer, та вітчизняні орно-просапні ХТЗ-160.
За прокладеними попередньо слідами ПТК рухаються в подальшому інші машинно-тракторні агрегати. Як підкреслювалось, їх ширина при цьому або дорівнює кроку колії або кратна їй. Якщо нині така вимога ще є проблематичною, то у найближчому майбутньому завдяки дедалі більшому поширенню модульного принципу конструювання сільгосптехніки вирішення цього питання стане тривіальним.
Істотнішого збільшення врожайності сільськогосподарських культур слід чекати лише після тривалого використання ПТК. Цілком реальним ефектом, який отримують на першому році впровадження системи землеробства з постійною колією, є зниження затрат на виробництво продукції. У першу чергу це відбувається за рахунок зменшення витрат енергії МТА, оскільки рух слідами ПТК однозначно характеризується як зростанням тягово-зчіпних якостей енергетичного засобу, так і значним зниженням опору на його перекочування.
Підтвердженням служать отримані нами дані експериментальних досліджень. Агрегат, ширина захвату якого дорівнювала 12,6 м, складався з енергетичного засобу МЕЗ-200, зчіпки СН-75, центрального культиватора КРН-8,4 і двох бічних культиваторів КРН-2,1. У першому варіанті МЕЗ-200 рухався по розпушеному ґрунту, а в другому — по заздалегідь прокладених слідах ПТК. Вологість агрофону становила 20,6%, а твердість — 0,38 мПа. Твердість ґрунту слідів ПТК була більшою в 3,56 раза, тобто становила 1,71 мПа. В обох варіантах агрегат рухався на одній і тій же передачі за постійно встановленої глибини обробітку ґрунту, яка дорівнювала 10 см. Результати виявилися такими. Якщо при переміщенні енергетичного засобу по розпушеному ґрунту буксування рушіїв складало 9%, то при русі слідами ПТК знизилося до 7%. Робоча швидкість руху МТА зросла при цьому з 7,85 до 8,05 км/год., витрата палива зменшилася з 21,3 до 19,0 кг/год., тобто на 12,1%.
Можливість руху МТА при колійному землеробстві з більшою робочою швидкістю пояснюється не тільки зниженням буксування рушіїв трактора. В якості констатації факту відзначимо, що не меншу роль грає підвищення плавності ходу енергетичного засобу через кращу поздовжню вирівняність слідів ПТК порівняно з мікрорельєфом поля, що обробляється. У тих випадках, коли приріст швидкості агротехнічно допустимий і прийнятний, зниження затрат праці, як свідчать розрахунки, може досягати 10 і більше відсотків. За потреби сліди ПТК використовуються протягом три- або чотирирічної сівозміни. Зазначу, що ми маємо практичний досвід застосування колійної технології землеробства.
Компетенції №16- 17-18
Для орієнтовного визначення розмірів зазорів у клапанах без зняття клапанних кришок користуються автостетоскопом, яким прослуховують стуки при малій частоті обертання колінчастого вала. Якщо виявлено чіткі металеві стуки потрібно зупинити двигун, відкрити клапанну коробку й перевірити розміри зазорів щупом або діагностичним пристроєм КИ-9918. Двигун допускається до експлуатації при помірних стуках клапанів, штовханів і розподільного вала на малих обертах холостого ходу. Якщо є потреба, то необхідно перевірити зазори клапанів і відрегулювати їх. Але це пов'язано з зупиненням і частковим розбиранням двигуна і виправдане лише в разі регулювання теплового зазору. Потребу такого регулювання потрібно встановити. для чого використовують віброакустичні методи.
Дослідження вібрацій, які формуються механізмом системи газорозподілу, показали, що зі зміною розмірів теплового зазору суттєво змінюється інтенсивність вібрації кришки головки блоку в зоні контрольованого клапана. Це й покладено в основу діагностування. Діагностичними зонами встановлення датчика) є гайки кріплення кришки головки блоку. Найкращі умови для виділення вібраційних імпульсів створюються на низькій частоті обертання колінчастого вала (приблизно при п = 1000 хв-1).
Для роздільного визначення нещільності клапанів газорозподілу використовують прилад К-69М, індикатор витрат газів КИ-4887-И та компресорно-вакуумну установку КИ-4942 .
Діагностування клапанів за витоком повітря та їх регулювання
За витоком повітря клапани діагностують з використанням приладу К-69М , подаючи стиснене повітря в контрольований циліндр від компресорно-вакуумної установки. Для цього служить спеціальний робочий накінечник, від якого повітря надходить в отвір для форсунки. Вентиль 1 повинен бути закритий, а вентиль 4 відкритий. Робочий накінечник приєднують до штуцера і стиснене повітря подається безпосередньо з ресивера поза приладом, який реєструє витік. З камери згоряння повітря надходить частково в картер крізь щілини між циліндром і поршневими кільцями, а частково крізь нещільності впускного і випускного клапанів. З колектора повітря частково потрапляє крізь відкритий клапан у камеру згоряння відповідного циліндра. В отвір для свічки (для форсунки) встановлюють спеціальний індикатор у вигляді скляної трубочки з гумовим накінечником і закріпленим у ній стрижнем з ворсинками. Другий кінець трубочки закритий гумовою пробкою з отвором.
Якщо якийсь клапан контрольованого циліндра прилягає нещільно, то стиснене повітря, потрапляючи у відповідний циліндр крізь відкритий клапан, виходить в атмосферу через індикатор і відхиляє його ворсинки. Чим більша нещільність клапана, тим більший кут відхилення ворсинок. Місце встановлення індикатора визначають за схемою, яка наводиться в інструкції і на кришці приладу, відповідно до порядку роботи двигуна. Недоліком цього методу є те, що він не дає змоги визначити об'єм витоку; ним можна лише констатувати, є витік повітря чи немає.
Більш інформативним є метод роздільного діагностування клапанів, який грунтується на подаванні повітря в контрольований циліндр з використанням індикатора витрат газів КИ-4887-ІІ. Для діагностування колінчастий вал двигуна встановлюють за кутом повороту колінчастого вала у таке положення, щоб впускний і випускний клапани контрольованого циліндра були закриті, а в інших циліндрах двигуна клапани не перекривалися.
Діагностуючи чотирициліндрові двигуни, спочатку встановлюють поршень контрольованого циліндра в положення верхньої мертвої точки в кінці такту стиску, а потім прокручують колінчастий вал проти ходу або за ходом обертання ще на 90°. При цьому випускний і впускний тракти двигуна не будуть з'єднані між собою.
Для перевірки випускного клапана стиснене повітря від компресорної установки через ресивер надходить у циліндр. Стиснене повітря з камери згоряння проривається частково крізь кільцеві ущільнення в картер, а частково крізь нещільності впускного клапана потрапляє у впускний трубопровід і звідти відсмоктується компресором через рідинний манометр, витратомір і дросель індикатора КИ-4887-ІІ у впускну систему компресора. Відсмоктування повітря регулюють дроселем і контролюють рідинним манометром так, щоб під час вимірювання тиск у впускному трубопроводі дорівнював атмосферному. Цим забезпечується збільшення точності вимірювань за рахунок уникнення витрат крізь кільцеві ущільнення циліндрів і впускного трубопроводу. Витрати повітря, виміряні витратоміром приладу, характеризують нещільність впускного клапана.
Нещільність випускного клапана визначають аналогічно, але для цього витратомір КИ-4887-ІІ приєднують до випускного трубопроводу. Якщо витік повітря хоч би крізь один клапан перевищує допустиме значення, потрібно зняти головку циліндрів і притерти клапани до гнізд.
Двигун допускається до експлуатації при помірних стуках клапанів, штовхачів і розподільного вала на малих обертах холостого ходу. У разі потреби теплові зазори в клапанах регулюють.
Необхідність регулювання клапанів, крім стуків, визначає втрата потужності двигуна з одночасним збільшенням шуму в клапанному механізмі.
Регулювання зазорів у клапанах - трудомістка операція, оскільки на багатьох двигунах потрібно виконати демонтажні роботи. Тепловий зазор вимірюють щупом або приладом КИ-9918. Розміри зазорів наводяться в інструкціях з експлуатації.
Зношення кулачків розподільного вала визначають штангенглибиноміром або штангенциркулем при розміщенні поршня у верхній мерів; точці на такті стиску. Спочатку вимірюють відстань від поверхні головки циліндрів до торця клапана, після чого прокручують колінчастий вал двигуна до повного відкриття клапана і знову вимірюють названу відстань. Різниця між вимірюваннями буде величиною переміщення клапана. Якщо вона менша за допустиме значення, то розподільний вал двигуна потрібно замінити.
Утворений нагар в умовах експлуатації можна вивести при знятій головні блоку і без зняття її.
При знятій головці нагар виводять металевими скребками або щітками. Перед цим його розм'якшують гасом.
Без зняття головки нагар виводять, заливаючи в кожен циліндр прогрітого двигуна 150...200 см3 суміші, яка складається з гасу (80%) та моторної оливи (20 %). Потім міняють свічки на зношені і декілька разів прокручують колінчастий вал, вмикаючи двигун на 20...3О хв через кожні 10...12 год (за цей час пом'якшений нагар вигоряє).
