Урок № 15
Тема: Наpiзуванняpiзі,
клепання, пpитиpання, паяння, запресовування i випpесовування
1. Пpофiлi та стандаpти piзі. Класи точностipiзі.
Iнстpументи для нарізування зовнiшньої та ввутрішньої piзі. Пеpевipка piзі piземipом
i наpiзними калiбpами. Бpак пiд час нарізування piзі, пpичини та запобiгання.
2. Застосування клепання. Метали, що викоpистовуються для
заклепок. Клепання холодне i гаpяче, фоpми головок заклепок. Iнстpумент для
клепання, його будова i застосування.
3. Пpизначення i застосування пpитиpки.
4. Матеpiали для пpитиpання. Веpстати для пpитиpання, їх
будова та застосування. Ручне притирання, iнструменти для ручного притирання.
Контpоль за якiстю пpитиpання.
5. Застосування паяння. Iнстpумент, пpистpої, обладнання
та матеpiали, що викоpистовуютьсяпiд час паяння.
6. Застосування запpесування i випpесування. Iнстpументи,
пpистpої та обладнання, що викоpистовуються пiд час запpесування та
випpесування. Нагpiвання i гаpяча посадка. Нагpiвання i випpесування.
7. Можливi дефекти пiд час запpесування i випpесування,
заходи запобiгання.
8. Пpавила безпеки праці пiд час нарізування piзі,
клепання, пpитиpання, паяння та pоботи на пpесi.
Урок №14
Тема: Свеpдлiння,
зенкування i pозвеpтання отворів.
1. Застосування свеpдлiння пiд час обpобки металiв.
Свеpдла, їх констpукцiї, кути заточування, сфеpа застосування. Охолодження i
змащення пiд час свеpдлiння. Види свеpдлiння.
2. Ручнi, пневматичнi та електpичнi дpилi, їх будова.
Пpичини поломки свеpдел та заходи запобiгання. Бpак пiд час свеpдлiння.
3. Пpизначення зенкеpування i зенкування. Будова зенкеpа
i зенкiвки. Пpизначення pозвеpтання. Розвеpтки та їх види.
4. Безпека праці пiд час свеpдлiння, зенкування та
pозвеpтання.
Конспект:
Свердління – один з найпоширеніших методів здобуття отвору різанням. Ріжучим інструментом тут служить свердло, яке дає можливість як отримувати отвори в суцільному матеріалі (свердління), так і збільшувати діаметр вже просвердленого отвору (розсвердлювання).
Мал. 4.14. Робота свердла при свердлінні
При свердлінні оброблювану деталь закріплюють на столі свердлильного верстата прихватами, в лещатах, на призмах і т. п., а зверху надають два спільні рухи (мал. 4.14) обертове v і поступальне (направлене уздовж осі свердла) s. Обертальний рух свердла називається головним (робочим) рухом. Поступальний рух уздовж осі свердла називається рухом подачі.
Свердління виконується на приводних свердлильних верстатах і вручну – ручними дрилями, за допомогою механізованого інструменту – електричними і пневматичними дрилями, а також електроіскровим і ультразвуковим методами. Мал. 4.15. Електрична дриль
Свердла, їх конструкції і призначення
По конструкції і призначенню свердла підрозділяються на ряд видів.
Перові свердла є простим ріжучим інструментом (мал. 4.16, а). Вони застосовуються головним чином в ручних дрилях для свердління невідповідальних отворів діаметром до 25 мм.
Мал. 4.16. Різноманітні конструкції свердел
Спіральні свердла з циліндричним і конічним хвостовиками (мал. 4.16, б, в) використовуються як для ручного свердління, так і при роботі на верстатах (свердлильних, револьверних і ін.).
Свердла для глибокого свердління застосовуються на спеціальних верстатах для здобуття точних отворів малого діаметру. Під глибоким свердлінням зазвичай розуміють свердління отворів, довжина яких перевищує їх діаметр в 5 разів і більш.
Центрові свердла (мал. 4.16, г) служать для здобуття центрових поглиблень на оброблюваних деталях.
Комбінований інструмент для обробки отворів дозволяє виконувати одночасну обробку одноосних отворів (мал. 4.16, д), а також одночасне свердління і зенкування або розвертання отворів (див., наприклад, мал.. 4.16, е).
Для виготовлення свердел, як правило, застосовують наступні інструментальні матеріали: вуглецеву інструментальну сталь марок У10А і У12А, леговані сталі – хромисту марки X і хромокремнієву 9ХС; швидкоріжучу сталь марок Р9 і Р18. Останніми роками для оснащення ріжучих кромок свердел стали застосовувати пластинки твердих сплавів марок ВК6, ВК8, Т15К6 і ін.
Свердла з швидкоріжучих сталей роблять зварними: робочу частину – з швидкоріжучої сталі, а іншу частину – з менш дорогої конструкційної сталі. Найбільш поширеними є спіральні свердла з швидкорізальних сталей.
Елементи і геометричні параметри спірального свердла
Спіральне свердло має робочу частину, шийку, хвостовик для кріплення свердла в шпинделі верстата чи дрилі і лапку, яка слугує упором при вибиванні свердла з гнізда шпинделя і передачі через неї великих крутячих моментів (мал. 4.17, а). Робоча частина, у свою чергу, розділяється на ріжучу і направляючу.
Мал. 4.17. Елементи спірального свердла
Ріжуча частина, на якій розташовані всі ріжучі елементи свердла, складається: з двох зубів (пер), утворених двома спіральними канавками для відведення стружки (мал. 4.17, б); перемички (серцевини) – середньої частини свердла, що сполучає обидва зуба (пера); двох передніх поверхонь, по яких збігає стружка, і двох задніх поверхонь; двох стрічок, які слугують для направлення свердла, калібрування отвору і зменшення тертя свердла об стінки отвору; двох головних ріжучих кромок, утворених перетином передніх і задніх поверхонь і виконуючих основну роботу різання; поперечної кромки (перемички), утвореної перетином обох задніх поверхонь. На зовнішній поверхні свердла між краєм стрічки і канавкою розташована дещо поглиблена частина, яка йде по гвинтовій лінії і називається спинкою зуба.
Зменшення тертя свердла об стінки просвердлюваного отвору досягається також тим, що робоча частина свердла має зворотний конус, тобто діаметр свердла в ріжучій частині більший, ніж на іншому кінці, біля хвостовика. Різниця у величині цих діаметрів складає 0,03-0,12 мм на кожних 100 мм довжини свердла.
До геометричних параметрів ріжучої частини свердла (мал. 4.18) відносяться: кут при вершині свердла, кут нахилу гвинтової канавки, передній і задній кути, кут нахилу поперечної кромки (перемички).
Мал. 4.18. Геометричні параметри спірального свердла
Кут при вершині свердла 2φ розташований між головними ріжучими кромками. Він робить великий вплив на роботу свердла. Величина цього кута вибирається залежно від твердості оброблюваного матеріалу і коливається в межах від 800 до 1400; для сталей, чавунів і твердих бронз 2φ = 116-1180, для латуні і м’яких бронз 2φ = 1300, для легких сплавів – дюралюміну, силуміну 2φ = 1400; для червоної міді 2φ = 1250; для ебоніту і целулоїду 2φ = 80-900.
Для підвищення стійкості свердел діаметром 12 мм і вище застосовують подвійне заточування свердел; при цьому головні ріжучі кромки мають форму не прямої, як при звичайному заточуванні (мал. 4.18, а), а ламаної лінії (мал. 4.18, б). Основний кут 2φ = 116-1180 (для сталей і чавунів), а другий кут 2φ0 = 70-750.
Кут нахилу гвинтової канавки позначається грецькою буквою омега ω (мал. 4.18, а). Із збільшенням цього кута процес різання полегшується, покращується вихід стружки. Проте свердло (особливо малого діаметру) із збільшенням кута нахилу гвинтової канавки ослаблюється. Тому в свердел малого діаметру цей кут робиться меншим, ніж в свердел великого діаметру.
Кут нахилу гвинтової канавки повинен вибиратися залежно від властивостей оброблюваного металу. Для обробки, наприклад, червоної міді і алюмінію цей кут потрібно брати рівним 35-400, а для обробки сталі ω = 250 і менше.
На мал. 4.18, в зображено приклад кутів φ = 1180, ω = 270.
Мал. 4.19. Заточка ріжучих кромок свердла: а – положення свердла в руках, б – положення свердла відносно шліфувального круга
Свердлильні станки
Мал. 4.20. Вертикально-свердлильний станок моделі 2135: 1 – основа, 2 – стіл, 3 – шпиндельний вузол, 4 – направляючий кронштейн, 5 – коробка швидкостей, 6 – колона
Мал. 4.21. Радіально-свердлильний станок: 1 – основа, 2 – нерухома колона, 3 – обертова колона, 4 – траверса, 5 – механізм підйому і опускання траверси, 6 – свердлильна головка, 7 – шпиндель
Процес різання при свердлінні
В процесі свердління під впливом сили різання ріжучі поверхні свердла стискують прилеглі до них частки металу, і коли тиск, що створюється свердлом, перевищує сили зчеплення часток металу, відбувається утворення елементів стружки і відділення її.
При свердлінні в’язких металів (сталь, мідь, алюміній і ін.) окремі елементи стружки, щільно зчіплюючись між собою, утворюють безперервну стружку, що завивається в спіраль (див. мал. 4.14). Така стружка називається зливною. Якщо оброблюваний метал крихкий, наприклад чавун або бронза, то окремі елементи стружки надламуються і відокремлюються один від одного. Така стружка, що складається з окремих роз’єднаних між собою елементів (лусочок) неправильної форми, носить назву стружки надлому.
Прийоми свердління
Залежно від точності і величини партії оброблюваних деталей свердління отворів може виконуватися по розмітці з накернюванням центрів отворів або по кондукторах.
Свердління по розмітці при відносно точному положенні отвору виконують в два прийоми: спочатку свердлять отвір попередньо, а потім остаточно. Попереднє свердління виконують з ручною подачею на глибину 0,25 діаметра отвору, потім свердло піднімають, видаляють стружку і перевіряють збіг кола надсверленного отвору з розмічальним колом. Якщо вони збігаються, то можна продовжувати свердління, включивши механічну подачу, і довести його до кінця. Якщо ж надсверлений отвір виявився не в центрі, то його виправляють шляхом прорубування двох-трьох канавок від центру з того боку центрального поглиблення, куди потрібно змістити свердло. Канавки направлять свердло в намічене кернером місце. Зробивши ще одне надсверлювання і переконавшись в його правильності, доводять свердління до кінця.
Мал. 4.22. Свердління в кондукторах: а – в закритому (коробчастому), б – в накладному
Свердління по кондуктору виконують в тих випадках, коли потрібно отримати вищу точність, а також при великій партії однакових деталей. Цей спосіб набагато продуктивніший свердління по розмітці, оскільки відпадає потреба в самій розмітці, у витримці деталі перед її обробкою; кріплення деталі виконується надійно і швидко; знижується стомлюваність робітника і т. п. Наявність постійних настановних баз і кондукторних втулок, що направляють інструмент, підвищує точність обробки і забезпечує взаємозамінність деталей.
На мал. 4.22, а зображений закритий кондуктор коробчастої форми. Оброблювану деталь закривають усередині коробки 1, доводять до упору 2 і кріплять гвинтами 4 і 6. Свердло спочатку вводять в направляючу втулку 3, а потім, просвердливши отвір і пересунувши кондуктор, просвердлюють другий отвір через направляючу втулку 5.
При користуванні накладними кондукторами оброблювану деталь затискають в машинних лещатах або на столі верстата.