Після виведення нагару потрібно замінити оливу в картері двигуна, а перед запуском у кожен циліндр залити по 20...30 см3 свіжої моторної оливи.
Тепловий зазор регулюють при повністю закритих клапанах, починаючи з першого циліндра, коли він перебуває у верхній мертвій точці на такті стиску. Перед тим потрібно перевірити і в разі потреби підтягнути гайки головки блоку циліндрів. Спочатку підтягують гайки, до яких є підхід. Якщо гайки прокручуються, з головки знімають валик з коромислом і динамометричним ключем підтягують усі гайки. Після того, як зняті деталі (крім кришок) будуть поставлені на місце, перевіряють і, якщо потрібно, регулюють зазори. Для цього встановлюють поршень першого; циліндра у верхню мертву точку при такті стиску. Після перевірки та регулювання клапанів і декомпресійного механізму в першому циліндрі регулюють зазори клапанів інших циліндрів.
Трудомісткість перевірки клапанів пристроєм КИ-9918 становить 0,1 люд.-год (з використанням щупа - 0,7 люд.-год) з похибкою ±0,02 мм (з використанням щупа - ±0,05 мм). Використовуючи цей пристрій, можна перевіряти не лише тепловий зазор у верхньоклапанному механізмі, але й фази газорозподілу, а також визначати положення верхньої мертвої точки поршня контрольованого циліндра.
Рис. 3.1 Пристрій КИ-9918:
1-пружина; 2-рухома каретка; 3-напрямна; 4 - вісь;
5-корпус (нерухома каретка); 6-відтискний кулачок;
7-стержень; 8 -індикатор; 9 - важіль; 10 - кулачок гальма;
11-накінечник індикатора; 12-валик декомпресора
Рис. 2.2Перевірка й регулювання теплового зазору
1 — коромисло; 2 — контргайка; 3 — регулювальний гвинт
Регулювання зазорів у механізмі привода клапанів відбувається тільки на холодному двигуні. Попередньо необхідно зняти кришку коромисел, трубку вакуумного регулятора й деталі системи вентиляції картера.
Зазначені в характеристиці величини зазорів не слід зменшувати навіть при наявності помітного стукоту. Зменшення зазору викликає нещільне прилягання клапана до сідла й небезпека його прогоряння.
Підвищений шум клапанів, хоча й неприємний на слух, але не викликає порушення нормальної роботи двигуна.
Основними роботами при технічному обслуговуванні газорозподільного механізму є підтяжка гайок (болтів) кріплення головки циліндрів, перевірка і при необхідності регулювання зазорів між клапанами і коромислами, а також прослуховування працюючого двигуна для виявлення стуків, заміна зношених або зламаних деталей.
Призначення і загальна будова кривошипно-шатунного механізму.
Блок-картери і циліндри рядних і V -подібних двигунів, їх призначення, будова, умови роботи; матеріал виготовлення. Гільзи циліндрів (сухі і мокрі), їх призначення, переваги і недоліки. Встановлення гільз та ущільнення в місцях посадки. Конструктивні особливості циліндрів двигунів з повітряним охолодженням. Конструктивні особливості блоків циліндрів дизельних і карбюраторних двигунів.
2. Головки циліндрів, їх призначення, матеріал виготовлення. Фактори, які впливають на конструкцію головок блоку циліндрів. Принцип ущільнення (газового і рідинного) стиків між головкою та блоком циліндрів. Конструкція поршнів карбюраторних і дизельних двигунів.
3. Розмірні (вагові) групи поршнів, матеріал та технологія виготовлення Поршневі кільця, їх призначення, матеріал і обробка. Типи кілець, їх конструкція. Кількість і розміщення кілець на поршні.
4. Збірні кільця. Покриття кілець, зазори в замках і по висоті між кільцем та поршневою канавкою. Установка кілець.
5. Поршневі пальці, їх призначення, умови роботи, матеріал і обробка. Вимоги до поршневих пальців. Способи кріплення пальців. Плаваючі пальці характер спряжень.
6. Шатуни і шатунні підшипники. Типи шатунних підшипників. Будова нижньої та верхньої головок шатуна. Шатунні болти. Затягування болтів. Зазори в підшипниках.
7. Колінчасті вали і їх конструктивні форми. Фіксація колінчастого вала в осьовому напрямку. Робота циліндрів за різної форми вала для дво-. чотири-, шести- та дванадцятициліндрових двигунів.
8. Корінні підшипники, застосування кулькових і роликових підшипників. Зазори в корінних підшипниках.
Маховики, їх призначення, матеріал та способи кріплення. Фактори, від яких залежить маса і розмір маховика. Мітки на маховику. Гасник крутильних коливань.
Література:
1.Білокінь Я.Ю.,Окоча А.І., Войцехівський С.О. Трактори та автомобілі. - К.; Вища школа, 2003.; с.51-64.
2. Лебедев А.Т. та ін. Трактори та автомобілі: Ч. 1. Автотрак-торні двигуни. - К.: В.Ш 2000. с.56-90.
1. Загальна будова
Кривошипно-шатунний механізм (КШМ) призначений для перетворення поворотно-поступальної ходи поршня в обертальний рух колінчастого валу і сприйняття тиску газів, виникаючого в циліндрі.
Рухомі деталі КШМ включають: поршні з кільцями і поршневим пальцем, шатун, колінчастий вал, і маховик;
нерухомі деталі - картер, блок циліндрів, головка циліндрів (головка блоку), кришка розподільних шестерень і піддон (масляний картер).
2. Блок-картер (блок циліндрів)
Картер являє собою масивну нерухому металеву деталь, яка несе основні складові одиниці і деталі двигуна. Картер більшості двигунів виконаний в загальній відливці з блоком, наприклад - А-41, Д-240, СМД-60, ГАЗ-53, ЗІЛ-130. Тоді, такі відливки називаються блок–картерами. При цьому конструкція двигуна більш жорстка. Відливають блок–картери і картери із сірого чавуну або з алюмінієвого сплаву.
Циліндр разом із головкою та поршнем утворюють замкнутий об’єм, у якому протікає весь тепловий процес роботи двигуна. По конструктивному виконанню циліндри можуть бути виконані кожен окремо або загальною відливкою (блок циліндрів). Циліндри індивідуального виготовлення кріпляться до картера з допомогою шпильок.
Конструкція циліндрів, в основному, визначається способом охолодження. Якщо охолодження двигуна повітряне, то циліндри мають спеціальні ребра охолодження. При рідинному охолодженні між зовнішньою поверхнею циліндра і внутрішніми стінками блока існує кільцевий простір - водяна сорочка, яка заповнюється рідиною. Оскільки циліндри в двигуні зношуються в першу чергу, то вони виготовляються із змінними гільзами.
Внутрішня поверхня циліндра, всередині якої переміщається поршень, називається дзеркалом. Гільзи поділяють на мокрі і сухі (рис.4.1). Зовнішній бік мокрої гільзи охолоджується рідиною, а суху гільзу встановлюють у розточений циліндр блок-картера і охолоджувальна рідина омиває зовнішній бік циліндра. Товщина стінок мокрих гільз становить 6 -
Рис. 4.1. Гільзи циліндрів:а – будова гільзи; б – встановлення в блок-картер мокрої гільзи; в – встановлення в блок-картер сухої гільзи: 1 – канавки для ущільнювальних кілець; 2, 4 - посадочні пояски; дзеркало циліндра; 5 – буртик; 6 – гільза циліндра; 7 – рідинна сорочка охолодження; 8 – блок-картер; 9 – гумові ущільнювальні кільця; 10 – мідне ущільнювальне кільце; 11 – металоазбестова прокладка головки циліндрів
Найбільше спрацювання проходить у верхній частині циліндра (гільзи), де висока температура і сильний корозійний вплив відпрацьованих газів. Тому, на деяких двигунах у верхній частині циліндра запресовують короткі вставки, виготовленні із антикорозійного чавуну.
За внутрішнім діаметром гільзи поділяють на групи: «Б» - велика; «С» - середня; «М» - мала. Літеру, якою позначається група, вибивають на торці верхнього бурта гільзи. При встановленні підбирають гільзи однієї групи. Це потрібно для забезпечення необхідного зазору між гільзами і поршнями, які також мають певні групи.
Знизу картер закриває піддон, який служить також резервуаром для масла. У масляному піддоні вмонтовано злив масла із зливною пробкою. На деяких двигунах у пробці закріплено магніт для вловлювання металевих частинок, які потрапляють у масло. Між масляним піддоном і картером встановлено картонну паронітову прокладку.
Рис 4.2 Деталі кривошипно-шатунного механізму:
а – V- образного карбюраторного двигуна; б - V- образного дизеля; в – з'єднання головки циліндра і гільзи, головки і блоку циліндрів дизеля КамАЗ-740; 1 – кришка блоку розподільних зубчатих коліс; 2 – прокладка головки блоку; 3 – камера згорання; 4 – головка блоку циліндрів; 5 – гільза циліндра; 6 і 19 – кільця ущільнювачів; 7 – блок циліндрів; 8 – гумова прокладка; 9 – головка циліндра; 10 – прокладка кришки; 11 – кришка головки циліндрів; 12 і 13 – болти кріплення кришки і головки циліндра; 14 – патрубок випускного колектора; 15 – болт – стягування; 16 – кришка корінного підшипника; 17 – болт кріплення кришки корінного підшипника; 18 – сталеве опорне кільце; 20 – сталева прокладка головки циліндра;
3. Циліндри двигуна
Циліндр служить направляючим для поршня і створює об'єм, необхідний для протікання ряду процесів робочого циклу двигуна. У двотактних двигунах циліндри забезпечують газообмін в двигуні. Циліндри можуть відлити у вигляді одного блоку разом з верхньою частиною картера (ВАЗ-2110 і ін., рис.4.3,а), можуть відлити окремо і кріпитися до верхньої половини картера двигуна (ЗАЗ-968М і ін.). Часто циліндри виготовляються у вигляді знімних гільз 5 (рис.4.3,в,г,д,е), встановлюваних в загальному блоці. Гільзи, безпосередньо омивані охолоджуючою рідиною, називаються "мокрими", а гільзи, зовнішня поверхня яких стикається з внутрішньою поверхнею блоку циліндра, називаються "сухими".
Використовування знімних гільз полегшує ремонт двигуна. Іноді у верхню частину циліндра (гільзи) запресовують коротку суху гільзу 1 з кислототривкого чавуну, що забезпечує рівномірний знос циліндра по висоті. Матеріалом для гільз є або сірий чавун (карбюраторні двигуни), або високоміцний легований чавун (дизелі ЯМЗ і КамАЗ і ін.).
Внутрішня поверхня циліндра для зменшення зносу ретельно обробляється і називається дзеркалом циліндра. Для установки гільз в блоці циліндрів двигунів ЗІЛ-130, ЯМЗ-236, КамАЗ-740, (рис.4.3,в,г) гільза має два направляючі поясочки - верхній і нижній і фіксується в осьовому напрямі верхнім буртом. У двигунах ГАЗ і ін. гільзи мають тільки один направляючий пояс і фіксуються в блоці нижнім буртом (мал.4.3,д). Верхній торець гільзи при установці в блок повинен виступати над його поверхнею на 0,02-0,15мм, тому при закріпленні головки блоку вона вдавлює свою прокладку в торець гільзи і притискує бурт гільзи до блоку.
Ущільнення нижньої частини гільзи здійснюється або гумовими кільцями 4 (рис.4.3,г), або мідною прокладкою 7 (рис.4.3,д).
Рис 4.3 Схеми циліндрів двигунів.
а – без гільзи; б – з короткою сухою гільзою; в – з мокрою гільзою (ЯМЗ- 236, ЯМЗ- 238); г - з мокрою гільзою з двома посадочними поясочками з короткою і сухою гільзою (ЗІЛ – 130); д – з мокрою гільзою і одним посадочним поясочком і з короткою сухою гільзою (ГАЗ - 53); е – з довгою сухою гільзою і повітряною сорочкою; 1 – вставка; 2 – сорочка охолоджування; 3 – наполегливий бурт; 4 – ущільнююче кільце; 5 – мокра гільза; 6 – повітряна сорочка; 7 – мідне кільце.
4. Головка циліндрів
Головка циліндрів може бути встановлена на кожен циліндр окрема 9 (КамАЗ-740 мал.4.2,б) або цільна 4 (Рис.4.2,а) - на групу циліндрів.
Головка блоку циліндрів служить кришкою для циліндрів. Для герметичності між головкою і циліндрами встановлюється прокладка 2. Головка виготовляється з алюмінієвого сплаву, а затягуються гайки сталевих шпильок кріплення головки - на "холодну" в певній послідовності і зі встановленим зусиллям.
Головка також може бути виготовлена з сірого чавуну (двигуни ЯМЗ-236, ЗІЛ-645, Д – 65, Д – 240, А - 41 і ін.). В цьому випадку гайки сталевих шпильок кріплення головок затягуються "на гарячу", тобто з попереднім підігрівом.
Головка має канали для охолоджуючої рідини, для проходу повітря, горючої суміші і відпрацьованих газів, в ній встановлюються клапани, свічки запалення або форсунки (у дизелів) і інші деталі. У двигунах в головці циліндрів часто розташовуються камери згорання (стиснення), в яких виробляється попереднє стиснення горючої суміші.
Найбільше поширення набули напівклинові камери згорання III з одностороннім розташуванням клапанів (двигуни ЗІЛа, ЗМЗ, Ваза і ін., рис.4.4,а), півсферичні II з двостороннім розташуванням клапанів (двигуни Москвичів). Зміщені або Г-образні IV використовуються на двигунах старих моделей з нижнім розташуванням клапанів, але вони менш компактні, погано протистоїть детонація, гірше забезпечують заповнення циліндрів свіжою горючою сумішшю.
У дизелів камери згорання розташовуються в поршні V і VI, а передкамери в головці циліндрів VII і VIII (Рис.4.4,б).
Між головкою і блоком циліндрів ущільненням служить азбестова прокладка, облямована металом або металева (сталь, мідь, дюралюміній) або азбестова, армована металевою сіткою.
Ущільнення каналів систем мастила і охолоджування виконують іноді гумовими прокладками.
Рис.4.4. Форми камер згоряння: а – карбюраторних двигунів; б – дизелів: I – циліндрична; II – напівсферична; III – клинова; IV – зміщена (Г- подібна); V і VI - нероздільна; VII і VIII – роздільні; 1 – клапан; 2 – свічка запалювання; 3 – насос-форсунка; 4 – камера згоряння; 5 – форсунка; 6 – передкамера; 7 – основна камера; 8 – вихрова камера
Рис4.5. Прокладка головки циліндрів чотирьохциліндрового дизеля:1 – стальний каркас; 2 – азбестові листи; 3 - обкантовка
5. Поршні
Поршень служить для сприйняття тиску газів, що розширяються, під час такту розширення і здійснює допоміжні такти (впускання, стиснення, випуск). Поршень 9 (рис.4.5) складається з трьох частин: головки, спідниці 8 і бобишек. Головка має днище 6 і канавки для поршневих кілець 3 і 4. Спідниця 8 є направляючою для поршня. Бобишки служать для кріплення поршневого пальця 2. З внутрішньої сторони на головці і днищі виконані ребра жорсткості для підвищення міцності. У бобишках проточені канавки для стопорних кілець 1, фіксуючі палець 2 від переміщень уздовж осі, щоб не пошкодити дзеркало циліндра. Оскільки поршень виготовляється з алюмінієвого сплаву, а гільзи циліндра з чавуну, то через великий коефіцієнт розширення алюмінієвого сплаву і великого нагріву, поршень має складну овально-конусну форму. Діаметр головки на 0,5-
Рис 4.5 Шатунно-поршнева група:
а – дизелів сімейства ЯМЗ; б і в – двигунів автомобілів ГАЗ – 53-12 (дані поршні в зборі з шатуном, встановлювані в перший, другий, третій і четвертий циліндри правого блоку і в п'ятий шостий сьомий і восьмий циліндри лівого блоку); 1 – стопорне кільце; 2 – поршневий палець; 3 – маслоз'ємне кільце; 4 – компресійні кільця; 5 – камера згорання в днищі поршня; 6 – днище поршня; 7 – головка поршня; 8 – спідниця; 9 – поршень; 10 – розпилювач масла (форсунка); 11 – шатун; 12 – вкладиші; 13 – замкова шайба; 14 – довгий болт; 15 – короткий болт; 16 – кришка шатуна; 17 – втулки головки шатуна; 18 – напис на поршні; 19 – номер на шатуні; 20 – влучна на кришці шатуна; 21 – шатунний болт.
При роботі двигуна, поршень нагрівається, діаметр бобишек збільшується і палець провертається, як в бобишках, так і у верхній головці шатуна. Така конструкція називається "плаваючий палець" і дозволяє уникнути стукотів пальця в поршні і збільшує термін служби. Під час переходу поршня через ВМТ він переміщається від однієї стінки циліндра до іншої, що супроводжується стукотами. Щоб усунути ці стукоти, вісь отвору під поршневий палець зміщують на (1,5-2,0мм) убік максимального бічного тиску (якщо дивитися на двигун спереду, то зсув робиться вліво). Оскільки поршень має складну геометричну форму, то для правильної його установки в циліндр на ньому робляться спеціальні мітки, які повинні поєднуватися з мітками на шатуні. На днищах поршнів двигунів ЯМЗ-236 зроблене поглиблення у формі тора, яке є неподіленою камерою згорання, що забезпечує добре завихрення і розпилювання палива і повніше його згорання. Крім того на поршні двигуна КамАЗ зроблені проточки під тарілки клапанів впускання, випускного, оскільки зазор між днищем поршня і головкою циліндра у цього двигуна дуже малий (біля 0,5мм). Поршень двигунів ЗМЗ має на спідниці напівкруглі вирізи для проходу противаг колінчастого валу, що одночасно зменшує вагу поршня і зменшує дію сил інерції. На спідниці поршня ЯМЗ-236 є додаткова канавка для маслоз'ємного кільця, що зменшує можливість попадання масла з картера в камеру згорання. Поршні до циліндрів підбирають по розмірних групах, що звичайно маркіруються буквами А, B, З, D, Е.