Кондуктор 3 накладають на ту частину поверхні деталі 1, де потрібно просвердлити отвір (мал. 4.22, б). Кріплять кондуктор на деталі бічними гвинтами 2 або притисками різних конструкцій.
Свердління прохідних отворів відрізняється від свердління глухих отворів. Коли свердло підходить до виходу з отвору, опір металу значно зменшується, і відповідно має бути зменшена подача. Якщо подачу не зменшити, то свердло різко опуститься, захопить великий шар металу, заклиниться і може зламатися. Зазвичай для того, щоб уникнути цього, в кінці свердління вимикають механічну подачу свердла і досвердлюють отвір з ручною сповільненою подачею.
Свердління глухих отворів на задану глибину вимагає попереднього налаштування по спеціальному пристосуванню, що є на свердлильному верстаті. Якщо ж такого пристосування немає, користуються упорною втулкою, закріпленою в потрібному місці безпосередньо на свердлі (мал. 4.23).
Мал. 4.23. Свердління глухих отворів по упору: 1 – упорна втулка, 2 – стопорний гвинт, 3 – деталь
Упорну втулку або пристосування для роботи по упору, змонтоване на шпинделі, настроюють так. Свердло опускають на деталь, а упорний стержень (втулку) встановлюють і закріплюють на висоті, що відповідає глибині свердління. Коли свердло опуститься на встановлену глибину, упорний стержень або втулка дійдуть до обмежувача або торця і зупиняться. При цьому шпиндель (свердло) не зможе пройти далі в метал.
Мал. 4.24. Свердління неповних отворів
Свердління неповних отворів виконують двома способами. За першим способом пару деталей закріплюють в лещатах так, щоб їх поверхні, на яких мають бути просвердлені неповні отвори, збіглися. Потім розмічають на лінії стику закріплених деталей центри отворів і виконують свердління звичайним способом (мал. 4.24, а). При свердлінні неповного отвору в одній деталі користуються прокладками з того ж матеріалу, що й деталь, яка обробляється (мал. 4.24, б).
Зенкування, зенкерування і розвертання
Зенкуванням називається обробка вхідної або вихідної частини отвору з метою зняття фасок, задирок, а також утворення поглиблень під голівки болтів, гвинтів і заклепок. Інструменти, що використовуються для цієї мети, називаються зенковками. За формою ріжучої частини зенковки поділяються на конічні і циліндричні (мал. 4.25).
Мал. 4.25. Зенковки і приклади обробки ними отворів: а – конічні, б – циліндричні
Мал. 4.26. Зенкери: а – цільний, б – насадний, в – зі вставними ножами
Зенкеруванням називається обробка (розширення) заздалегідь просвердлених штампованих або литих отворів з метою надання їм строгої циліндричної форми, досягнення більшої точності і чистоти поверхні. Зенкерування забезпечує здобуття отворів 4-5-го класів точності. Отвори 2-3-го класів точності виходять розвертанням. Тому зенкерування застосовують переважно як проміжну операцію між свердлінням і розвертанням. Інструменти, що використовуються для цієї технологічної операції, називаються зенкерами (мал. 4.26).
Зенкеруванням обробляються також литі, штамповані і прошиті в кузні отвори.
Зенкери відрізняються від свердел влаштуванням ріжучої частини і великим числом ріжучих кромок. Велика кількість направляючих стрічок забезпечує правильне і стійкіше положення зенкера відносно осі оброблюваного отвору, а розподіл зусиль на три-чотири ріжучі кромки – більш плавну, ніж при свердлінні, роботу і отримання чистого і достатньо точного отвору.
Розвертання є операцією чистової обробки отворів, що забезпечує високу точність розмірів і чистоту поверхні. Ця операція виконується за допомогою інструменту, що називається розверткою (мал. 4.27).
Мал. 4.27. Основні типии розверток: а-д – циліндричні, е-з – конічні
Основні види браку при свердлінні отворів
Груба поверхня просвердленого отвору виходить при роботі тупим або неправильно заточеним свердлом при великій величині подачі і недостатньому охолоджуванні свердла. Для запобігання цьому виду браку потрібно перед початком роботи перевірити шаблоном правильність заточування свердла, працювати лише по режимах, вказаних в технологічній карті, своєчасно регулювати подачу охолоджуючої рідини на свердло.
Діаметр просвердленого отвору, що перевищує заданий, виходить унаслідок неправильного вибору розміру свердла, неправильного його заточування (нерівні кути в ріжучих кромок, ріжучі кромки різної довжини, зсув поперечної кромки свердла), наявність люфта у вузлі шпинделя верстата і ін. Щоб уникнути цього вигляду браку необхідно до початку роботи перевірити заточування свердла, вибрати свердло необхідних розмірів, перевірити положення шпинделя і ретельно відрегулювати його.
Зсув осі отвору виходить в результаті неправильної розмітки деталі (при свердлінні по розмітці), неправильної установки і слабкого кріплення деталі на столі верстата (деталь зрушилася при свердлінні), биття свердла в шпинделі і відведення свердла убік. Щоб запобігти зсуву осі, потрібно правильно розмічати деталь і заздалегідь засвердлювати центрове поглиблення, перевіряти міцність кріплення деталі до початку роботи, а також биття і правильність заточування свердла.
Перекіс осі отвору може бути викликаний неправильною установкою деталі на столі верстата або в пристосуванні, попаданням стружки під деталь, не перпендикулярністю столу до шпинделя верстата і надмірно великим натиском на свердло при його подачі. Щоб попередити цей вид браку, необхідно детально перевірити установку і кріплення деталі, попередньо очистивши стіл від стружки і бруду, вивірити стіл, слідкувати за силою натиску на свердло при ручній подачі.
Безпека праці
Безпека праці при розмітці.
При виконанні розміточних операцій необхідно дотримуватись наступних правил безпеки праці:
встановлення заготовок (деталей) на плиту і зняття з плити необхідно виконувати лише в рукавицях;
заготовки (деталі), пристосування надійно встановлювати не на краю плити, а ближче до середини;
перед встановленням заготовок (деталей) на плиту слід перевірити її на стійкість;
під час роботи на вільні (не використовувані) гостро заточені кінці чертилок обов’язково надівати запобіжні пробки або спеціальні ковпачки;
мідний купорос, що використовується для фарбування, наносять лише кісточкою, дотримуючись мір безпеки (він ядовитий);
слідкувати за тим, щоб проходи навколо розміточної плити були завжди вільні;
слідкувати за справністю кріплення молотка на ручці;
видаляти пил і окалину з розміточної плити лише щіткою, а з крупних плит – мітлою;
промаслене дрантя і папір складають лише в спеціальні металеві ящики.
Безпека праці при свердлінні.
При роботі на свердлильному верстаті слід дотримуватись наступних правил безпеки праці:
правильно встановлювати, надійно закріплювати заготовки на столі верстата і не утримувати їх руками в процесі обробки;
не залишати ключа в свердлильному патроні після зміни ріжучого інструменту;
пуск верстата виконувати лише тоді, коли є тверда впевненість в безпеці роботи:
стежити за роботою насоса і кількістю охолоджуючої рідини, що поступає до місць обробки;
не братися за ріжучий інструмент, що обертається, і
шпиндель;
не виймати рукою зламаних ріжучих інструментів з отвору, користуватися для цього спеціальними пристосуваннями;
не натискувати сильно на важіль подачі при свердлінні заготовок на прохід, особливо при свердлінні свердлами малого діаметра;
підкладати дерев’яну підкладку на стіл верстата під
шпиндель при зміні патрона або свердла;
користуватися спеціальним ключем, клином для видалення свердлильного патрона, свердла або перехідної втулки з
шпинделя;
постійно стежити за справністю ріжучого інструменту і пристроїв кріплення заготовок і інструменту;
не передавати і не приймати яких-небудь предметів через працюючий верстат; не працювати на верстаті в рукавицях; не спиратися на верстат під час його роботи.
Обов’язково зупиняти верстат у випадку:
відходу від верстата навіть на короткий час;
припинення роботи;
виявлення несправностей у верстаті, приладді, пристосуваннях і ріжучому інструменті;
змащування верстата;
установки або зміни ріжучого інструменту і пристосувань, приналежностей і т. д.;
прибирання верстата, робочого місця і стружки з інструменту, патрона і заготовки
Важливим моментом перед свердлінням підготувати поверхню. торець заготовки має бути підрізаний, тобто перпендикулярний до осі.
Для запобігання зміщенню свердла на початку свердління торець заготовки засвердлюють коротким свердлом , діаметр якого перевищує розміри отворів, що мають просвердлюватися.
Рис. Засвердлювання торця заготовки
Заготовка на верстаті має бути надійно закріплена, без биття. Співвісність верстату необхідно перевіряти раніше щоб запобігти уводу свердла. Свердло встановлюють в пінолі задньої бабки в свердлильному патроні або перехідній втулці з мінімальним вильотом. Включають обертання шпинделя і плавно підводять свердло ручною подачею. При виході сверла з крізного отвору подачу необхідно зменшити, щоб уникнути викришування ріжучих кромок.Обертання шпинделя виключити після того, як свердло вивели з отвору. Для підвищення стійкоті різця використовують охолоджуючу рідину.Охолоджувальна рідина під час свердління на токарному верстаті має подаватися безпосередньо в отвір, що обробляється.
Задану довжину свердління (глибину отвору) контролюють під час роботи за поділками на пінолі або за крейдяною міткою на свердлі, за допомогою обмежувальної втулки ( а), чи індикаторного пристрою, що закріплюється на пінолі (б). Індикатор настроюють за еталонною деталлю; він забезпечує точність контролю глибини отвору до 0,01 мм.

Рис. Контроль глибини під час свердління: а – за допомогою обмежувальної втулки; б – за Свердління є одним з найпоширеніших методів одержання отвору різанням. Різальним інструментом тут є свердло, яке дає можливість як одержувати отвір у суцільному матеріалі (свердління), так і збільшувати діаметр уже просвердленого отвору (розсвердлювання).

Під час свердління оброблювану деталь закріплюють на столі свердлильного верстаті прихватами, у лещатах, на призмах і т. п., а зверху надають двох сумісних рухів (рис. 152) — обертального за стрілкою і поступального (направлений вздовж осі свердла) за стрілкою 5. Обертальний рух свердла називається головним (робочим) рухом. Поступальний рух вздовж осі свердла називається рухом подачі.
Свердла для глибокого свердління застосовуються на спеціальних верстатах для одержання точних отворів Рис. 152. Робота свердла малого діаметра. Під глибоким свердлінням звичайно розуміють свердління отворів, довжина яких перевищує їх діаметр у 5 раз і більше. Центрові свердла (рис. 153, г) застосовуються для одержання центрових заглиблень на оброблюваних деталях.
Свердління застосовується під час виконання багатьох слюсарних робіт. Воно виконується на приводних свердлильних верстатах і вручну — ручними дрилями, з допомогою механізованого інструменту — електричними і пневматичними дрилями, а також електроіскровим і ультразвуковим методами.
Свердла, їх конструкції і призначення. Зд конструкцією і призначенням свердла поділяються на ряд видів.
Перові свердла являють собою простий різальний інструмент (рис. 153, а). Вони застосовуються головним чином у тріскачках і ручних дрилях для свердління невідповідальних отворів діаметром до 25 мм.
Спіральні свердла з циліндричними і конічними хвостовиками (рис. 153,6, в) використовуються як для ручного свердління, так і для роботи на верстатах (свердлильних, револьверних і ін.).