6. Поршневі кільця
Поршневі кільцяпо призначенню поділяють на компресійні (ущільнювальні), які встановлюють по 3-4, і маслоз’ємні- по 1 або 2.
Поршневі компресійні кільця служать для ущільнення зазору між поршнем і стінкою циліндра. В результаті їх встановлення попереджується прорив повітря чи газів з простору над поршнем в картер двигуна, а також проникнення масла в камеру згоряння. Одночасно компресійні кільця відводять тепло від головки поршня до стінок циліндрів. Компресійні кільця притискаються до стінки циліндра силами своєї пружності і тиску газів. Виготовляють їх із легованого чавуну або сталі.
Виріз в поршневому кільці називається замком. Замки мають різну форму: пряму, косу (30-40 °) ступінчасту або фасонну. Найбільше поширення отримали кільця із прямими замками. Щоб зменшити проривання газів через замки (величина яких на встановлених в гільзу кільцях 0,2...0.8 мм), кільця встановлюють так, щоб замки не перебували в одній площині, а залежно від числа кілець - під кутом 90... 120°. Компресійне кільце працює надійно, якщо воно щільно прилягає до дзеркала циліндра. Для забезпечення щільного прилягання кільця виготовляють з різною формою поперечного перерізу (рис.15). Якщо прийняти тиск в камері згоряння за 100% то зверху перше кільце сприймає (гасить) 76% тиску, друге -20%, третє – 7,6%.
Рис. 4.6. Форми поперечних січень поршневих компресійних кілець:а - прямокутне; б –конусне; в – з фаскою із внутрішньої сторони; г – з виточкою на внутрішній стороні; д – одностороння трапеція; е – кільце з виточкою по зовнішній стороні
Маслоз’ємні кільця знімають зайве масло із дзеркала циліндра й відводять його в картер через отвори в кільцях та масловідвідні канали в канавках поршня (рис4.6.1). Масло яке залишається маслозємні кільця рівномірно розподіляють по дзеркалу. Як правило на поршень встановлюють одне або два кільця. За конструктивним виконанням вони бувають циліндричні з проточками та отворами для відведення масла, з пружним розширювачем, скребкового типу, яких в канавку поршня вкладається два. Збірні маслоз’ємні кільця з пружними розширювачами (рис.4.6.1 в) краще знімають масло зі стінок циліндра.
Рис.4.6.1. Маслоз’ємні поршневі кільця: а – схема роботи маслоз’ємних кілець при русі поршня вниз; б – схема роботи маслоз’ємних кілець при русі поршня вверх; в – збірне маслоз’ємне кільце: 1 – масло відвідний канал; 2 – поршень; 3 – циліндр; 4 – прорізь в кільці; 5 – канал в поршні; 6 – плоскі стальні кільця; 7 – осьовий розширювач; 8 – радіальний розширювач
Вони складаються з двох стальних дискових кілець 6 між якими встановлюють розширювачі – осьовий 7 і радіальний 8. Радіальний розширювач виготовлений із стальної пластини, яка завдяки своїй пружності збільшує тиск кілець на дзеркало. Маслоз’ємні кільця виготовляють як із чавуну, так і сталі.
7. Поршневі пальці
Поршневий палець служить для шарнірного з’єднання поршня із шатуном. При роботі поршневий палець піддається механічним навантаженням, змінними по значенню і напрямку, тому повинен бути міцним і жорстким. Крім цього, поршневий палець повинен бути легким і зносостійким. Виготовляють пальці із труб маловуглецевої сталі. Поверхню цементують на глибину до
У сучасних автомобілях під час роботи палець вільно обертається у бобишках і у верхній головці шатуна, тому його називають плаваючим. Для того щоб палець під час роботи двигуна не переміщався в осьовому напрямку і не пошкоджував при цьому дзеркало гільзи циліндра, його закріплюють.
За величиною зовнішнього діаметра пальці поділяють на розмірні групи, які позначаються на внутрішній поверхні пальців. При складанні розмірні групи пальців і поршнів повинні співпадати. Відсутність маркування свідчить про єдину розмірну групу.
"Плаваючі" пальці, що провертаються в поршні і в шатуні, від осьового зсуву утримуються стопорними кільцями в поршні. "Неплаваючі" пальці запресовуються у верхню головку шатуна, в ній не провертаються і стопорних кілець не вимагають. Пальці підбирають до поршнів по розмірних групах, що позначаються на пальцях і поршнях фарбою певного кольору.
8. Шатуни
Шатун служить для передачі зусилля від поршневого кільця до колінчастого валу і їх з'єднання.
Шатун з'єднує поршень через поршневий палець з шатунною шийкою колінчастого вала. Внаслідок того, що на шатун діють значні зусилля, які розтягують або стискують його стержень, шатуни повинні бути міцними, жорсткими і легкими. Шатуни виготовляють з високоякісної сталі, потім піддають термічній обробці (загартовуванню та відпуску). Шатун (див. рис.4.8) складаєтьсяз верхньої та нижньої головок і стержня.
Верхняголовка не рознімна. Для зменшення тертя шатуна з поршневим пальцем у верхню головку запресовують підшипник, виготовлений у вигляді бронзової або стальної втулки з шаром бронзи. Змащення поршневого пальця здійснюється завдяки отворам у верхній головці, які вловлюють краплини масла.
Стержень шатуна для більшої міцності двотавровий і переходить у нижню та верхню головки. Така конструкція забезпечує необхідну міцність і жорсткість при мінімальній масі.
Площина розняття нижньої головки перпендикулярна до осі симетрії шатуна (дизелі Д-21А, Д-120, Д-37Е, Д-Н4, Д-240) або розміщена під кутом 45" до вертикальної осі шатуна (дизелі Д-65, А-41, СМД-60). Кришку 10 нижньої головки шатуна кріплять до нього двома болтами 8, виготовленими з високоякісної сталі. Гайки болтів шатуна затягують динамометричним ключем і ретельно шплінтують або стопорять спеціальними стопорними шайбами.
Нижню головку шатуна і кришку розточують разом для отримання отвору правильної циліндричної форми. Тому, кришку не можна перевертати або переставляти на інші шатуни. На шатунах і кришках з одного боку ставлять необхідні для цього мітки.
У нижній головці шатунів встановлюють підшипники ковзання, що складаються з двох вкладишів. Взаємозамінні тонкостінні вкладиші виготовлені із сталевої стрічки (товщиною 1,3 -
Від осьового зсуву і прокручування шатунні підшипники утримуються в своїх гніздах вусиками, що входять в пази, які розташовані на одній стороні шатуна. Масло до вкладишів надходить по каналах, виконаних в колінчастому валу, коли ті під час його обертання співпадають з отворами вкладишів. За допомогою каналу на внутрішній поверхні масло рівномірно розподіляється по поверхні вкладиша.
Рис.4.8. Шатун і шатунні підшипники:1 – верхня головка; 2 - втулка верхньої головки; 3 - стержень; 4 - нижня головка; 5 - вкладиш шатунного підшипника; 6 - кришка нижньої головки; 7 – шплінт; 8 – гайка; 9 - вус-фіксатор; 10 - шатунний
9. Колінчастий вал.
До деталей групи колінчастого вала належать: колінчастий вал, маховик, корінні підшипники, пристрої для фіксації колінчастого вала від осьових переміщень, масловідбивачі і сальники.
Колінчастий вал сприймає ударні навантаження, які передаються від поршнів через поршневий палець і шатун. Крутний момент, який розвивається на колінчатому валу, передається на трансмісію, а також використовується для приводу в рух різних механізмів і деталей двигуна.
Колінчастий вал (рис.4.9.1.) складається із наступних основних елементів: корінних шийок 1, якими вал спираються на корінні підшипники, що розміщенні у картері; шатунних шийок 11; щік 2 і 12, які зв’язують корінні і шатунні шийки для зменшення концентрації напружень; носка (передній кінець); хвостовика (задній кінець).
Місця переходу шийок в щоки виконані у вигляді заокруглень і називаються галтелями 13. З метою розвантаження корінних підшипників від дії відцентрових сил, на щоках колінчастих валів деяких двигунів, встановлюються противаги 14.