Свердла для глибокого свердління застосовуються на спеціальних верстатах для одержання точних отворів малого діаметра. Під глибоким свердлінням звичайно розуміють свердління отворів, довжина яких перевищує їх діаметр у 5 раз і більше.
Центрові свердла (рис. 153, г) застосовуються для одержання центрових заглиблень на оброблюваних деталях.
Комбіновані свердла дають можливість провадити одночасну обробку одноосьових отворів (рис. 153,5), а також одночасне свердління і зенкування або розвірчування отворів (див., наприклад, рис. 153, е).

Для виготовлення свердел, як правило, застосовують такі інструментальні матеріали: вуглецеву інструментальну сталь марок У10А і У12А, леговані сталі — хромисту марки X і хромокрем- нисту 9ХС; швидкорізальну сталь марок Р9 і Р18. В останні роки для цієї мети застосовують також металокерамічні тверді сплави марок ВК6, ВК8 і Т15К6.
Свердла з швидкорізальних сталей виготовляють зварними: робочу частину — з швидкорізальної сталі, а решту — з менш дорогої конструкційної сталі. Найпоширенішими є спіральні свердла з швидкорізальних сталей.
Елементи і геометричні параметри спірального свердла. Спіральне свердло має робочу частину, шийку, хвостовик для кріплення свердла в шпинделі верстата і лапку, що є упором під час вибивання свердла з гнізда шпинделя (рис. 154, а). Робоча частина, в свою чергу, поділяється на різальну і напрямну.
Різальна частина, на якій розміщені всі різальні елементи свердла, складається: з двох зуб'їв (пер), утворених двома спіральними канавками для відведення стружки (рис. 154,6); перемички (серцевини) — середньої частини свердла, що з'єднує обидва зуби (пера); двох передніх поверхонь, по яких збігає стружка, і двох задніх поверхонь; двох стрічечок, призначених для направлення свердла, калібрування отвору і зменшення тертя свердла об стінки отвору; двох головних різальних кромок, утворених перетином передніх і задніх поверхонь і виконуючих основну роботу різання; поперечної кромки (перемички), утвореної перетином обох задніх поверхонь. На зовнішній поверхні свердла між краєм стрічечки і канавкою розташована трохи заглиблена частина, що йде по гвинтовій лінії, яка називається спинкою зуба.
Зменшення тертя свердла об стінки просвердлюваного отвору досягається також тим, що робоча частина свердла має зворотний конус, тобто діаметр свердла біля різальної частини більший, ніж на другому кінці, біля хвостовика. Різниця між величиною цих діаметрів становить 0,03—0,12 мм на кожні 100 мм довжини свердла.
У свердел, оснащених пластинками твердих сплавів, зворотна конусність приймається від 0,1 до 0,3 мм на кожні 100 мм довжини.
До геометричних параметрів різальної частини свердла (рис. 155) відносяться: кут при вершині свердла, кут нахилу гвинтової канавки, передній і задній кути, кут нахилу поперечної кромки (перемички).
Кут при вершині свердла 2ср розміщений між головними різальними кромками. Він дуже впливає на роботу свердла. Величина цього кута вибирається залежно від твердості оброблюваного матеріалу і коливається в межах від 80 до 140°;
для сталей, чавунів і твердих бронз 2ср = 116-И18°; для латуней і м'яких бронз 2ф = 130°; для легких сплавів — дуралюміну, силуміну, електрону і бабіту 2ф = 140°; для червоної міді 2ф = 125°; для ебоніту і целулоїду 2ф = 80-т-90°.
Для підвищення стійкості свердел діаметром 12 мм і більше застосовують подвійну заточку свердел; при цьому головні різальні кромки мають форму не прямої, як при звичайному заточуванні (рис. 155, а), а ламаної лінії (рис. 155,6). Основний кут 2ф = 116-і- -т-1180 (для сталей і чавунів), а другий кут 2ф0= 70-г-75°.
свердло (особливо малого діаметра) із збільшенням кута нахилу гвинтової канавки ослаблюється. Тому у свердел малого діаметра цей кут роблять меншим, ніж у свердел великого діаметра.
Кут нахилу гвинтової канавки повинен вибиратися залежно від властивостей об- j$ роблюваного металу.
Кут нахилу гвинтової канавки позначається буквою омега о> (рис. 155, а). Із збільшенням цього кута процес різання полегшується, поліпшується вихід стружки. Але для міді і алюмінію цей кут треба брати в межах 35—40°, а для обробки сталі ш = 25° і менше.
Якщо розсікти спіральне свердло площиною, перпендикулярною до головної різальної кромки, то ми побачимо передній кут (див. переріз Б—Б на рис. 155, в).
Передній кут ^ (гамма) у різних точках різальної кромки має різну величину: він більший біля периферії свердла і помітно менший біля його осі. Так, якщо біля зовнішнього діаметра передній кут y = 25-КЗО®, то біля перемички він близький до 0°. Непостійність величини переднього кута відноситься до недоліків спірального свердла і є однією з причин нерівномірного і швидкого його спрацювання.
Задній кут свердла а (альфа) передбачений для зменшення тертя задньої поверхні об поверхню різання. Цей кут розглядається в площині А—А, паралельній осі свердла (рис. 155, в). Величина заднього кута також змінюється в напрямі від периферії до центра свердла; біля периферії він дорівнює 8—12°, а біля осі а = 2(Н-26°.
Кут нахилу поперечної кромки ф (псі) для свердел діаметром від 1 до 12 мм коливається від 47 до 50° (рис. 155, в), а для свердел діаметром понад 12 мм ф =55°.
Свердла, оснащені пластинками твердих сплавів, порівняно з свердлами, виготовленими з сталей, мають меншу довжину робочої частини, більший діаметр серцевини і менший кут нахилу гвинтової канавки. Ці свердла мають високу стійкість і забезпечують більш високу продуктивність. Особливо ефективне застосування свердел з пластинками твердих сплавів під час свердління і розсвердлювання чавуну, твердої сталі, пластмас, скла, мармуру та інших твердих матеріалів.
Свердла, оснащені пластинками твердих сплавів, випускаються чотирьох типів: спіральні з циліндричним хвостовиком (рис. 156, а); спіральні з конічним хвостовиком (рис. 156,6); з прямими канавками і конічним хвостовиком (рис. 156, б) і з косими канавками і циліндричним хвостовиком (рис. 156,2).
Процес різання під час свердління. У процесі свердління під діянням сили різання різальні поверхні свердла стискують частинки металу, що до них прилягають, і коли тиск, створюваний свердлом, перевищить сили зчеплення частинок металу, починають утворюватись елементи стружки, і вона відділяється.
Під час свердління в'язких металів (сталь, мідь, алюміній і ін.) окремі елементи стружки, щільно зчіплюючись між собою, утворюють безперервну стружку, що завивається в спіраль (див. рис. 152). Така стружка називається зливною. Якщо оброблюваний метал крихкий, наприклад чавун або бронза, то окремі елементи стружки надламуються і відокремлюються один від одного. Така стружка, що складається з окремих роз'єднаних між собою елементів (лусочок) неправильної форми, носить назву стружки надлому.
У процесі свердління розрізняють такі елементи різання: швидкість різання, глибина різання, подача, товщина і ширина стружки (рис. 157).
Головний робочий рух свердла (обертальний) характеризується швидкістю різання.
Швидкість різання — це шлях, що проходить у напрямі головного руху найбільш віддалена від осі інструмента точка різальної кромки за одиницю часу. Прийнято швидкість різання позначати латинською буквою V і вимірювати в метрах за хвилину.
Якщо відомі число обертів свердла і його діаметр, не важко визначити швидкість різання. Вона підраховується за загальновідомою формулою
г) ~ Тооо м^хв>
де й — діаметр інструмента (свердла), мм\ п — число обертів свердла за хвилину; я — постійне число, що приблизно дорівнює 3,14.
Якщо відомі діаметр свердла і швидкість різання, то число обертів можна обчислити за формулою
1000
п = обіхв.
Подачею при свердлінні називається переміщення свердла вздовж осі за один оберт. Вона позначається буквою 5 і вимірюється в мм/об. Свердло має дві головні різальні кромки. Отже, подача на одну різальну кромку буде виражена так:
Для характеристики величини переміщення свердла за хвилину іноді визначають подачу за хвилину
Ручна пневматична дриль ИП-1027 призначена для свердління отворів діаметром до 10 мм у сталях середньої міцності з тимчасовим опором σв≤ 400 МПа (40 кгс/мм2), а також у кольорових металах, пластмасах і дереві при температурі навколишнього середовища до +40С. Загальний вид дрилі ИП-1027 наведений на (рис. 6.9).
Пневматична дриль ИП-1027 складається з наступних основних вузлів і деталей: шпинделя 1, на виступаючому кінці якого кріпиться свердлильний патрон, корпусу2, планетарного редуктора3, ротаційного пневмодвигуна5, відцентрового регулятора6, рукоятки7з убудованими в неї механізмом8зміни частоти обертання й пусковим пристроєм9.
При натисканні на курок пускового пристрою стиснене повітря надходить у робочу порожнину двигуна й обертає ротор. Обертання ротора через планетарний редуктор і шпиндель передається свердлу. Регулювання частоти обертання здійснюється поворотом перемикача.
Технічна характеристика пневматичної дрилі ИП-1027: максимальний діаметр свердла – 10мм; частота обертання шпинделя на холостому ходу без регулювання – 46,6 с–1(2800 хв–1), з регулюванням – 23,3 с–1(1400 хв–1); номінальна потужність на шпинделі (без регулювання) – 0,38 кВт; питома витрата повітря – 1,8 м3·хв–1 кВт–1; габаритні розміри, мм: довжина– 180, ширина – 53, висота – 178; маса (без патрона) – 1,1 кг.

Рис. 6.9. Схема пневматичної дрилі ИП-1027:
1 – шпиндель; 2 – корпус; 3 – планетарний редуктор; 4 – стопорний гвинт;
5 – ротаційний пневмодвигун; 6 – відцентровий регулятор; 7 – рукоятка; 8 – механізм зміни частоти обертання; 9 – пусковий пристрій
Система підведення стисненого повітря (рис. 6.10) складається із трубопроводу, крана керування, фільтра-вологовіддільника, редукційного пневмоклапана, манометра, маслорозпилювача, рукава довжиною 3…5 м (внутрішній діаметр рукава 12,5 мм), приєднувального пристрою.

Рис. 6.10. Схема підведення стисненого повітря до дрилі:
1 – трубопровід; 2 – кран керування; 3 – фільтр-вологовіддільник;
4 – редукційний пневмоклапан; 5 – манометр; 6 – маслорозпилювач;
7 – рукав; 8 – приєднувальний пристрій
Дрилі з пневматичним приводом найчастіше застосовуються під час ремонту кузовів. Їхні переваги над електричними – менша маса (0,5...2,5 кг), ергономічність форми, менша вартість експлуатації.
6.7. Пневматичні ножиці для листового металу
Пневматичні ручні ножиціпризначені для розрізу листового металу завтовшки до 2,5мм. Вони мають невеликі розміри, зручні та безпечні в експлуатації.
Пневматичні ручні ножиці моделі П-5401 (рис. 6.11) складаються з металевого корпусу 7, гумової сорочки6,ротаційного двигуна8,плунжера9,планетарного редуктора5з ексцентриковим водилом, повзуна4з верхнім рухомим ножем3,завитка7із нерухомим ножем2. При натисканні на кнопку пускового пристрою стиснене повітря (тиск 0,5 МПа) надходить у робочу порожнину ротаційного двигуна8.
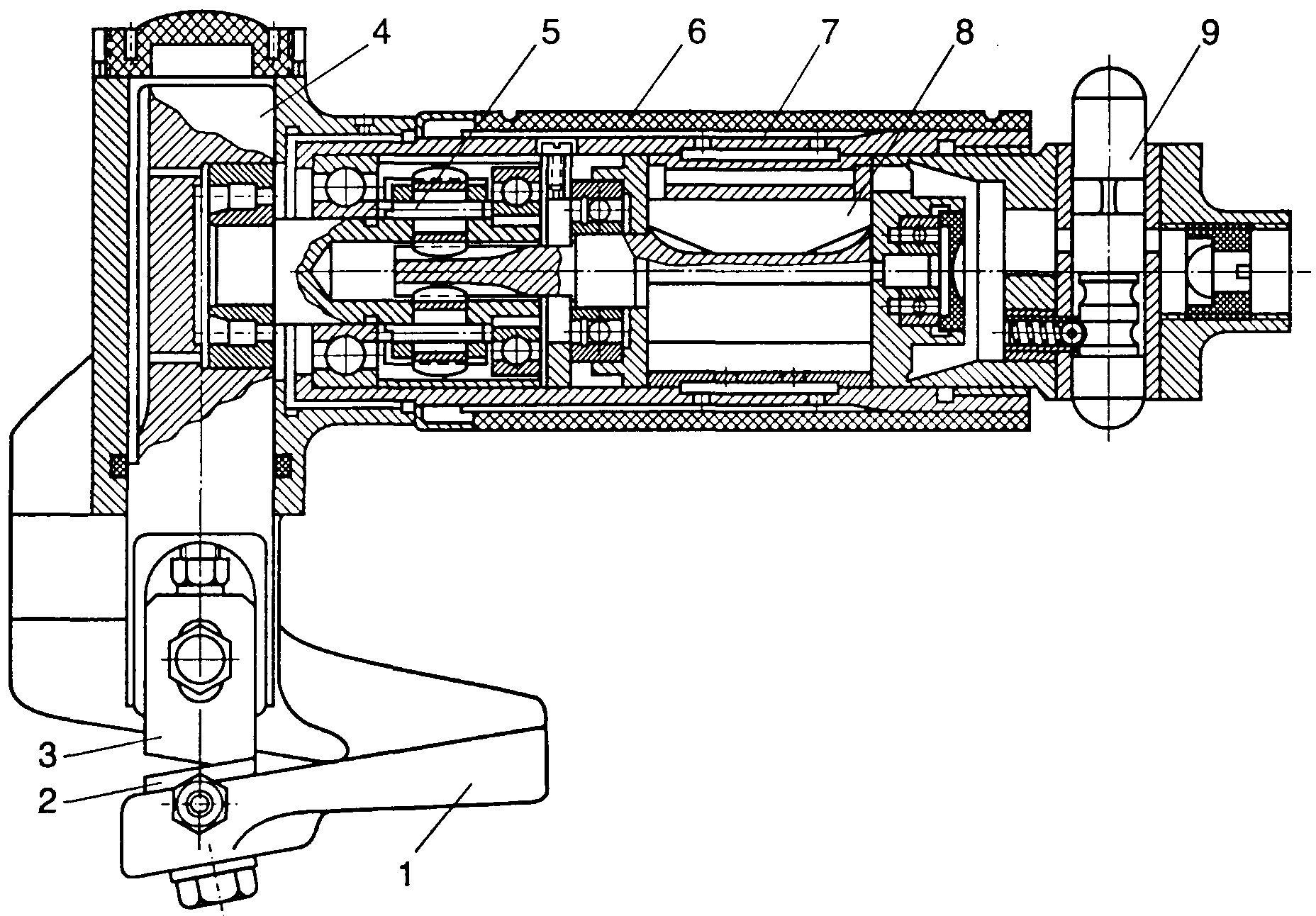
Рис. 6.11. Пневматичні ручні ножиці:
1 – завиток; 2 – нерухомий ніж; 3 – рухомий ніж; 4 – повзун; 5 – планетарний редуктор; 6 – сорочка; 7 – корпус; 8 – двигун; 9 – плунжер
Обертальний рух ротора двигуна через планетарний редуктор 5передається ексцентриковому водилу, з’єднаному з повзуном4, на якому закріплено верхній рухомий ніж3. Унаслідок цього повзун із ножем дістає зворотно-поступальний рух із кількістю подвійних ходів 2500 ± 250.
Під час різання листового металу ножиці тримають за корпус правою рукою, а лівою відгинають лист, що розрізується.

Урок №13
Тема: Обпилювання металiв.
1. Застосування обпилювання.
2. Напилки, їх пpофiлi та
pозмipи.
3. Види насiчок напилкiв.
4. Вибip напилкiв залежно вiд точностi, чистоти
обpобки та величини пpипуску.
5. Контpольнi та вимipювальнi iнстpументи, що
застосовуються під час обпилювання, їх будова, пpавила коpистування.
6. Розпилювання отвоpiв.
7. Застосування шаблонiв i вкладишiв.
8. Бpак пiд час
обпилювання i заходи запобiгання.
9. Безпека праці пiд час обпилювання металiв.
Конспект:
Призначення і застосування обпилювання. Призначення напилків, номери насічок. Закріплення деталі. Допуск металу на обпилювання. Обпилювання зовнішніх плоских та криволінійних поверхонь. Обпилювання за копіром (кондуктором). Припасування. Види браку при обпилюванні, причини і заходи його попередження.Зачищення металу. Механізація процесів обпилювання і зачищенняТонке, точне, чистове і грубе шабрення. Підвищення продуктивності шабрення з одночасним його притиранням. Шабери ручні і механічні. Механізація процесу шабрення. Два способи притирання. Механізовані машини при виконанні притирочних робіт. Остаточна обробка поверхонь притирковими пастами. Перевірка якості поверхонь, що притираються.Обробка поверхонь методом полірування. Шліфувально-полірувальні верстати.
Обпилювання металу
Обпилювання – операція, при виконанні якої з поверхні заготовки знімається шар металу (припуск) за допомогою ріжучого інструменту – напилка. Мета обпилювання – надання деталям необхідної форми, розмірів і заданої шорсткості поверхні.
У практиці слюсарної обробки частіше за інших застосовуються наступні основні види обпилювальних робіт: обпилювання зовнішніх плоских і криволінійних поверхонь; обпилювання зовнішніх н внутрішніх кутів, а також складних або фасонних поверхонь; обпилювання поглиблень, отворів, пазів і виступів. Обпилювання виконується різними напилками і поділяється на попереднє (чорнове) і остаточне (чистове і оздоблювальне).
Обробка напилком дає можливість отримати точність деталей до 0,05 мм, а в окремих випадках навіть до 0,01 мм.
Припуски при обпилюванні зазвичай невеликі – від 0,5 до 0,025 мм.
Напилки, їх конструкція і класифікація
Напилком називають ріжучий інструмент у вигляді сталевого загартованого бруска певного профілю з великою кількістю насічок або нарізок, утворюючих дрібні і гострі зуби. Цими зубами напилок зрізує невеликий шар металу у вигляді стружки.
Матеріалом для виготовлення напилків служить вуглецева інструментальна сталь марки У13 і У13А, а також хромиста шарикопідшипникова сталь ШХ15.
Напилки мають різну форму поперечного перетину: плоску, квадратну, тригранну, круглу і ін. Залежно від характеру виконуваної роботи застосовують напилки різної довжини, а також з різним числом насічок, що приходяться на 1 пог. см робочої частини (драчові, личкувальні і оксамитові).
Мал. 6.1. Звичайні напилки
Є три типи ручних напилків: звичайні, надфілі і рашпілі. Звичайні напилки (мал. 6.1) роблять з вуглецевої інструментальної сталі марок У13 і У13А. Надфілі (див. мал. 6.2) – це ті ж напилки, але менших розмірів і з насічкою лише на половину або три чверті своєї довжини. Гладка частина надфіля служить рукояткою. Надфілі виготовляються із сталі У12 і У12Д, вони застосовуються для обробки малих поверхонь і доведення деталей невеликих розмірів.Мал. 6.2. Надфілі
Рашпілі (див. мал. 6.3, в) відрізняються від напилків і надфілів конструкцією насічки. Вони застосовуються для грубої обробки м’яких металів – цинку, свинцю і т. і., а також для обпилювання дерева, кісті, рогу.Мал. 6.3. Насічки напилків
Конструкція напилків. Конструкція напилка залежить від вигляду насічки, геометрії зубів, профілю і інших чинників. Зуби напилка можуть бути утворені
карбуванням,
фрезеруванням, нарізанням,
протяганням і
точінням методом обкатування. Найбільш поширеним способом утворення зубів є карбування їх на спеціальних верстатах.
Насічки на поверхні напилка утворюють зуби. Чим менше насічок на 10 мм довжини напилка, тим більше зуб. По вигляду або формі насічок напилки бувають з одинарною (однорядною) і подвійною (перехресною), а також рашпільною насічками.
Напилки з одинарною насічкою зрізують метал широкою стружкою, рівною всій довжині зуба, тому робота ними вимагає великих зусиль. Такі напилки застосовуються для обробки кольорових металів, целулоїду, дерева і ін. Одинарна насічка наноситься під кутом 25-300 по відношенню до лінії, перпендикулярної до осі напилка (мал. 6.3, а)
У напилках з подвійною насічкою (мал. 6.3, б) спочатку карбують нижню глибоку насічку, яка називається основною, а поверх неї – верхню неглибоку насічку, яка називається допоміжною; вона розрубує основну на велике число окремих зубів. Допоміжна насічка має напрям справа наліво вгору, а основна, що утворює профіль зуба, – зліва направо вгору, якщо дивитися на насічку напилка від хвостовика до носка. Перехресна насічка подрібнює стружку, що полегшує роботу. В напилків з подвійною (перехресною) насічкою основна насічка зазвичай виконується під кутом нахилу 250, а допоміжна – під кутом нахилу 450.
Крок (відстань) між двома сусідніми зубами на основній насічці більше, ніж на допоміжній. В результаті зуби розміщуються один за одним по прямій, що складає кут 50 з віссю напилка (мал. 6.3, г), і при його русі сліди зубів частково перекривають один одного. Тому на обробленій поверхні зменшується шорсткість, і вона виходить відносно чистою і гладкою.
Зуби рашпільної насічки (мал. 6.3, в) утворюються витискуванням металу заготовки рашпіля насічними зубилами із спеціальною формою заточування. Кожен зуб рашпільної насічки зміщений відносно розташованого попереду зуба на половину кроку. Це зменшує глибину канавок, що утворюються на поверхні обпилюваної заготовки, і полегшує процес різання. Напилки з таким виглядом насічки застосовуються для обпилювання м’яких матеріалів (дерево, каучук, гума, кість, ріг і ін.), оскільки в цьому випадку знімається велика стружка, що вимагає і крупних зубів. В напилках із звичайною насічкою стружка таких матеріалів забиває зуби, і вони не можуть різати.
Класифікація напилків. Напилки розрізняються по числу насічок (величині зубів), профілю перетину, довжині, призначенню.
По кількості зубів, насічених на 10 мм довжини, напилки діляться на 6 класів (таблиця 5.1).
Таблиця 5.1
Номера насічки | Кількість основних насічок на 10 мм довжини напилка при довжині напилка в мм |
100 | 125 | 150 | 200 | 250 | 300 | 350 | 400 |
0 | – | – | – | – | – | – | 4,5 | 4,5 |
1 | 14 | 14 | 12 | 10 | 8,5 | 7 | 6 | 6 |
2 | 20 | 20 | 17 | 14 | 12 | 10 | 8,5 | 8,5 |
3 | 28 | 28 | 24 | 20 | 17 | 14 | 12 | 12 |
4 | 40 | 40 | 34 | 28 | 24 | 20 | – | – |
5 | 56 | 56 | 48 | 40 | 34 | 28 | – | – |
Залежно від виконуваної роботи (призначення) напилки поділяються на наступні види: слюсарні – загального призначення і для спеціальних робіт, машинні, надфілі і рашпілі.