Шатунні і корінні шийки вала спрацьовуються від тертя, тому матеріал колінчастого вала повинен бути досить твердим, водночас в'язким і мати високу міцність. Колінчасті вали виготовляють з якісної вуглецевої сталі (СМД-60, Д-240, ЯМЗ),способом гарячого штампування або відливають з високоміцного чавуну (ГАЗ-53). Робочі поверхні загартовують струмом високої частоти на глибину від 1,5 до,0 мм, шліфують і полірують з великою точністю (овальність і конусність шийок не повинна перевищувати
Рис.4.9.1. Колінчастийвал дизеля:1- корінна шийка; 2, 12 – щоки; 3- упорні півкільця; 4 – нижній вкладиш корінного підшипника; 5 – маховик 6 - масловідбивна шайба; 7 – установочний штифт; 8 – болт; 9 – зубчатий вінець; 10 - верхній вкладиш п’ятого корінного підшипника; 11 – шатунна шийка; 13 – галтель; 14 – противага; 15 – болт кріплення противаги; 16 – замкова шайба; 17 – шестерня колінчастого вала; 18 – шестерня приводу масляного насосу; 19 – упорна шайба; 20 – болт; 21 – шків; 22 – канал підведення масла в порожнину шатунної шийки; 23 пробка; 24 – порожнина в шатунній шийці; 25 – трубка для чистого масла
Форма колінчастого вала залежить від кількості і розташування циліндрів, порядку роботи і тактності двигуна. Кількість шатунних шийок в рядних двигунах відповідає кількості циліндрів двигуна, а у V- подібних - кількості циліндрів в одному ряду, оскільки в них до одної шийки приєднано два шатуни. Корінних шийок на одну більше, ніж шатунних. Шатунні шийки відносно одна одної у дво- і чотирициліндрових двигунів зміщені на 180°, у шестициліндрових - на 120°, у восьмициліндрових – на 90°. Це забезпечує рівномірне чергування робочих тактів і зрівноваження сил інерції.
У передній частині вала встановлено одну або дві (двигун
Д-240) шестерні 17 і 18 приводу газорозподільного механізму та масляного насоса, шків 21 приводу вентилятора. Хвостовик колінчастого вала закінчується фланцем для кріплення маховика. Для обмеження переміщення колінвала в поздовжньому напрямку, використовуються стопорні упорні шайби 19 та напівкільця 3.
У більшості двигунів у колінчастому валові робляться отвори для підведення мастила до корінних і шатунних підшипників, а також передбаченні порожнини 24 для відцентрової очистки масла (в щоках і корінних шийках є отвори і порожнини для накопичення металевих домішок).
Шатунні та корінні підшипникиколінчастого вала більшості двигунів є підшипниками ковзання. Підшипники кочення застосовують тільки в одно-, двоциліндрових двигунах та в двигунах з рознімним колінчастим валом.
Вкладиші корінних підшипників за будовою подібні до шатунних. Вкладиші виготовляють із стальної стрічки товщиною 1...3 мм; шар антифрикційного сплаву становить 0.1...0,9 мм. Цей сплав наноситься безпосередньо на стальну стрічку або на металокерамічну основу (60% міді та 40% нікелю).
Як антифрикційні сплави використовують високо-олов'янисті бабіти на свинцевій основі, свинцевисті бронзи, сплави на алюмінієвій основі та інші. У бабітів незначний коефіцієнт тертя і вони добре змащуються, однак з підвищенням температури їх механічні властивості погіршуються. Застосовують бабіти для виготовлення вкладишів карбюраторних двигунів.
Свинцевисті бронзи й алюмінієві сплави використовують для виготовлення вкладишів дизелів, оскільки вони можуть працювати при навантаженнях більше 10 МПа і температурі понад 800С.
Мідно-нікелева основа тришарового вкладиша зміцнює з'єднання бабіту зі стальною стрічкою. Шар бабіту на основі товщиною до
Перед встановленням вкладиші вкривають тонким шаром олова (0,002...0,003 мм) для швидкого припрацювання тертьових поверхонь, щільного їх прилягання і кращого відведення теплоти від підшипника.
Для компенсації подовження валапри нагріванні передбачено певний осьовий зазор. Обмежується осьове переміщення колінчастого вала більшості двигунів (в межах 0,1...0,5мм) різними способами: упорними півкільцями, ущільнювальними вкладишами і вставками, буртиками, виконаними на колінчастому валі тощо.
Підшипники корінні 14 і 15 і шатунні 2 (рис.4.9.2) складаються з двох сталевих вкладишів кожен, на які наноситься антифрикційний шар (АТ-20 або свинцева бронза). Для запобігання осьовому зсуву валу передбачається наполегливий підшипник ковзання (рис.4.9.3), що складається з двох кілець або чотирьох напівкілець 25 і 27 з антифрикційного матеріалу (бронза) цілком або із сталі, але з антифрикційними шаром.
Рис 4.9.3 Осьова фіксація колінчастого валу 1 – блок-картер; 2 і 5 – півкільця; 3 – кришка корінного підшипника; 4 – штифт стопорний; 6 – корінна шийка; | Рис 4.9.2 Деталі кривошипно-шатунного механізму двигуна ВАЗ – 2105: 1 – колінчастий вал; 2 – вкладиші підшипника нижньої головки шатуна; 3 – поршневий палець; 4 – шатун; 5 – болт кришки шатуна; 6 – кришка нижньої головки шатуна; 7 – головка поршня; 8 – бобишка; 9 – лунки; 10 – маховик; 11 – підшипник первинного валу коробки передач; 12 – зубчатий вінець маховика; 13 – наполегливе півкільце; 14 – вкладиші першого, другого, четвертого і п'ятого корінних підшипників; 15 – вкладиші третього (центрального) корінного підшипника; а – противага; б – шатунна шийка; в – корінна шийка; |
Рис. 4.9.4 Ущільнення колінчастого валу:
а – ущільнення переднього кінця валу; б – ущільнення заднього кінця валу; 1 – самопідтискний сальник; 2 – пилевидбивач; 3 – шків приводу водяного насоса, вентилятора і генератора; 4 – маточина; 5 – храповик; 6 – колінчастий вал; 7 – кришка блоку розподільних зубчатих коліс; 8 – передня нерухома шайба; 9 і 14 – штифти; 10 – блок циліндрів; 11 – задня нерухома шайба; 12 – вкладиш; 13 – кришка корінного підшипника; 15 – наполеглива шайба, що обертається; 16 – шпонка; 17 – розподільне зубчате колесо; 18 – оливовидбивач; 19 – оливовідбивний гребінь; 20 – болт кріплення маховика; 21 – оливосгінне різьблення; 22 – шарикопідшипник валу коробки передач; 23 – фланець; 24 – сальник; 25 – утримувач сальника; 26 маховик.
Ущільнення переднього і заднього кінців валу (рис.4.9.4) здійснюється гумовими самопідтискними сальниками 1 або азбестовим шнуром 24 (двигуни ГАЗ і ЗІЛ, Д - 65, Д - 240) (рис.4.9.5).
Для підвищення зносостійкості шийок їх гартують ТВЧ і шліфують, а перехід від шийки до щоки роблять плавним.
Сталеві вали виготовляють штампуванням, вали з високоміцного чавуну литвом.
Рис 4.9.5 Сальники колінчастого валу:
а – самопідтискної; б і в – задні двигунів ГАЗ; 1 – гумове кільце; 2 – стягнута пружина; 3 – утримувач ущільнювача; 4 – шнур ущільнювача; 5 – утримувач сальника; 6 – г- образний гумовий ущільнювач.
10. Маховик
Маховик служить для зменшення нерівномірності обертання колінчастого валу, накопичення енергії під час робочого ходу і використовування її для обертання валу під час підготовчих тактів, висновку деталей КШМ з мертвих точок, полегшення пуску двигуна і зрушення автомобіля з місця, а також для передачі моменту, що крутить, агрегати трансмісії.
Виготовляється маховик 10 (рис.4.9.2) з чавуну і піддається динамічному балансуванню в зборі з колінчастим валом і зчепленням. На колінчастому валу маховик встановлюється в строго певному положенні за допомогою несиметрично розташованих спеціальних штифтів або болтів кріплення до фланця або до торця колінчастого валу.
На обід маховика напресовується зубчатий вінець 12, призначений для обертання колінчастого валу стартером при пуску двигуна. На торець або обід маховика часто наносять мітки, по яких визначають положення поршня першого циліндра при установці запалення і моменту початку подачі палива
Технічне обслуговування кривошипно-шатунного механізму автомобільних двигунів
Технічний догляд за кривошипно-шатунний механізмом треба виконувати згідно з вимогами інструкції заводу-виготовника.
Для запобігання підвищеного спрацьовування деталей кривошипно-шатунного механізму тракторист зобов'язаний виконувати такі операції:
– При щоденному технічному обслуговуванні (ЛІТО) очищати двигун від пилу і бруду,
– Усувати підтікання охолоджувальної рідини і масла;
– Перевіряти зовнішнє кріплення деталей, звертаючи особливу увагу на щільність з'єднання повітроочисника і впускних трубопроводів;
– Перевіряти рівень і стан масла в картері двигуна; під час роботи слідкувати за тиском масла і кольором вихлопних газів, перевіряти роботу дизеля для виявлення сторонніх стуків;
– При перших ознаках ненормальної роботи потрібно усунути несправності;
- При першому і другому технічному обслуговуванні (ТО 1 і ТО 2) перевірити і при необхідності долити масло в картер двигуна; перевірити тиск масла в головній магістралі системи мащення. Зниження тиску масла до 0,15–0,10 МПа на прогрітому двигуні при працюючих агрегатах системи мащення і правильних показаннях манометра свідчить про значне спрацювання підшипників колінчастого вала;
+– При третьому технічному обслуговуванні (ТО 3) перевірити технічний стан циліндро-поршневої групи за кількістю газів, які надходять в картер двигуна, за допомогою індикатора витрати газів при роботі у номінальному режимі або вимірюванням компресії (тиск в циліндрі наприкінці такту стиску) за допомогою ком-пресіометра Для цього знімають головку циліндрів двигуна, очищають від нагару головку циліндрів і поршні, при необхідності міняють поршневі кільця і прокладку.