Слюсарні напилки загального призначення виготовляються восьми типів: плоскі (тупоносі і гостроносі), квадратні, тригранні, напівкруглі, круглі, ромбічні і ножівкові завдовжки від 100 до 400 мм з насічкою № 0-5. Напилки мають подвійну (перехресну) насічку, утворену способом карбування.
Слюсарні напилки для спеціальних робіт призначаються для видалення досить великих припусків при обпилюванні пазів, фасонних і криволінійних поверхонь; для обробки кольорових металів, неметалічних матеріалів і т. п. Залежно від виконуваних робіт напилки цього виду діляться на пазові, плоскі з овальними ребрами, брусовки, двокінцеві і ін.
Мал. 6.4. Напилки машинні: а – стрижньові, б – дискові і пристосування, в якому закріплюється напилок при роботі, в – фасонні головки
Машинні напилки (мал. 6.4) по своїй конструкції поділяються на стержневі, дискові, фасонні голівки і пластинчасті. В процесі роботи стержневим напилкам надається зворотно-поступальний рух, дисковим напилкам і фасонним голівкам – обертальний, а пластинчастим – безперервний рух разом з безперервно рухомою металевою стрічкою.
Надфілі (дрібні напилки) виготовляються 10 типів: плоскі – тупоносі і гостроносі, трьохгранні – однобічні, квадратні, напівкруглі, круглі, овальні, ромбічні, завдовжки 40, 60 і 80 мм з насічкою 5 номерів (мал. 126). Довжина надфіля визначається довжиною робочої частини. Ребра плоских надфілів мають одинарну або подвійну насічку. Бічні сторони і верхнє ребро ножівкових надфілів мають подвійну насічку.Машинні напилки застосовують для обробки фасонних поглиблень і отворів, криволінійних поверхонь, для видалення
облоя і зняття задирок.
Надфілі застосовуються для обпилювання невеликих поверхонь і вузьких місць, недоступних для обробки слюсарними напилками.
Рашпілі виготовляють чотирьох типів: загального призначення, шевські (з рос. сапожные) і копитні. Залежно від профілю рашпілі загального призначення поділяються на плоскі (тупоносі і гостроносі), круглі і напівкруглі з насічкою № 1-2 і завдовжки від 250 до 350 мм.
Окрім вказаних, при слюсарній обробці застосовуються напилки, які кріпляться в спеціальних пристосуваннях.
Вибір напилків. Використання напилків того або іншого класу залежить від характеру виконуваної роботи (це було зазначено вище), припуску на обпилювання, а також від необхідної точності і шорсткості поверхні.
Вибір напилка з тією чи іншою кількістю насічок залежить від припуску на обпилювання, а також від необхідної точності і шорсткості поверхні:
Для грубого обпилювання, коли потрібно зняти великий шар металу (до 1,0 мм), використовуються брусовки – напилки квадратного перетину, що мають дуже крупну насічку: 4,5-7 насічок на 10 мм довжини.
Для грубого обпилювання заготовок, коли необхідно зняти припуск до 0,5 мм, застосовуються драчові напилки, що дозволяють за один хід зняти шар 0,08-0,15 мм.
Личкувальні напилки використовуються для чистішої обробки поверхні (після попередньої обробки драчовим напилком), коли потрібно зняти припуск не більше 0,15 мм. Личкувальні напилки дозволяють за один хід зняти шар металу завтовшки 0,05-0,08 мм; при цьому досягається шорсткість поверхні, відповідна 7-8-у класам чистоти.
Напилки з оксамитовою насічкою застосовуються для найточнішої обробки, підгонки, доведення деталей і шліфування поверхонь з точністю 0,01-0,05 мм; за один хід знімається шар металу 0,01-0,03 мм. Шорсткість поверхні при цьому відповідає 9-12-у класам чистоти.
Надфілі призначені для дуже точної і дрібної роботи головним чином в інструментальних цехах. Ними випилюють фасонні отвори і пази в шаблонах, доводять деталі, що сполучаються, і т. п.
Як зазначалося вище, також окремий вид насічки мають рашпілі.
Вибір напилка того чи іншого профілю залежить від форм обпилюваних поверхонь:
Плоскі напилки застосовуються для обпилювання вільних зовнішніх і внутрішніх площин, опуклих поверхонь, а також поверхонь, зв’язаних під кутом 90° (мал. 6.5, а, б і ж).
Квадратні напилки застосовують для розпилювання квадратних і прямокутних отворів, прямокутних пазів, недоступних для роботи плоским напилком. Личкувальні квадратні напилки часто використовують для зачистки зовнішніх і внутрішніх кутів (мал. 6.5, в).
Трьохгранні напилки служать для обпилювання відкритих і закритих кутів більше 600, багатогранних отворів і площин в недоступних для плоских напилків місцях (мал. 6.5, г).
Напівкруглі напилки застосовують для обпилювання опуклою стороною криволінійних (увігнутих) поверхонь з великим радіусом. Плоскою стороною напівкруглого напилка можна обпилювати прямолінійні поверхні і кути менше 600 (мал. 6.5, д і е).
Мал. 6.5. Прийоми використання напилків різноманітного профілю
Круглі напилки служать для розпилювання круглих або овальних отворів, а також увігнутих поверхонь недоступних для напівкруглого напилка (мал. 6.5, з).
Ножівкові напилки застосовують для обпилювання внутрішніх кутів більше 100, клиновидних канавок, вузьких пазів, площин в трьохгранних, квадратних і прямокутних отворах (мал. 6.5, и).
Машинні напилки, наприклад фасонні головки, використовуються в процесі виготовлення моделей і штампів переважно для обпилювання фасонних порожнин, отворів і ін. (мал. 6.5, к).
Мал. 6.6. Прийоми насаджування і знімання рукоятки напилка
Рукоятки до напилків. Для зручності і безпеки обпилювання на хвостовик напилка насаджують дерев’яну рукоятку з берези, липи або пресованої паперової маси. Довжина рукоятки вибирається залежно від розміру напилка. Звичайно рукоятка в півтора рази довше за хвостовик напилка. Поверхня рукоятки має бути чистою і рівною.
Щоб рукоятка не розкололася під час насадки на хвостовик напилка, на її шийку надівають металеве кільце. Отвір в рукоятці під хвостовик напилка просвердлюють, а потім пропалюють хвостовиком старого напилка. При насадженні хвостовик вставляють в отвір рукоятки і вертикальними помахами ударяють головкою рукоятки об верстак або лещата (мал. 6.6, а). У ряді випадків насадження рукоятки на хвостовик напилка виконується так, як показано на мал. 6.6, б. Щоб зняти рукоятку з напилка, наносять два – три короткі слабкі удари молотком по верхньому краю шийки (мал. 6.6, в).
Вимоги до якості напилків. Низька якість напилка ускладнює процес обробки деталей. Основні вимоги до напилків зводяться до наступного. Вони не повинні мати видимих на око викривлень. Насічка має бути гострою, однорідною по кроку і глибині, правильною і чистою. Поверхня напилків має бути без тріщин, плівок, чорновин, ржавих плям, вм’ятин. Напилки не повинні ламатися при падінні на дерев’яну підлогу з висоти 1 м. При ударі об ковадло напилок повинен давати чистий звук. Хвостовик напилка має бути прямим. Вісь хвостовика повинна збігатися з віссю напилка.
Основні правила роботи напилком
Успішне виконання операції обпилювання залежить від правильного кріплення заготовки в лещатах, правильного положення (корпусу, ніг і рук) робітника і раціональних робочих рухів в процесі обпилювання.
Мал. 6.7. Положення працівника при обпилюванні: а – вид зверху, б – положення ніг
Деталь затискають в лещатах так, щоб оброблювана поверхня її виступала над губками лещат не більше ніж на 5-8 мм.
Положення робітника по відношенню до лещат залежить від характеру обпилювання. Найбільш зручним положенням слід вважати таке, при якому корпус робітника складає 450 з лінією, що проходить через губки лещат (мал. 6.7, а). Ліва нога слюсаря має бути висунута вперед носком у бік робочого руху напилка на відстань 150-200 мм від переднього краю верстака, а права – віддалена від лівої на відстань 200-300 мм так, щоб кут між середніми лініями ступень складав приблизно 60-70° (мал. 6.7, б). При знятті напилком товстих шарів металу, коли доводиться натискувати на напилок з великою силою, праву ногу відставляють від лівої на відстань 500-700 мм, оскільки в цьому випадку вона є основною опорою. При слабкому натиску на напилок, наприклад при доведенні або обробці поверхні деталі, ноги ставлять майже поруч.
Істотне значення мають прийоми «хватки» напилка. Його слід брати в праву руку так, щоб рукоятка упиралася в долоню руки, чотири пальці захоплювали рукоятку знизу, а великий палець поміщався зверху (мал. 6.8, а). Ліву руку накладають долонею впоперек напилка на відстані 20-30 мм від його носка. При цьому пальці повинні бути напівзігнуті; вони не підтримують, а лише притискують напилок (мал. 6.8, б і в). Лікоть лівої руки має бути злегка підведений. Права рука – від ліктя до кисті – повинна складати з напилком пряму лінію.
Мал. 6.8. Тримання («хватка») напилка: а – положення правої руки, б, в – положення лівої руки на напилку, г – положення лівої руки на напилку при доведенні
При доведенні, коли обпилювання ведеться з незначним зусиллям, можна натискувати на носок напилка не долонею, а лише великим пальцем лівої руки (мал.. 6.8, г).
Мал. 6.9. Прийоми руху напилка: а – правильні прийоми натиску на напилок, б – утворення завалу при обпилюванні
В процесі обпилювання натискувати на напилок слід лише при русі його вперед. На початку ходу напилка натиск лівою рукою має бути максимальним, а правою – мінімальним. При переміщенні напилка вперед натиск правою рукою необхідно збільшувати, а лівою – зменшувати (див. діаграму сил на мал. 6.9, а).
При натиску на напилок з постійною силою він на початку робочого ходу відхилятиметься рукояткою вниз, а в кінці – носком вниз. При цьому напилок буде «завалювати» краї обпилюваної поверхні. У ряді випадків «завали» можуть виходити і внаслідок інших причин, наприклад через надмірно глибокої установки заготовки при закріпленні її в лещатах, губки яких мають пологий підйом (мал. 6.9, б). В цьому випадку напилок відриватиметься від поверхні заготовки, що і призведе до утворення «завалу».
Переміщати напилок у зворотному напрямі потрібно вільно, без натиску, не відриваючи його від обпилюваної поверхні, оскільки при цьому втрачається опора, а з втратою опори пропадає упевненість в правильному положенні напилка при подальшому робочому русі. При обпилюванні площин напилок потрібно переміщати не лише вперед, але одночасно і вбік – вправо і вліво, щоб спилювати рівномірний шар металу зі всієї площини.
Якість обпилювання значною мірою залежить від уміння регулювати силу натиску на напилок, що досягається досвідом практичної роботи.
Частота рухів напилка залежить від навиків і фізичного тренування слюсаря. Найбільш раціональним вважається темп обпилювання 40-60 подвійних рухів напилка в хвилину.
Способи обпилювання. Напрям руху напилка, а отже, і положення штрихів (сліду напилка) на обробленій поверхні може бути поздовжнім, поперечним, перехресним і круговим.
Працюючи напилком лише в поздовжньому або лише в поперечному напрямі, важко отримати правильну і чисту поверхню заготовки.
Мал. 6.10. Напрямок руху напилка: а – поперечним штрихом, б – поздовжнім штрихом, в – перехресним штрихом, г – круговим штрихом
При поперечному обпилюванні напилок швидше знімає шар металу, ніж при поздовжньому, оскільки він стикається з меншою площею обпилюваної поверхні і легше врізається в метал. Отже, для зняття великих припусків краще застосовувати поперечне обпилювання (мал. 6.10, а). Процес обпилювання в даному випадку можна завершити наведенням поздовжнього штриха на оброблюваній поверхні (мал. 6.10, б). Поєднання поперечного і поздовжнього обпилювання грані дозволяє досягти потрібної міри її прямолінійності в поздовжньому напрямі.
Добрі результати по продуктивності і якості поверхні при обробці площин досягаються при обпилюванні перехресним (косим) штрихом; рух напилка переноситься при цьому поперемінно з кута на кут (мал. 6.10, в). Зазвичай спочатку обпилюють площину заготовки справа наліво під кутом 35-400 до бічної сторони лещат, а потім – також зліва направо. При обпилюванні перехресним штрихом на поверхні заготівки повинна весь час зберігатися сітка, що утворюється зубами напилка. По цій сітці контролюється якість роботи: відсутність сітки на якій-небудь ділянці поверхні вказує на неправильне положення напилка в цьому місці.
Круговими штрихами обпилювання виконують в тих випадках, коли з оброблюваної поверхні потрібно зняти виступаючі частини металу (мал. 6.10, г).
Чистове обпилювання і обробка поверхонь. При обпилюванні забезпечується не лише задана точність обробки, але і необхідна чистота обробки поверхні. Груба обробка досягається обробкою драчовим напилком, більш ретельна личкувальними напилками. Найбільш досконала обробка виходить при обробці оксамитовими напилками, паперовою або полотняною абразивною шкіркою, абразивними брусками і ін.
Мал. 6.11. Прийоми обробки обпиляних поверхонь: а – прийом обробки напилком, б – обробка поверхні дерев’яним бруском, в – обробка увігнутої поверхні абразивною шкіркою, г – прийоми очистки напилка скребками
При обробці площини оксамитовими напилками обпилювання виконується нанесенням поздовжніх і поперечних штрихів з легким натиском на напилок (мал. 6.11, а). Після обробки напилком поверхню в разі потреби обробляють абразивними брусками і шкірками, насухо або з маслом. У першому випадку отримують блискучу поверхню металу, в другому – напівматову. При обробці міді і алюмінію шкірку натирають
стеарином.
Для обробки поверхонь користуються також дерев’яними брусками з наклеєною на них абразивною шкіркою (мал. 6.11, б і в). У ряді випадків шкірку намотують на плоский напилок.
Очищення напилків від стружки виконується сталевими щітками, а також спеціальними скребками із сталевого або латунного дроту з розплющеним кінцем (мал. 6.11, г). При очищенні напилків від каучукової, фібрової і дерев’яної стружки їх заздалегідь опускають на 15-20 хв в гарячу воду, а потім прочищають сталевою щіткою. Замаслені напилки чистять шматком березового вугілля, яким натирають поверхні уздовж рядів насічок, а потім вже прочищають сталевою щіткою. Якщо таке очищення виявиться малоефективним, замаслений напилок слід промити в гарячому розчині
каустичної соди, очистити сталевою щіткою, промити у воді і висушити.
Способи виміру поверхні при обпилюванні. Контроль якості обпилювання виконується за допомогою перевірочних лінійок, плит, косинців і кронциркулів. Правильність обпилюваної площини контролюється перевірочною лінійкою на просвіт. Якщо лінійка лягає на площину щільно, без просвіту, це означає, що площина обпиляна чисто і правильно. Якщо вийшов рівномірний просвіт по всій довжині лінійки, означає площина обпиляна правильно, але грубо. Такий просвіт на поверхні виходить із-за штрихів, що залишаються зубами напилка, і лінійка щільно не прилягає.
Перевірка на просвіт виконується вздовж, впоперек і по діагоналі контрольованої площини. Не можна пересувати лінійку по поверхні, що перевіряється, оскільки вона швидко зношується і втрачає прямолінійність.
Якщо плоска поверхня повинна бути обпиляна особливо ретельно, її перевіряють за допомогою перевірочної плити «на фарбу». Для цього на поверхню перевірочної плити за допомогою ганчіркового тампона наносять тонкий рівномірний шар фарби (синьки або сажі, розведеної в маслі). Деталь, що потім перевіряється, обережно накладають на поверхню плити і легким зусиллям переміщають по всій її поверхні. Після зняття деталі з плити на виступаючих ділянках поверхні деталі залишається фарба. Саме ці виступаючі ділянки і підлягають додатковому обпилюванню. Перевірка виконується до тих пір, поки не буде отримана поверхня з рівномірними плямами фарби.
Мал. 6.12. Прийоми визначення паралельності площин: а – кронциркулем, б – штангенциркулем
У тих випадках, коли площина повинна бути обпиляна під певним кутом до іншої суміжної площини, контроль здійснюється за допомогою косинця.
Для перевірки паралельності двох площин користуються кронциркулем, нутроміром і штангенциркулем. Відстань між паралельними площинами в будь-якому місці має бути однаковою. Кронциркуль тримають правою рукою за шайбу шарнірного з’єднання (мал. 6.12, а). Для перевірки встановлюють розбіг ніжок кронциркуля точно по відстані між площинами в якому-небудь одному місці і переміщають кронциркуль по всій поверхні. Якщо ніжки кронциркуля ковзають по поверхнях рівномірно з легким тертям, то площини після обпилювання паралельні між собою.
При контролі паралельності сторін або вимірі відстані між сторонами за допомогою штангенциркуля, деталь, що перевіряється, беруть в ліву руку, а штангенциркуль – в праву; великим пальцем правої руки зрушують рухому рамку інструменту до щільного зіткнення з деталлю і за допомогою гвинта закріплюють її (мал. 6.12, б). Потім деталь повертають протилежним кінцем і обережно вводять у встановлений розбіг ніжок штангенциркуля. Наявність гойдання вказує на те, що одна сторона менше іншої.
Види обпилювання
У практиці слюсарної обробки найчастіше зустрічаються наступні види обпилювання: обпилювання плоских – зв’язаних, паралельних і перпендикулярних поверхонь деталей; обпилювання криволінійних поверхонь; обпилювання циліндричних і конічних деталей з підгонкою їх по місцю.
Обпилювання починається, як правило, з перевірки припуску на обробку, який міг би забезпечити виготовлення деталі по розмірах, вказаних на кресленні. Перевіривши розміри заготовки, визначають базу, тобто поверхню, від якої слід витримувати розміри деталей і взаємне розташування її поверхні.
Розмір напилка вибирають з таким розрахунком, щоб він був довше обпилюваної поверхні не менше ніж на 150 мм. Якщо клас чистоти поверхні на кресленні не вказаний, обпилювання виконують лише драчовим напилком. При необхідності отримати чистіші і гладкіші поверхні обпилювання закінчують личкувальним напилком.
Продуктивність праці при обпилюванні залежить від послідовності переходів, правильного користування напилком, а також від вживаних при обпилюванні пристосувань та оснастки для закріплення деталі і напряму напилка.
Обпилювання плоских поверхонь. Цей вид обпилювання – одна з найскладніших слюсарних операцій. Якщо слюсар навчиться правильно обпилювати прямолінійні поверхні, то він без зусиль обпиляє і будь-яку іншу поверхню. Для здобуття правильно обпиляної прямолінійної поверхні вся увага має бути зосереджена на забезпеченні прямолінійного руху напилка. Обпилювання потрібно вести перехресним штрихом (з кута на кут) під кутом 35-400 до бічних сторін лещат. При обпилюванні по діагоналі не слід виходити напилком на кути заготовки, оскільки при цьому зменшується площа опори напилка і він легко завалюється; потрібно частіше міняти напрям руху напилка.
Розглянемо послідовність переходів при обпилювані широких площин – сторін плоскопаралельної прямокутної плитки (мал. 6.13).
Мал. 6.13. Послідовність обпилювання плитки
Перед обпилюванням деталь затискають в лещатах так, щоб оброблювана поверхня була розташована горизонтально і виступала на 5-8 мм над губками лещат. Обробку починають з широкої площини 1 (мал. 6.13, а), що приймається за основну вимірювальну базу. Чорнове обпилювання ведуть плоским драчовим напилком, а чистове – плоским личкувальним напилком. Закінчивши обпилювання площини, деталь знімають. Перевірку правильності площини виконують лінійкою, накладаючи її вздовж, поперек і по діагоналі обробленої поверхні. Потім переходять до обпилювання таким же способом другої широкої площини 2. При цьому паралельність площин 1 і 2 контролюють кронциркулем. Встановивши на лещатах нагубники, обпилюють одну з вузьких площин (ребро 3) і перевіряють її лінійкою і косинцем від площини 1 (мал. 6.13, б). Потім виконується обпилювання ребер 4, 5 і 6 (мал. 6.13, а) з перевіркою їх від базової площини 1 першого ребра 4 (мал. 6.13, в).
Обпилювання вузьких площин на тонких деталях представляє значні труднощі. Дрібні і тонкі деталі (товщиною до 4 мм) важко рівномірно затиснути в лещатах, щоб отримати при обпилюванні рівну площину. В цілях підвищення продуктивності при цій роботі удаються до склепування 3-10 таких деталей в пакети. Прийоми обпилювання ребер в такому пакеті не відрізняються від обпилювання плитки з широкими ребрами.
Можна, проте, обійтися і без склепування тонких деталей, використовуючи при їх обпилюванні пристосування, що називаються намітками. До таких пристосувань відносяться: обпилювальні призми, розсувні рамки, намітки-рамки, плоскопаралельні намітки, копірні пристосування (кондуктори) і ін. Використання наміток полегшує точну установку і закріплення деталей, що дозволяє слюсареві працювати з більшою упевненістю, без побоювання зіпсувати оброблювану поверхню або не отримати потрібний розмір. Робочі частини пристосувань (наміток) точно оброблені, загартовані і відшліфовані.
Обпилювальна призма складається з корпусу 1 (мал. 6.14, а), на бічній поверхні якого жорстко закріплюються притиск 2, косинець 3 і лінійка 4. Косинець або лінійка використовуються для правильної установки оброблюваної деталі, а притиск – для її закріплення. Поверхня А корпусу призми служить направляючою для напилка. Шар металу заготовки, що підлягає зняттю, повинен виступати над площиною корпуса призми. Корпус обпилювальної призми закріплюють в слюсарних лещатах в горизонтальному положенні.
Мал. 6.14. Обпилювання вузьких граней за допомогою пристосувань: а – обпилювальна призма, б – обпилювання в наміткі-рамці
У практиці обпилювання тонких деталей застосовуються також намітки-рамки (мал. 6.14, б). Обпилювання в такому пристосуванні виключає «завали», оскільки деталь затискається не збоку пристосування, а в середині – в проймі. Розмічену заготовку вставляють в рамку, злегка притискуючи її гвинтом до внутрішньої стінки рамки. Уточнюють установку, добиваючись збігу риски на заготовці з внутрішнім ребром рамки, після чого остаточно закріплюють гвинти. Рамку затискають в лещатах і обпилюють вузьку поверхню заготівки до рівня робочої кромки рамки.