– Після встановлення головки циліндрів на блок-картер гайки шпильок необхідно затягувати у певній послідовності з необхідним моментом затягування гайок кріплення головки циліндрів.
Урок № 9-10
Комбіновані ґрунтообробні агрегати (машини) призначені для виконання за один прохід кількох технологічних операцій. Агрегати повинні виконувати тільки такі технологічні операції, які суміщуються в часі без порушення агротехнічних показників і строків виконання.
Використання комбінованих агрегатів значно зменшує ущільнення і розпилювання ґрунту ходовими системами агрегатів, скорочує строки виконання робіт, підвищує продуктивність праці та знижує витрати.
Розрізняють три основні типи комбінованих агрегатів: із кількох послідовно з'єднаних простих машин, кожна з яких виконує окрему операцію; машина з послідовно встановленими простими робочими органами для виконання кількох операцій; машина зі спеціальними комбінованими робочими органами для послідовного виконання технологічного процесу.
За послідовністю технологічних операцій, що виконуються при обробітку ґрунту, комбіновані машини поділяють на чотири основні групи:
- машини для суміщення основного та допоміжного (передпосівного) обробітку ґрунту;
- машини для суміщення операцій при передпосівному обробітку ґрунту;
- машини для суміщення основного або передпосівного обробітку ґрунту
з одночасним внесенням добрив;
- машини для суміщення передпосівного обробітку ґрунту і сівби.
Комбіновані агрегати АКП-2,5 та АКП-5 використовують для пошаро
вого основного обробітку ґрунту без обертання скиби під сівбу зернових,
пожнивних та деяких просапних культур.
Агрегат АКП-5 складається з передньої начіпної частини і приєднаної до неї причіпної задньої. На рамі передньої секції розміщені чотири дискові робочі секції (рис. 1.56), шість штоскорізальних лап 2, два опорних пневматичних колеса 4 і 7, начіпний пристрій 9, два гідроциліндри і маслопроводи.
Рис. 1.56. Агрегат комбінований ґрунтообробний АКП-5:
1 - вирівнювач; 2 — плоскорізальна лапа; 3 і 5 — секції дискових батарей; 4 і 7 - передні опорні пневматичні колеса; 6 - рама; 8 - гвинтовий механізм колеса; 9 - начіпний пристрій; 10 - задня рама; 11 - маслопроводи; 12 – заднє колесо; 13 і 14 — кільчасто-шпорові котки
Рама складається з основної центральної і двох шарнірне приєднаних бокових.
Кожна дискова секція має сім дисків діаметром 450 мм. Диски розміщені з кроком 185 мм.
Задня секція складається з трисекційної рами 10, восьми робочих секцій із двох рядів кільчасто-шпорових котків діаметром 520 мм, двох опорних пневматичних коліс 12, причіпного пристрою. До знижувачів рами і передньої частини причіпного пристрою приєднаний вирівнювач. Гідросистема агрегату забезпечує переведення бокових секцій у транспортне положення. Дискові батареї можуть бути зі сферичними або голчастими дисками.
Під час руху агрегату дискові батареї 3 і 5 розпушують ґрунт на глибину До 8 см, а плоскорізальні лапи 2 підрізують і розпушують його до 14 см, вирівнювач 1 вирівнює поверхню поля, а котки кільчасто-шпорові подрібнюють грудки й ущільнюють ґрунт.
Робоча ширина захвату агрегату -5м. Робоча швидкість - 7-10 км/год. Продуктивність - до 3,5-5,0 га/год. Агрегатують з тракторами класу 5.
Агрегати ґрунтообробні АГ-4, АПГ-4,5, Агро-КОГ-4,5призначені для безполицевого основного пошарового обробітку ґрунту з одночасним інтенсивним перемішуванням його з рослинними рештками і добривами під сівбу зернових культур і повторних посівів.
Агрегат АГ-4напівначіпний складається з основної рами 5 (рис. 1.57, а), двох передніх опорних металевих 1 і 4 та двох задніх 7 пневматичних коліс, п'яти плоскорізальних лап 2, батарей кільчасто-шпорових котків, двох секцій ротаційних борін 11 з ножеподібними зубами, причіпного пристрою 3, гвинтового механізму б, гідроциліндра 9 і маслопроводів 8.
Рис. 1.57. Агрегат ґрунтообробний АГ-4 (а) і культиватор ККП-3,7 (б): 1 і 4 — опорні металеві колеса; 2 - плоскорізальна лапа; 3 — причіпний пристрій; 5 — рама основна; 6 — гвинтовий механізм; 7 - опорне пневматичне колесо; 8 - маслопровід; 9 - гідроциліндр; 10 - кільчасто-шпоровий коток; 11 -ротаційна борона; 12 - секція котка; 13 - стрілчаста лапа; 14 - пневматичне колесо; 15 — дискова секція; 16 -рама; 17 - причіпний пристрій; 18 - гідроциліндр
Опорні металеві колеса мають гвинтові механізми для регулювання глибини ходу робочих органів. Гідроциліндр забезпечує переведення агрегату з робочого положення у транспортне.
Плоскорізальні лапи підрізують шар ґрунту на глибину до 16 см, ротаційні борони зубами інтенсивно розпушують, подрібнюють і перемішують ґрунт, рослинні рештки, а кільчасто-шпорові котки ущільнюють підпо-верхневий шар, подрібнюють грудки. За один прохід агрегат виконує три операції. Ширина захвату -4м. Робоча швидкість - 5-9 км/год. Продуктивність - 2,0-3,6 га/год. Агрегатують з тракторами класу 3.
Культиватор комбінований ККП-3,7 напівпричіпний, призначений для основного обробітку ґрунту після збирання зернових, високостеблових просапних культур і передпосівного обробітку ґрунту з питомим опором до 0,09 МПа.
Агрегатують його з тракторами Т-150, Т-150К, ХТЗ-161, ХТЗ-17021.
Культиватор складається з трьох дискових секцій 15 (рис. 1.57, б), рами 16, двох рядів стрілчастих плоскорізальних лап 13, трьох секцій пруткових котків 12 з підвісними рамками, опорних пневматичних коліс 14, причіпного пристрою 17, гідроциліндра 18 і маслопроводів.
Культиватор дисковими секціями розпушує верхній шар ґрунту, стрілчастими лапами підрізує кореневища бур'янів, розпушує нижній шар і котками подрібнює грудки та прикочує поверхню поля.
Підпружинені стояки стрілчастих лап забезпечують їх коливання у ґрунті, що підвищує ступінь розпушення і самоочищення від рослинних решток та бур'янів.
Глибина обробітку - до 16 см. Ширина захвату - 3,7 м. Робоча швидкість - 6-10 км/год. Продуктивність - 2,3-3,7 га/год.
Агрегати чизельні АЧП-2,5 і АЧП-4,5 призначені для глибокого розпушення ґрунту, руйнування плужної підошви, поглиблення орного шару.
Робочими органами агрегатів є розпушувальні долотоподібні або стрілчасті лапи на жорстких стояках і ротаційні борони. Ширина захвату долотоподібних лап - 70 мм, а стрілчастих - 270 мм. Лапи розміщують на рамі в поперечному напрямку з кроком 40 або 50 см.
Ширина захвату агрегатів АЧП-2,5 і АЧП-4,5 відповідно 2,5 і 4,5, агрегатують їх з тракторами класу 3 і 5. Робоча швидкість - до 8 км/год.
Агрегати комбіновані АКШ-3,6 і АКШ-5,6 призначені для безполице-вого основного, післязбирального, пошарового, передпосівного обробітку ґрунту з якісним розпушенням та інтенсивним подрібненням грудок, за-робки органічних та мінеральних добрив при застосуванні традиційної системи землеробства і використанні ґрунтозахисних технологій.
Агрегат АКШ-3,6 начіпний, складається з рами 3 (рис. 1.58), двох передніх металевих опорних коліс 4 з гвинтовими механізмами 5, начіпно-го пристрою 6, двох рядів плоскорізальних лап (ножів), двох секцій дискових батарей, гнучкої ротаційної борони 10. В передній частині плоско-різальної лапи закріплений горизонтальний ніж з направленим твердим сплавом вздовж леза для подовження строку роботи. Дискова секція має дві послідовно розміщені батареї. Диски кожної батареї плоскі з вирізами і встановлені під невеликим кутом атаки. Під час руху вони коливаються в поперечному напрямку. Ротаційна борона має загострені пруткові зуби і закріплена на двох кронштейнах 12. Підіймальним пристроєм 8 і кронштейнами 12 вона утримується на заданій висоті від поверхні поля.
Рис. 1.58. Агрегат комбінований АКІП-3,6:
1 і 2 — плоскорізальні лапи; 3 — рама; 4 — опорне металеве колесо; 5 - гвинтовий механізм; 6 - начіпний пристрій; 7 - поздовжній брус; 8 - підіймальний пристрій; 9 - заднє опорне колесо; 10 -ротаційна борона; 11 - зуб борони; 12 - кронштейн; 13 і 14 - батареї дисків
Під час роботи агрегату плоскорізальні лапи ножами підрізують і частково піднімають шар ґрунту, диски секцій подрібнюють, змішують і перемішують ґрунт, а гнучка ротаційна самоочисна борона розпушує, вирівнює його, вириває, вичісує бур'яни і викидає їх на поверхню поля, закриває вологу. Глибина обробітку - 5-20 см. Ширина захвату - 3,6 м. Робоча швидкість - 6-15 км/год. Продуктивність - 3-6 га/год. Агрегатують з тракторами Т-150, ХТЗ-17021 та ін.
Агрегат АГРО-3 напівначіпний, ротаційний, призначений для безпо-лицевого основного і передпосівного обробітку стерньових агрофонів після збирання зернових, просапних та інших культур.
Агрегат (рис. 1.59) складається з двох рядів розпушувальних лап 1 і 2, передньої 3 і задньої 5 дискових робочих тандем-секцій, передніх опорних металевих і задніх 4 двох пневматичних коліс, двох поздовжніх брусів з трьома допоміжними рамами, до яких кріпляться робочі органи, і причіпного пристрою.
Кожна дискова секція має по дві батареї плоских зірчастих дисків. Диски задньої батареї зміщені вбік і входять у проміжки між дисками переднього ряду. Диски батарей мають гострі і відігнуті вбік під невеликим кутом зуби.
Під час руху агрегату в полі розпушувальні лапи підрізують, розпушують ґрунт, а робочі тандем-секції зірчастих дисків розрізують ґрунт, подрібнюють грудки, стерню, рослинні рештки та інтенсивно перемішують їх. Глибина обробітку - 5-15 см.
Агрегат дозволяє змінювати послідовність розміщення робочих органів для обробітку ґрунту після різних попередників. Дискову секцію встановлюють у передній частині рами, а розпушувальні лапи - в середній, між дисковими тандем-секціями.
Рис. 1.59. Схема розміщення робочих органів
Ґрунтообробного агрегату АГРО-3 (а) і дискова секція (б):
1 і 2 — розпушувальні лапи; 3 - передня секція зірчастих дисків; 4 — опорне пневматичне колесо; 5 — задня секція зірчастих дисків; 6 — вісь передньої батареї дисків; 7 - плоский зірчастий диск; 8 - вісь задньої батареї дисків
Ґрунтообробні агрегати такого типу називаються мультитіллери. Серед зарубіжних конструкцій використовують агрегат фірми RAU.
Ширина захвату агрегату АГРО-3 -Зм. Робоча швидкість - 8-9 км/год. Продуктивність - 2,4-2,7 га/год. Агрегатують з тракторами класу 5 типу Європака.
Агрегати ґрунтообробні АГ-6, АКГ-6, АП-6, АПБ-6 і КАПП-6призначені для передпосівного обробітку ґрунту, закриття вологи, інтенсивного розпушування, подрібнення, ущільнення ґрунту, вирівнювання поверхні поля.
Агрегат АГ-6напівначіпний, складається з основної рами 23 (рис. 1.60), двох опорних пневматичних коліс 9, двох рухомих рам, переднього 19 і заднього 14 вирівнювальних брусів, передніх розпушувальних зубів 21, тандем-котків 11 і 12, трьох рядів розпушувальних лап 16, переднього пруткового котка 18, гідроциліндрів 3, 6 і 8, маслопроводів 4 і причіпного пристрою 1.
Передній вирівнювальний брус 19, коток 18 і розпушувальні зуби 16 кріпляться до рами за допомогою підвіски 17, а тандем-котки і пружинна борона 10 приєднані до задньої підпружиненої підвіски 13.
Під час руху агрегату розпушувальні зуби 21 розпушують сліди коліс трактора, передній вирівнювальний брус 19 частково вирівнює поверхню поля, котки пруткові 18 подрібнюють грудки, частково ущільнюють ґрунт, лапи на пружинних стояках 16 розпушують ґрунт на глибину до 15 см, далі другий вирівнювальний брус 14 вирівнює поверхню поля, тандем-котки подрібнюють грудки, ущільнюють поверхневий шар, а борона пружинна 10 забезпечує оптимальну верхню структуру ґрунту.
Глибину обробітку регулюють переміщенням передньої підвіски котка і розпушувальних лап. Ступінь подрібнення грудок регулюють зусиллям пружини задньої підвіски.
Рис. 1.60. Схема агрегату ґрунтообробного АГ-6:
1 — причіпний пристрій; 215- пальці; 3, 6 і 8 — гідроциліндри; 4 - маслопроводи; 7 - кронштейн; 9 - опорне колесо; 10 - зуб пружинної борони; 11 і 12 - котки задньої секції; 13 і 17 - підвіски; 14 і 19 - вирівнювальні бруси; 15, 20 і 22 - пружини; 16 - розпушувальні лапи; 18 - коток прутковий; 21 - розпушувальні зуби; 23 - основна рама
Ширина захвату агрегату -6м. Робоча швидкість - до 10 км/год. Продуктивність - до 6 га/год. Агрегатують з тракторами класу 3.
Агрегат ґрунтообробний АП-3,7 начіпний, призначений для закриття вологи, передпосівного обробітку ґрунту.
АП-3,7 складається з рами 7 (рис. 1.61, а), підпружиненого вирівнювального бруса 1, чотирьох рядів розпушувальних лап 3 на пружних стояках, підпружинених пруткових котків 4, двох опорних пневматичних коліс 2 і начіпного пристрою 6. За один прохід агрегат виконує інтенсивне розпушування ґрунту на глибину до 12 см, вирівнювання поверхні поля за допомогою підпружиненого вирівнювального бруса 1, подрібнення грудок і прикотковування.
Робоча ширина захвату агрегату - 3,7 м. Робоча швидкість -8-10 км/год. Продуктивність - 3,0-3,7 га/год.
Ґрунтообробні агрегати РВК-3,6, РВК-5,4 і РВК-7,2 застосовують для передпосівного обробітку ґрунту на глибину до 12-15 см. Вони розпушують ґрунт, руйнують грудки, брили, вирівнюють мікрорельєф і прикотковують.
Робочими органами агрегатів є послідовно розміщені: передній ряд 8 (рис. 1.61, б) розпушувальних лап на пружних стояках, передній розріджений кільчасто-шпоровий коток 9 з дисками діаметром 520 мм, далі - другий ряд 10 розпушувальних лап на пружних стояках, за ним - металевий брус 11 для вирівнювання ґрунту і позаду - кільчасто-шпоровий коток 12.
Ширина захвату агрегатів РВК-3,6, РВК-5,4 і РВК-72 відповідно 3,6; 5,4 і 7,2 м. Робоча швидкість - 8-11 км/год.
Комбіновану машину ВИП-5,6 застосовують для передпосівного обробітку ґрунту під зернові, технічні та овочеві культури.
Машина складається із двох задніх та однієї передньої секцій. Кожна секція має голчасту ротаційну мотику, вирівнювальний брус та кільчасто-зубчастий коток (рис. 1.61, в).
Ротаційна мотика складається з батарей голчастих дисків 13, які вільно обертаються на осі.
Рис. 1.61. Агрегат передпосівний АП-3,7 (а),
Ґрунтообробний агрегат РВК-3,6 (б) і машина ВИП-5,6 (в):
1, 11 і 14 - вирівнюючі бруси; 2 - опорне колесо; 3, 8 і 10 – розпушувальні лапи; 4 - коток прутковий; 5 - штанга з пружиною; 6 - начіпний пристрій; 7 -рама; 9 і 12 - кільчасто-шпорові котки; 13 - голчастий диск; 15 - коток
Вирівнювальний брус 14 шарнірно приєднаний до рами і підпружине-ний. Кільчасто-зубчастий коток 15 складається із зубчастих кілець та клиноподібних дисків.
Під час руху машини голчасті диски розпушують ґрунт, подрібнюють грудки, вирівнювальний брус вирівнює поверхню поля, а коток ущільнює ґрунт.
Робоча ширина захвату машини - 5,6 м. Робоча швидкість -6-8 км/год., продуктивність - 3,3-4,5 га/год. Машину агрегатують із тракторами класу 1,4 ІЗ.
Машини для суміщення основного або передпосівного обробітку ґрунту з одночасним внесенням добрив. Внесення рідких мінеральних добрив під час оранки, культивації проводиться комбінованими агрегатами, які складені з простих машин: плуга або культиватора і підживлювача рідких мінеральних добрив та ін.
Використовуються також і спеціальні комбіновані ґрунтообробні машини, які укомплектовані висівними апаратами для твердих мінеральних добрив. Сюди слід віднести комбіновану машину МКП-4 та культива-тори-глибокорозпушувачі-удобрювачі типу ГУН-4 та ін.
Машини для суміщення передпосівного обробітку ґрунту і сівби. Комбіновані агрегати, що проводять передпосівний обробіток ґрунту і сівбу, можуть складатись із окремих простих машин (культиватора і сівалки), але є і спеціальні ґрунтообробно-посівні агрегати.