Розсувна рамка (обпилювальна намітка, або «паралелі») служить тим же цілям. Вона складається з двох подовжених брусків 1 прямокутного перетину (мал. 6.15, а), зв’язаних між собою двома направляючими планками 2. Один з брусків жорстко сполучений з направляючими планками, а інший може пересуватися уздовж цих планок паралельно першому бруску і притому так, що верхні грані обох брусків (поверхні А) залишаються в одній горизонтальній площині.
Розсувну рамку слід встановлювати в лещата так, щоб вона спиралася на губки лещат двома парами штифтів 3, які впресовані в зовнішні бічні грані брусків 1. Відстань між направляючими планками повинна бути більше, а між штифтами – менше ширини губок лещат.
Для обпилювання заготовок під прямим кутом користуються розсувним паралельним косинцем (мал. 6.15, б).
Мал. 6.15. Розсувні паралелі: а – рамка, б – паралельний косинець
Плоскопаралельна намітка представляє собою загартовану пластину з двома Г-образними виступами 1 і 2 (мал. 6.16). На такій намітці можна обпиляти чотири сторони (кромки) заготовки під кутом 900, не контролюючи правильності кутів в процесі роботи.
Мал. 6.16. Застосування плоскопаралельної намітки при обпилюванні
При установці намітка повинна лягти виступом 1 на нерухому губку. Потім розташовують оброблювану тонку заготовку 4 між рухомою губкою лещат і площиною 3 намітки, упираючи її ребро у виступ 2. Злегка затиснувши лещата, легким постукуванням по заготовці поєднують нанесену на ній розмічальну риску з верхньою кромкою намітки. Після цього остаточно затискають заготовку в лещатах і починають обпилювання під кутом 25-300до бічних сторін лещат (заготовки). Якщо робота виконується драчовим напилком, то, не доходячи 0,3 мм до верхньої поверхні намітки, його відкладають і продовжують обпилювання личкувальним напилком і працюють ним до тих пір, поки кромка заготовки не порівняється з верхньою поверхнею намітки.
Мал. 6.17. Обпилювання тонких заготовок і деталей: а – на дерев’яному бруску, б – на дерев’яному бруску з притиском, в – в металевих кутниках
Перевірка кромки, обпиляної цим способом, за допомогою лекальної лінійки покаже, що вона строго прямолінійна: між кромкою і лінійкою просвіту не буде. Для обпилювання другої кромки по розмічальній рисці заготовку переставляють в нове положення так, щоб оброблена кромка прилягла до виступу 2 намітки, а риска збіглася з верхньою поверхнею намітки. За допомогою плоскопаралельної намітки можна обпилювати прямолінійні ділянки заготовки, а також поверхні, розташовані під різними кутами.
Бічні сторони тонких заготовок обпилюють на затиснутому в лещатах бруску з твердого дерева (мал. 6.17, а). Дрібні деталі можна обпилювати за допомогою притисків (мал. 6.17, б). Заготовки, довжина яких перевищує довжину губок, при обробці затискають між двома металевими кутниками або дерев’яними брусками (мал. 6.17, в).
Обпилювання криволінійних поверхонь. Криволінійні поверхні деталей машин поділяються на опуклі і увігнуті. Звичайне обпилювання таких поверхонь пов’язано із зняттям значних припусків. Тому, перш ніж приступити до обпилювання, слід розмітити заготовку, а потім вибрати найбільш раціональний спосіб видалення зайвого металу: у одному випадку потрібно попереднє виконання ножівкою, в іншому – висвердлювання, в третьому – вирубка і т. д.
Надмірно великий припуск на обпилювання веде до збільшення часу на виконання завдання; малий припуск створює небезпеку псування деталі.

Мал. 6.18. Чистове обпилювання носка молотка личкувальним напилком
Опуклі поверхні обпилюють плоскими напилками вздовж і поперек опуклості. На мал. 6.18 показаний прийом обпилювання носка слюсарного молотка. При русі напилка вперед уздовж опуклості права рука повинна опускатися вниз, а носок напилка – підніматися вгору. Такі рухи забезпечують здобуття плавного заокруглення поверхні, без кутів, з оброблювальними штрихами, направленими уздовж кривизни поверхні.
При поперечному обпилюванні опуклої поверхні напилку надають окрім прямолінійного руху ще і обертальний.
Мал. 6.19. Обпилювання увігнутої поверхні круглим напилком
Увігнуті поверхні обпилюють круглими, напівкруглими і овальними напилками (мал. 6.19). При цьому також поєднуються два рухи напилка – прямолінійний і обертальний, тобто кожен рух напилка вперед супроводжується невеликим переміщенням його правою рукою на ¼ оберту вправо або вліво.
Значну частину металу при виконанні цієї роботи з цілого шматка часто видаляють вирізанням ножівкою. Потім плоским або квадратним напилком розпилюють грані, а напівкруглим або круглим напилком спилюють виступ, наближаючись до розмічальної риски (мал. 6.19).
Профіль перетину напівкруглого напилка необхідно підібрати з таким розрахунком, щоб його радіус був менший, ніж радіус поверхні, що розпилюється.
При обпилюванні опуклих або увігнутих поверхонь чорнове обпилювання слід вести драчовим напилком; не доходячи приблизно на 0,3-0,5 мм до розмічальної риски, драчовий напилок потрібно замінити личкувальним, після чого продовжити обпилювання або розпилювання поверхні до встановленого розміру. Перевірку правильності форми поверхні краще всього вести за шаблоном «на просвіт».
Перпендикулярність поверхні до торця заготовки перевіряють косинцем.
Найбільш продуктивним і точним способом обпилювання криволінійних поверхонь є обпилювання по копіру або кондуктору.
Мал. 6.20. Обробка деталі в обпилювальному кондукторі (копірі): 1 – копірна планка, 2 – заготовка
Копір-кондуктор в загальному випадку є пристосуванням, контур робочих поверхонь якого з точністю від 0,5 до 0,1 мм відповідає контуру оброблюваної на цьому пристосуванні деталі. Обпилювання в кондукторі виконується без попередньої розмітки. Робочі сторони пристосування повинні бути точно оброблені, загартовані і відшліфовані.
На мал. 6.20 показаний приклад обробки криволінійної поверхні тонкої деталі (пластини) в обпилювальному кондукторі. Заготовку, яка підлягає обпилюванню вставляють в кондуктор і разом з ним затискають в лещатах. Потім обпилюють частину заготовки, що виступає з кондуктора, до рівня робочих поверхонь кондуктора. При виготовленні великої кількості однакових деталей з тонкого листового матеріалу в кондукторі одночасно закріплюють декілька заготовок.
Припасування
Припасуванням називається точний взаємний пригін деталей, що з’єднуються без зазорів при будь-яких перекантовуваннях. Припасування відрізняється високою точністю обробки, що необхідно для беззазорного сполучення деталей (світлова щілина більше 0,002 мм є видимою).
Мал. 6.21. Припасування: а – розмітка, б – підгонка, в – підпилювання, г – перевірка вкладишем
Припасовують як замкнуті, так і напівзамкнуті контури. З двох припасованих деталей отвір прийнято називати проймою, а деталь, що входить в пройму, – вкладишем (мал. 6.21).
Припасування виконується напилками з дрібною і дуже дрібною насічкою – № 2, 3, 4 і 5, а також абразивними порошками і пастами.
Шліфування
Шліфування – один з видів обробки металів різанням. При цьому шар металу знімається шліфувальним кругом, який представляє собою пористе тіло, що складається з великої кількості дрібних зерен, які з’єднані між собою клеючою речовиною – зв’язкою.
Мал. 6.22. Процес шліфування: а – обробка периферією шліфувального круга, б – схема роботи абразивного зерна; 1 – зв’язка, 2 – пори, 3 – зерно, 4 – деталь, 5 – торець круга, 6 – периферія круга
Процес шліфування полягає в тому, що шліфувальний круг, який обертається, стикаючись з металом гострими гранями абразивних зерен, знімає з поверхні заготовки шар металу.
Мал. 6.23. Листи наждачного паперу з різною зернистістю (40, 80, 150, 240, 600).
Також для зачищення металу від іржі, зняття неглибоких подряпин, зачищення підгорілих контактів та при неможливості доставити оброблювану деталь до шліфувального круга виконують шліфування вручну наждачним папером (мал. 6.23). Залежно від необхідної чистоти оброблюваної поверхні використовують наждачний папір з певною величиною абразивного зерна, відповідно наждачний папір має номер зернистості. Чим більша цифра, тим менші частки абразивного матеріалу і, тим більша зернистість, відповідно чистіша обробка поверхні. Мал. 6.24. Насадки з наждачним папером до «болгарки» та електродрилі
Для механізації процесу шліфування наждачним папером використовують спеціальні насадки для «болгарки» або дрилі, до яких кріпиться наждачний папір на липучці або гайкою (мал. 6.24).
Механізація процесу обпилювання
Мал. 6.25. Обпилювальний станок і прийоми установки напилка: а – загальний вигляд станка, б – схема взаємного розташування напилка і заготовки на обпилювальному станку
1 – стійка, 2 – шток, 3 – нижній кронштейн, 4 – коробка швидкостей, 5 – ремінна передача, 6 – педалі, 7 – нижня частина корпуса, 8 – гвинт, 9 – підйомно-поворотний стіл, 10 – заготовка, 11 – притиски, 12 – напилок, 13 – патрон, 14 – верхній кронштейн
Види браку при обпилюванні
До видів браку, що найчастіше зустрічаються, при обпилюванні відносяться нерівності поверхні і завали країв заготовки. Ці дефекти – результат неправильного вибору напилка, а найчастіше – результат відсутності навиків обпилювання. Брак виходить також унаслідок слабкого або надмірного затиску в лещатах обпилюваної заготовки. При цьому з’являються вм’ятини і навіть може статися поломка заготовки.
Поширеним виглядом браку є неточність розмірів унаслідок неправильної розмітки, зняття зайвого або, навпаки, недостатнього шару металу, а також несправності вимірювального інструменту або невмілого користування ним.
Нерідко обпиляна поверхня виявляється подряпаною (задертою). Причиною такого браку є робота напилком, «засаленим» (забрудненим) стружкою.
Шабрення металу
Шабрення – операція завершальної обробки різанням поверхонь, яка полягає в знятті дуже тонких стружок металу шляхом зіскоблювання за допомогою ріжучого інструменту – шабера.
Мета цієї операції — забезпечити щільне прилягання спряжених поверхонь і герметичність з’єднання. Шабренням оброблюють прямолінійні та криволінійні поверхні. Його широко використовують в інструментальному виробництві як завершальний процес оброблення незагартованих поверхонь.
Широке застосування шабрення пояснюється особливими якостями отриманої поверхні:
– на відміну від шліфованої чи отриманої притиранням абразивами шабрена поверхня стійкіша до спрацювання, оскільки не має шаброваних в її пори залишків абразивних зерен, які прискорюють процес спрацювання;
– вона краще змочується і довше зберігає мастильні речовини завдяки наявності так званого розбиття цієї поверхні, що також підвищує її зносостійкість і знижує коефіцієнт тертя;
– шабрена поверхня дає змогу використовувати найпростіший і найдоступніший метод оцінки її якості за кількістю плям на одиницю площі. Шабрення дає можливість отримати точність оброблення поверхні від 0,003 до 0,01 мм; за один прохід шабером знімається шар металу завтовшки 0,005 — 0,07 мм.