Найпростішим комбінованим агрегатом є агрегат ЗКА-3,6, складений з культиватора типу КПС-4 і зернотукової сівалки.До спеціальних комбінованих машин, які проводять культивацію і сівбу одночасно, відносяться сівалки-культиватори, лущильники-сівалки, фрезерні культиватори-сівалки та комбінований агрегат КА-3,6.
Комбінований агрегат КА-3,6застосовують для проведення передпосівного обробітку важких ґрунтів, сівби зернових та зернобобових культур з одночасним внесенням добрив та прикотковування рядків.
Агрегат складається з начіпного фрезерного культиватора КФГ-3,6 (рис. 1.62), зернотукової сівалки та прикотковуючого пристрою (клинчасті котки).
Рис. 1.62. Комбінований агрегат КА-3,6:
1 — опорне колесо; 2 - стрілчаста лапа; 3 — ґрунтообробна фреза; 4 - фартух; 5 — зернотукова сівалка; 6 — котки
При роботі агрегату ножі фрезбарабана розпушують ґрунт, робочі органи сівалки утворюють борозни і подають на дно їх насіння та добрива, а клинчасті котки ущільнюють ґрунт у рядках.
Ширина захвату агрегату - 3,6 м. Робоча швидкість - до 7-9 км/год. Продуктивність - до 2,7 га/год.
Компетенція №5-6 Особливості конструкції дизельних двигунів.
1. Про дизельний двигун
2. Будова дизельного двигуна
3. Системи дизельного двигуна:
— Система Common Rail
— Випускна система
— Система рециркуляції відпр. газів
— Впускна система
— Турбонаддув дизеля
— Система передпускового підігрівання
4. Як працює дизельний двигун
5. Про дизельний двигун e-HDi
Дизельний двигун
Дизельний двигун — це поршневий двигун внутрішнього згорання, який працює на дизельному пальному. Основна відмінність дизельного двигуна від бензинового полягає у способі подачі паливо-повітряної суміші в циліндр і способі її загоряння. В бензиновому двигуні пальне змішується із повітрям до потрапляння в циліндр, отримана суміш підпалюється в потрібний момент свічкою запалювання. В дизельному двигуні повітря подається в циліндр окремо від пального і потім стискається. Через високу ступінь стискання, коли повітря нагрівається, до температури самозапалювання пального (700-800°C), воно впорскується в камери згоряння форсунками під великим тиском.
Дизельний двигун використовує в своїй роботі термодинамічний цикл Дизеля або (частіше) цикл Трінклера Сабате. Ці цикли вирізняються великим ККД порівняно з циклом Отто, який використовується в бензинових двигунах. Саме завдяки високій ефективності дизельний двигун спочатку почав використовуватися на вантажних автомобілях, а згодом і більшість легкових авто отримали в свої лінійки моторів дизельні двигуни. Так, зараз в Європі дизель поступово витісняє бензинові двигуни, наприклад, більше 50% нових легкових автомобілів там мають саме дизельний двигун.
Будова дизельного двигуна
Через наведені вище нюанси конструкції в дизельному двигуні відсутні не тільки свічки, але і вся система запалювання, що значно спрощує конструкцію і підвищує надійність. На противагу цьому паливна система дизельного двигуна суттєво відрізняється від бензинового в сторону ускладнень. В основному через високий тиск в системі і підвищення вимог до точності подачі пального.
Для основні елементи паливної системи дизеля — це ПНВТ (паливний насос високого тиску) і форсунки. ПНВТ забезпечує подачу пального від паливного баку, через фільтр до форсунок. Форсунки вприскують пальне в камери згорання в потрібний час і в потрібній кількості. Алгоритм системи має наступний вигляд.
ПНВТ (2) забирає пальне з паливного баку (7) по трубопроводу (8) через паливний фільтр (1). Далі по трубопроводу (6) під високим тиском пальне подається до форсунок (5), які вприскують пальне в камери згорання. Частина пального, не використана під час вприскування, поступає назад в бак по трубопроводу (4). Схема трохи спрощена, але саме так в дизельному двигуні все і працює.
До речі, свічки в дизельному двигуні все таки є, але виконують вони зовсім інше функцію і називаються свічками розжарювання. Їх завдання — розігріти камеру згорання для полегшення холодного пуску, тобто це, по суті, просто елемент для нагрівання. Давайте розберемося в ще декількох системах і термінах, які часто зустрічаються в зв’язку з дизельним двигуном.
Системи дизельного двигуна
Основними напрямками вдосконалення дизельних двигунів є зниження витрати пального, токсичності відпрацьованих газів, рівня шуму, підвищення потужності двигуна, полегшення холодного запуску. Для реалізації цих вимог на сучасних дизельних двигунах застосовується цілий ряд систем: Common Rail, впускна і випускна системи, система рециркуляції відпрацьованих газів, турбонаддув, система передпускового підігріву.
Система Common Rail
Система Common rail (комон-рейл) – це система подачі пального в дизельних двигунах, яка була винайдена відносно недавно. Суть в тому, що ПНВТ подає пальне не на кожну форсунку безпосередньо, а в загальну рампу. Далі, сучасні електронні форсунки забирають пальне з рампи і впорскують безпосередньо в циліндри. Вся система керується електронікою і дозволяє здійснювати впорскування з максимальною точністю.
Завдяки цій, по суті, революційній технології дизельні двигуни отримали унікальні технічні характеристики, які рніше були їм недоступними. Ця система позбавила дизельні двигуни багатьох недоліків, властивим попереднім поколінням дизелів. Загалом, саме система Common rail наблизила дизельні двигуни за характеристиками до бензинових побратимів, а в дечому і взагалі дозволила їх обійти.
Випускна система дизельного двигуна
Випускна система сучасного дизельного двигуна орієнтована на зниження у відпрацьованих газах сажі, неспалених вуглеводнів і оксидів азоту. Для цього в системі встановлюється спеціальний сажний фільтр. Накопичена у фільтрі сажа видаляється шляхом регенерації.
Система рециркуляції відпрацьованих газів
Система рециркуляції відпрацьованих газів призначена для зниження вмісту у відпрацьованих газах оксиду азоту. Для цього частина газів повертається у впускний колектор. Підвищення ефективності роботи системи забезпечується завдяки примусовому охолодженню відпрацьованих газів у спеціального охолоджувачі, який вбудований в систему охолодження двигуна.
Впускна система дизельного двигуна
Впускна система сучасного дизельного двигуна може обладнуватися впускними заслінками. Застосування заслінок утворює два канали всмоктування, забезпечує завихрення повітряного потоку і покращення утворення суміші на всіх режимах. При запуску двигуна і роботі на низьких обертах заслінки закриті, при високій частоті обертання колінчастого валу і високому обертовому моменті — відкриті. Закриття заслінок приводить до зниження у відпрацьованих газуах оксиду вуглецю і неспалених вуглеводнів.
Турбонаддув дизеля
Турбонаддув — вид наддуву, при якому повітря в циліндри двигуна подається під тиском за рахунок використання енергії відпрацьованих газів. На даний момент турбонаддув є найефективнішою системою підвищення потужності двигуна без збільшення частоти обертання колінчастого валу і об’єму циліндрів. Окрім підвищення потужності турбонаддув забезпечує економію пального в розрахунку на одиницю потужності і зниження токсичності відпрацьованих газів за рахунок більш повного згорання пального.
Система турбонаддуву встановлюється не тільки на дизельний, а й на бензинових двигунах. Однак найефективнішим турбонаддува є саме на дизелях (за рахунок високого степеня стискання і відносно невисокої частоти обертання колінчастого валу.
Система передпускового підігрівання
Для забезпечення запуску дизельного двигуна в холодну пору застосовується система передпускового розігріву, яка представляє собою вище згадані електронно-керовані свічки розжарювання, встановлені у впускному колекторі. Крім цієї системи додатково на автомобіль може встановлюватися підігрівач дизельного пального.
Як працює дизельний двигун
Принцип роботи чотиритактного дизельного двигуна заснований на займанні робочої суміші (повітря+паливо) при дуже високому тиску. Відрізняється дизельний від бензинового, тим, що утворення суміші у нього відбувається безпосередньо в камері згорання, а не в карбюраторі (повітря може нагнітатися турбіною).
Такти роботи дизельного двигуна:
- Такт впускання, при якому відкривається впускний клапан і циліндр заповнюється повітрям. Клапан через деякий час закривається.
- Такт стискування. Поршень починає рухатися вгору і стискати повітря. Трохи не доходячи до верхньої мертвої точки поршня, в циліндр упорскує через форсунку паливо.
- Робочий такт. Вибух суміші, при цьому розширення газів примушує рухатися поршень вниз, зрештою повернути колінчастий вал і маховик, здійснюючи роботу.
- Такт випуску, при якому відкривається випускний клапан і усі відпрацьовані гази виштовхуються поршнем назовні.
Про сучасний дизельний двигун e-HDi
Мікро-гібридна технологія e-HDI — це нова розробка компанії Citroen і групи PSA, направлена на зниження витрати пального і зменшення кількості вихлопних газів. Про всі переваги дизельних двигунів e-HDI дивіться на відео нижче.
Немає коментарів:
Дописати коментар