Мал. 6.26. Шабери: а – плоский однобічний, б – з відігнутим кінцем, в – плоский двобічний, г – три- і чотиригранні
Шабери (мал. 6.26) є сталевими смугами або стержнями певної довжини з ретельно заточеними робочими гранями (кінцями). По конструкції шабери поділяються на цілісні і складені; за формою робочої частини – на плоскі, тригранні і фасонні, а по числу ріжучих кромок – на однобічні, що мають зазвичай дерев’яні рукоятки, і двосторонні без рукояток.
Окрім цілісних шаберів, останнім часом застосовують і змінні, складені, що складаються з державки і вставних пластин. Ріжучими лезами таких шаберів можуть служити пластинки інструментальної сталі, твердого сплаву і швидкорізальної сталі. Шабери не стандартизовані. Вони виготовляються з інструментальної вуглецевої сталі У10А і У12А з подальшим загартовуванням.
Плоскі шабери застосовують для шабрення плоских поверхонь — відкритих, пазів, канавок і т. д. їх виготовляють з прямими або відігнутими кінцями. Відкриті поверхні шабрять шаберами з прямими кінцями; стінки пазів, канавок, а також м’які метали (алюміній, цинк) — шаберами з відігнутими кінцями.
Технологічний процес шабрення передбачає підготовку оброблюваних поверхонь за допомогою перевірочних плит або лінійок.
Мал. 6.27. Фарбування поверхні під час шабрення: а – фарбування плити тампоном, б – переміщення деталі по плиті, в – фарбована деталь, г – переміщення плити по деталі
Підготовка до шабрення полягає у фарбуванні оброблюваної поверхні спеціальною фарбою (мал. 6.27), яку попередньо наносять на перевірочну плиту, а потім тертям — на оброблювану поверхню деталі .
Мал. 6.28. Прийоми шабрення плоских деталей: а – «від себе», б – «на себе», в – розміщених під кутом, г – при оздоблювальних операціях
Після цього деталь затискують у лещатах, використовуючи для цього губки з м’якого матеріалу (мідь, алюміній, латунь). Потім рухами шабера вперед і назад з довжиною робочого ходу шабера 10-15 мм знімають шар металу з пофарбованих місць (мал. 6.28). На завершення поверхню деталі очищують щіткою і ретельно витирають сухою чистою ганчіркою. Шабрення в різних напрямках чередують з перевіркою на контрольній плиті доти, доки вся оброблювана поверхня буде рівномірно зафарбована.
Штрихи від шабрення мають розміщуватися в шаховому порядку. Точність шабрення перевіряють за допомогою контрольної рамки (мал. 6.29) на трьох-чотирьох ділянках поверхні.
Шабрення закінчують з появою 12-16 плям фарби з рівномірним їх розподілом на внутрішній площі контрольної рамки розміром 25 х 25 мм. Залежно від точності шабери мають ширину: для грубою попереднього шабрення – 20-30 мм, для чистого шабрення – 10-15, для точного – 5-15 мм.
Мал. 6.29. Рамка (а) і контроль нею якості шабрення (б)
Притирання і доведення
Притирання є завершальною слюсарною операцією зі зняття тонкого шару металу з оброблюваних поверхонь абразивними порошками або пастами для отримання найщільнішого прилягання цих поверхонь.
Притирання здійснюють спеціальними інструментами – притирками. Притирки виготовляють. із м’якшого матеріалу, ніж оброблювана деталь, завдяки чому абразивні зерна вдавлюються в поверхню притирки й утримуються в ній, як невеликі різці у своєрідній оправі. Матеріалами для притирок є чавун, м’яка сталь і скло.
Поверхні, що підлягають притиранню і доведенню, потрібно попередньо обробити шліфуванням або шабренням.
Припуск на притирання становить 0,01 —0,02 мм.
Притирання широких поверхонь звичайно виконують на двох притиральних плитах (мал. 6.30).
Мал. 6.30. Плоскі притирки: а – з канавками, б – гладенька
Для попереднього притирання застосовують плити з канавками завглибшки і завширшки 1 мм, розміщеними одна від одної на відстані 10-15 мм, а для остаточного притирання використовують плити з гладенькою поверхнею. Як притиральні застосовують тверді абразивні матеріали у вигляді порошків (наждак, корунд, карборунд та ін.), а також притиральні пасти ГОІ. Пасти ГОІ порівняно з іншими шліфувальними матеріалами ефективніші і можуть застосовуватися для притирання як твердих, так і м’яких металів.
Для притирання (мал. 6.31) водночас із різними абразивними порошками застосовують різні змащувальні матеріали: для грубих і середніх порошків — гас, а для дрібних — машинне масло.
Завершальною стадією притирання поверхонь є доведення. Під час оброблення поверхонь доведенням отримують розміри з точністю до 0,01 мкм і дзеркальну поверхню. Припуск на доведення становить 1—2 мкм.
Мал. 6.31. Притирання плоских поверхонь: а – попереднє, б – кінцеве
Для попереднього й остаточного доведення застосовують ті самі абразивні порошки і пасти, як і для притирання. Для отримання дзеркальної поверхні використовують тонку пасту
ГОИ, а також оксид хрому або алюмінієву пудру, розчинені в бензині.
Після притирання і доведення контролюють поверхню на прямолінійність лінійкою зі щупом, паралельність площин — індикатором, перевірку зазору між паралельними площинами — мікрометром (див. урок №8).
Притирання і доведення деталей, що мають циліндричну форму, виконують на токарних верстатах, де швидкість обертання деталі не повинна перевищувати 6—10 м/хв. Для притирання використовують або плоску притирку, або притирку-кільце з регульованим внутрішнім діаметром.
Притирання і доведення закінчують, досягнувши на валику чистої дзеркальної поверхні, яку перевіряють мікрометром на овальність, конусоподібність і бочкоподібність.
Механізація процесів шабрення і притирання
Мал. 6.32. Пневматичний шабер: а – влаштування, б -прийоми роботи, 1 – штуцер, 2 – кришка ручки, 3 – золотникова коробка, 4 – шпилька, 5 – кришка двигуна, 6 – шток, 7 – патрон для закріплення шабера
Мал. 6.33. Електромеханічний шабер: 1 – електродвигун, 2 – візок, 3 – редуктор, 4 – гнучкий вал, 5 – кривошип, 6 – інструмент
Мал. 6.34. Станок для притирання
Обробка поверхонь методом полірування
Полірування — механічна або ручна чистова обробка виробів, що надає їхній поверхні високої чистоти і дзеркального блиску. Металеві вироби обробляють на
полірувальних верстатах, вдаються також до
електролітичної та електромеханічної обробки.
Полірування виконують після шліфування або гальванічного покриття. Завдяки поліруванню металу усуваються мікронерівності на поверхні виробу.
При ручному поліруванні пасту наносять на
повсть і нею роблять кругові рухи на поверхні виробу.
Механічне полірування виконують полірувальними кругами з повсті або бавовняних тканин, змазаних пастою. Вони приводяться в рух від електродвигунів із частотою обертання близько 2000 об/хв. Для механічного полірування використовують шкірки № 280 і № 325 і мікропорошки марок М-5, М-7, М-10, М-14, М-20, М-28 (цифри означають розмір зерен у мікрометрах).
Можна користуватися пастою
ГОИ № 1, 2 і 3 відповідно для грубого, середнього й тонкого полірування, а якщо її немає – зеленою художньою фарбою в тюбику «Окис хрому». Наждакову пасту застосовують для початкового полірування, крокусну – щоб підготувати поверхню для
гальванічного покриття, хромову й пасту
ГОИ № 1 і 2 – переважно для полірування виробів з
міді, нержавіючої
сталі, хромованих і
нікельованих поверхонь, вапняну й частково пасту
ГОИ № 2 – для полірування
кольорових металів.
Хромовою й пастою
ГОИ можна також полірувати м’які метали, проте, вапняна діє на них більш м’яко й додає блиску.
Полірують метал такими пастами, частин за масою:
Наждакова
Наждаковий пил……………………………35-45
Парафін……………………………………………10
Жир яловичий (тваринний комбіжир)…5
Масло мінеральне……………………………..1
Хромова
Окис хрому …………………………………….81
Стеарин…………………………………………..10
Жир яловичий (тваринний комбіжир) …5
Гас ………………………………………………….2
Крокусна
Крокус (окис заліза) ……………………..33-45
Олеїн ……………………………………………20
Стеарин …………………………………………5
Парафін…………………………………………5
Вапняна
Полірувальне вапно…………………..40-50
Стеарин ……………………………………..15
Олеин ………………………………………..10
Сірка в порошку ………………………….1
Для готування паст спочатку розтоплюють в одній посудині стеарин, віск, жир і інші речовини, потім старанно їх перемішують і додають полірувальний порошок. Після охолодження, але перед отвердінням, суміш заливають у форми або виливають на металеві аркуші.
Промисловість виготовляє повстяні полірувальні круги трьох типів: грубошерсті, напівгрубої вовни й тонкошерсті.
Мал. 6.35. Шліфувально-полірувальний верстат
На шпиндель полірувального верстата (мал. 6.35) надягають кілька таких кругів і здавлюють їх шайбами діаметром, що становить 1/3 діаметра кола. На круги наносять пасту, і деталь притискають до круга. Як правило, паста є твердою, тому, щоб нанести її на круг, необхідно притиснути пасту до круга, який обертається. Попередньо можна змочити пасту в бензині. Полірувальне коло повинно обертатися на працівника, деталь при цьому притискають нижче центра кола. Тоді паста з-під деталі відлітає долілиць, а у випадку виривання з рук деталь також упаде долілиць. Полірувати краще під кутом 90
0 до напрямку попереднього
шліфування.
Якщо полірують деталі з матеріалів різної твердості, то спочатку обробляють найбільш тверді поверхні, а потім — м’які. Щоб очистити забруднене коло, до його поверхні під кутом 900, але нижче центра, рукою легенько притискають штаб з гострою гранню.
Тканинні круги звичайно не чистять.
Безпека праці
Безпека праці при обпилюванні металу.
при обпилюванні заготовок з гострими кромками не можна притикати пальці лівої руки під напилок при зворотному ході;
утворену в процесі обпилювання стружку, необхідно змітати з верстата волсяною щіткою. Суворо заборонено скидати стружку голими руками, здувати її або видаляти стисненим повітрям;
при роботі слід користуватися лише напилками з міцно насадженими рукоятками; заборонено працювати напилками без рукояток або напилками з тріснутими, розколеними рукоятками.
При роботі на верстатах слід дотримуватись наступних правил безпеки праці: повинна бути виключена можливість захвату одягу рухомими частинами станка, заготовкою або різцем; затискні пристрої верстата повинні забезпечувати надійне закріплення заготовки; працюють в окулярах для захисту очей від попадання стружки; видаляють стружку лише щіткою, крючком або совком; не можна вимірювати деталі на працюючому станку; заборонено залишати працюючий станок без нагляду, робоче місце і проходи повинні бути чистими, не захаращеними матеріалами, пристосуваннями, готовими виробами та ін.
Безпека праці при шабруванні.
деталь, що обробляється, повинна бути надійно встановлена і міцно закріплена;
не допускається робота несправними шаберами (без ручок або з тріснутими ручками);
при виконанні робіт шліфувальними головками дотримуватись правил електробезпеки.
Безпека праці при притиранні і доведені.
В процесі виконання притирочних робіт необхідно поверхню, що обробляється, чистити не рукою, а ганчіркою (дрантям); користуватися захисними пристроями для відсмоктування абразивного пилу; обережно поводитися з пастами, так як вони містять кислоти; надійно і стійко встановлювати притири; дотримуватись техніки безпеки при роботі механізованим інструментом, а також на верстатах.





Немає коментарів:
Дописати коментар